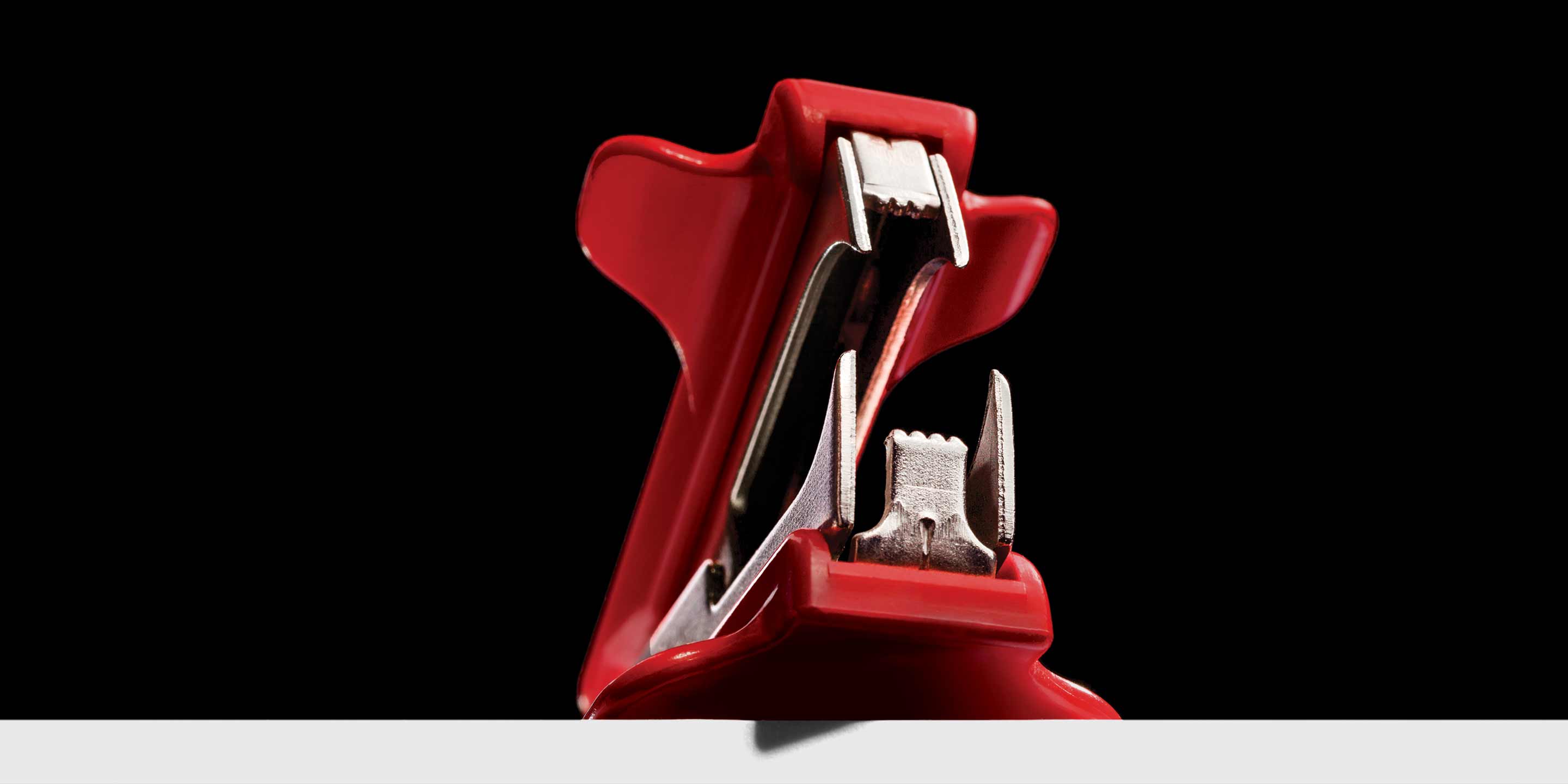
The hierarchy is a way to protect workers from dangers. It is widely accepted by many safety agencies and is commonly used in practice. It is taught to industry managers, who then implement it as a standard procedure. However, there are some variations of this system. For more information, see our guide to the NFPA70E hazard classification system. This information will help you to better apply the hierarchy in your workplace.
NFPA70E
NFPA 70E is a set of standards for electrical safety in the workplace. The 2018 edition includes a new Annex Q section that describes human performance, human error, as well as their potential negative consequences. This section also provides a hierarchy of control, which prioritizes the elimination of hazards. To eliminate electrical hazards, it is important to first remove the source of the energy or danger. Only as a last resort, personal protective equipment should not be used.
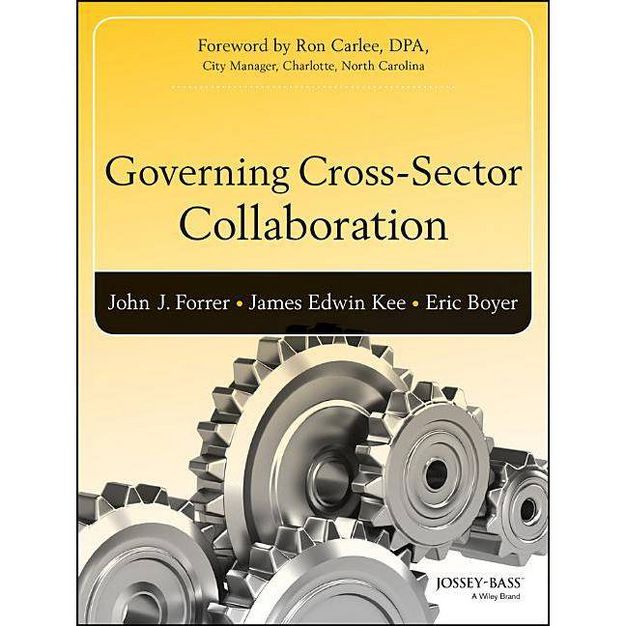
The next step in reducing the severity of risks is to assess the extent of your exposure. While engineering controls can reduce the amount of hazardous substances that are exposed, they cannot eliminate all hazards. The hierarchy of control's goal is to reduce the severity of hazards and prevent them from happening. A common example is an engineering control, such as a fog machine or ventilation system, or a fire alarm.
Appendices are also included in the NFPA 70E standard. These documents detail procedures and practices and provide guidance. Appendices provide sample forms, PPE guidance guidelines, design requirements, as well as risk assessment and guidelines. Annexes serve the same purpose as the main text. They provide guidance for how to implement standard. Sometimes, annexes may be used to provide additional information that can help ensure safety in a workplace or building.
Variation of ARECC
The ARECC variant in the hierarchy is a method to reduce the chance of being exposed to a given hazard. Although this system is a traditional one in the United States, Canada and other countries, it has been adapted to other countries. For example, some countries place isolation before engineering controls, while others combine both. The ARECC variant includes employee training and warnings. It is important to remember that warnings cannot eliminate all hazards at work.
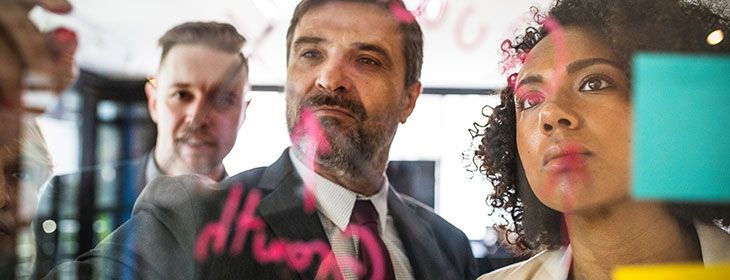
The ARECC hierarchy for controls is a framework to ensure occupational safety. It provides a framework for occupational safety and health. The hierarchy contains five categories of controls: engineering controls and administrative controls. Each category has its own specific strengths and weaknesses, and is important for a specific situation. Some controls in the ARECC hierarchy work better than others.
FAQ
What is a basic management tool used in decision-making?
A decision matrix is a simple but powerful tool for helping managers make decisions. It allows them to consider all possible solutions.
A decision matrix is a way to organize alternatives into rows and columns. This makes it easy for you to see how each option affects other options.
In this example, there are four possible options represented by boxes on the left-hand side of the matrix. Each box represents an alternative. The top row displays the current situation, and the bottom row shows what might happen if nothing is done.
The effect of choosing Option 1 can be seen in column middle. In this case, it would mean increasing sales from $2 million to $3 million.
These are the results of selecting Options 2 or 3. These are positive changes - they increase sales by $1 million and $500 thousand respectively. They also have negative consequences. Option 2 can increase costs by $100 million, while Option 3 can reduce profits by $200,000.
The final column shows results of choosing Option 4. This would result in a reduction of sales of $1 million.
A decision matrix has the advantage that you don’t have to remember where numbers belong. It's easy to see the cells and instantly know if any one of them is better than another.
The matrix already does all the work. It's as easy as comparing numbers in the appropriate cells.
Here is an example how you might use the decision matrix in your company.
You want to decide whether or not to invest more money into advertising. You'll be able increase your monthly revenue by $5000 if you do. You'll also have additional expenses up to $10,000.
The net result of advertising investment can be calculated by looking at the cell below that reads "Advertising." It is 15 thousand. Advertising is worth more than its cost.
How does Six Sigma work?
Six Sigma employs statistical analysis to identify problems, measure them and analyze root causes. Six Sigma also uses experience to correct problems.
The first step to solving the problem is to identify it.
Next, data is collected and analyzed to identify trends and patterns.
Then, corrective actions can be taken to resolve the problem.
Finally, data is reanalyzed to determine whether the problem has been eliminated.
This cycle continues until the problem is solved.
What are the key management skills?
Managerial skills are crucial for every business owner, regardless of whether they run a small store in their locality or a large corporation. They are the ability to manage people and finances, space, money, and other factors.
Management Skills are also needed when you're setting goals and objectives, planning strategies, leading teams, motivating employees, resolving problems, creating policies and procedures, and managing change.
There are so many managerial tasks!
What is Kaizen and how can it help you?
Kaizen is a Japanese term for "continuous improvement." It encourages employees constantly to look for ways that they can improve their work environment.
Kaizen is built on the belief that everyone should be able do their jobs well.
What does it mean to say "project management"
This refers to managing all activities that are involved in a project's execution.
We include defining the scope of the project, identifying the requirements, preparing the budget, organizing the project team, scheduling the work, monitoring progress, evaluating results, and closing down the project.
How to effectively manage employees
The key to effective management of employees is ensuring their happiness and productivity.
It is important to set clear expectations about their behavior and keep track of their performance.
To do this successfully, managers need to set clear goals for themselves and for their teams.
They must communicate clearly with their staff. They need to communicate clearly with their staff.
They will also need to keep records about their team's activities. These include:
-
What did we accomplish?
-
How much work were you able to accomplish?
-
Who did it and why?
-
When it was done?
-
Why?
This information can help you monitor your performance and to evaluate your results.
What is the difference between Six Sigma Six Sigma and TQM?
The key difference between the two quality management tools is that while six-sigma focuses its efforts on eliminating defects, total quality management (TQM), focuses more on improving processes and reducing cost.
Six Sigma stands for continuous improvement. It emphasizes the elimination or minimization of defects through statistical methods such control charts and p charts.
This method seeks to decrease variation in product output. This is done by identifying root causes and rectifying them.
Total quality management is the measurement and monitoring of all aspects within an organization. This includes training employees to improve their performance.
It is often used as a strategy to increase productivity.
Statistics
- Your choice in Step 5 may very likely be the same or similar to the alternative you placed at the top of your list at the end of Step 4. (umassd.edu)
- Hire the top business lawyers and save up to 60% on legal fees (upcounsel.com)
- This field is expected to grow about 7% by 2028, a bit faster than the national average for job growth. (wgu.edu)
- The profession is expected to grow 7% by 2028, a bit faster than the national average. (wgu.edu)
- UpCounsel accepts only the top 5 percent of lawyers on its site. (upcounsel.com)
External Links
How To
How can you implement the Kaizen technique?
Kaizen means continuous improvement. The term was coined in the 1950s at Toyota Motor Corporation and refers to the Japanese philosophy emphasizing constant improvement through small incremental changes. It's a team effort to continuously improve processes.
Kaizen, a Lean Manufacturing method, is one of its most powerful. In this concept, employees who are responsible for the production line must identify problems that exist during the manufacturing process and try to solve them before they become big issues. This increases the quality of products and reduces the cost.
Kaizen is a way to raise awareness about what's happening around you. It is important to correct any problems immediately if they are discovered. It is important that employees report any problems they see while on the job to their managers.
There are some basic principles that we follow when doing kaizen. We always start from the end product and move toward the beginning. To improve our factory, for example, we need to fix the machines that produce the final product. We then fix the machines producing components, and the machines producing raw materials. Finally, we repair the workers who are directly involved with these machines.
This method is known as kaizen because it focuses upon improving every aspect of the process step by step. After we're done with the factory, it's time to go back and fix the problem.
How to measure kaizen's effectiveness in your business is essential to implement it. There are many ways you can determine if kaizen has been implemented well. Another way to determine if kaizen is working well is to look at the quality of the products. Another way is determining how much productivity increased after implementing kaizen.
To determine if kaizen is effective, you should ask yourself why you chose to implement kaizen. Was it just because it was the law or because you wanted to save money? Did you really believe it would lead to success?
Let's say you answered yes or all of these questions. Congratulations! You are now ready to begin kaizen.