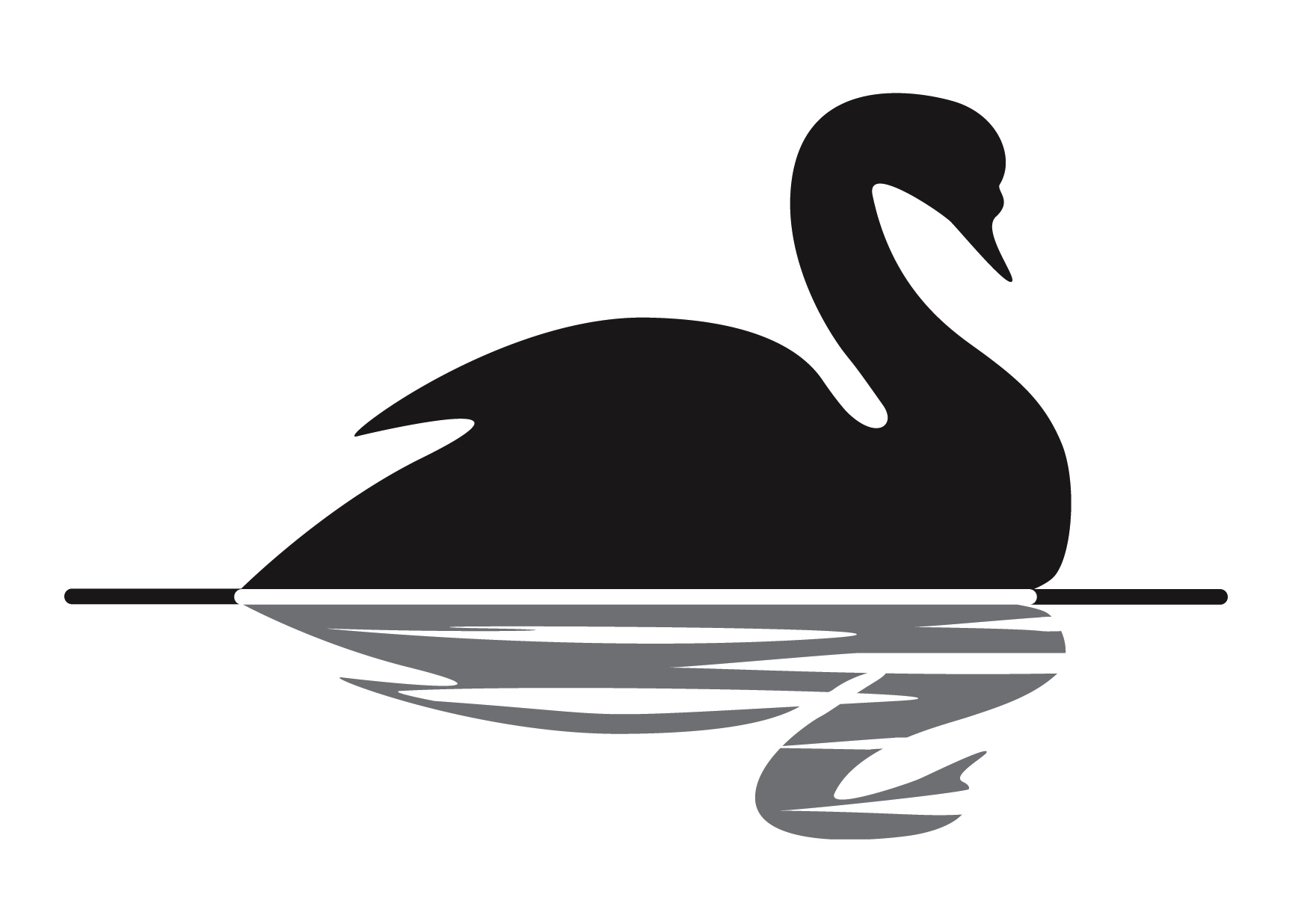
As a middle manger, you will have to lead the line and special manager teams. Some middle managers are directly or indirectly responsible to junior staff for their productivity and performance. As such, you'll need to be able and confident in interpersonal communication.
Becoming a good middle manager
To be a mid-manager requires special skills. Middle management requires the ability to balance the demands of higher and lower-level management. Additionally, it involves managing multiple departments' responsibilities. The middle managers must be skilled in communication, leadership and problem solving.
The biggest challenge middle managers face when managing people is onboarding new employees. Middle managers have to deal with a myriad of tasks from onboarding new employees to submitting requests for new team tools. It takes them time and drains their energy. If they are unable to see the line, they could alienate sections of the company.
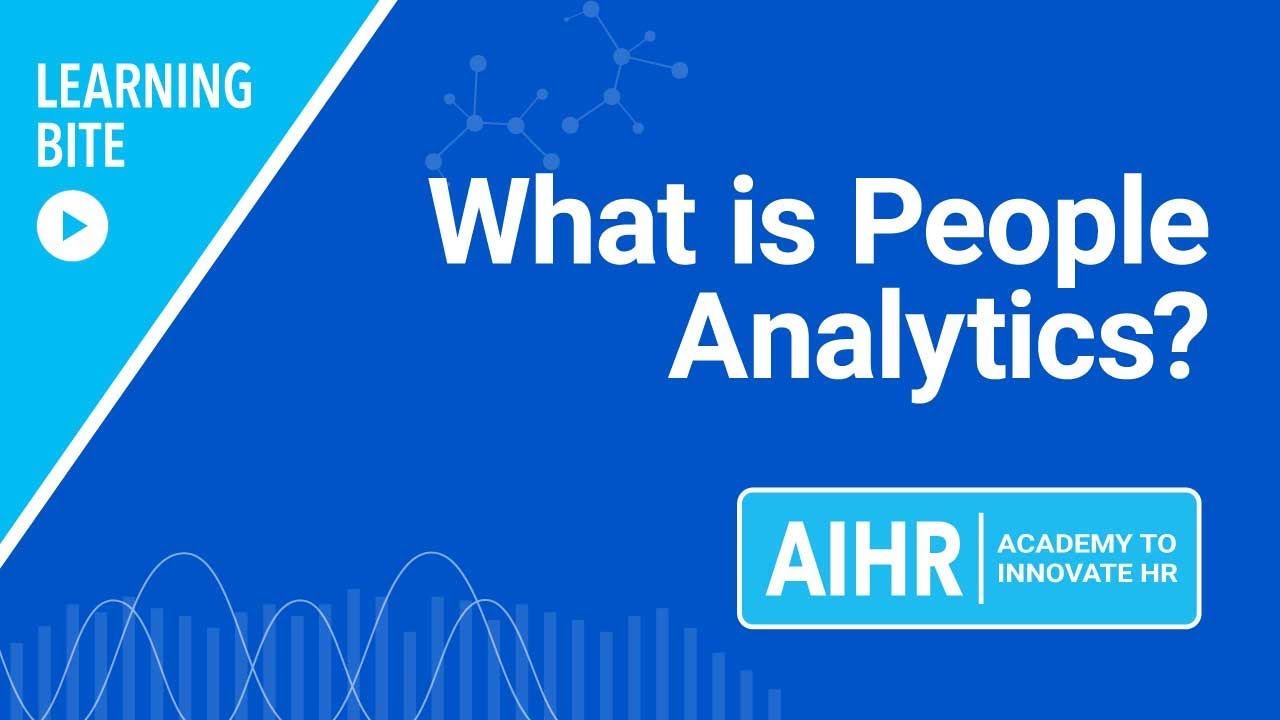
A second challenge for middle managers is the internalization of their team's challenges. It can adversely affect their well-being so it is important to have someone objective and impartial to help them process their thoughts. This process is critical as it determines whether the new hire will fit in with the culture of the company and their team. This will help you assess potential candidates' future abilities and their impact on your team. Potential performance can be analyzed through skills assessments and behavioral interviews.
Communication skills
It is crucial to develop your communication skills as middle managers. You will interact with employees and senior managers in this role. You need to be able respond to all situations, even those that are conflict- or confrontational. Effective communication and managing employee reactions to change is key to leading a team. By improving your communication skills as a middle manager, you can improve your influence, productivity, and engagement.
For middle managers to communicate effectively with senior managers, they need to be able provide reports that are accurate and complete. They also must provide an open channel for employees to discuss problems and ask for help. Also, middle managers are often responsible in bringing projects to completion. It is their responsibility to ensure that employees know the importance and value of the work they do.
In an organization, power dynamics
Power dynamics play an important role in the organization of middle manager. However, the most effective way to mitigate power dynamics is by setting clear roles for people. This will keep energy levels in check and help the team focus on its overall goal. Laura Handrick (workplace analyst) points out that a power struggle could lead to a team losing sight of its overall objective.
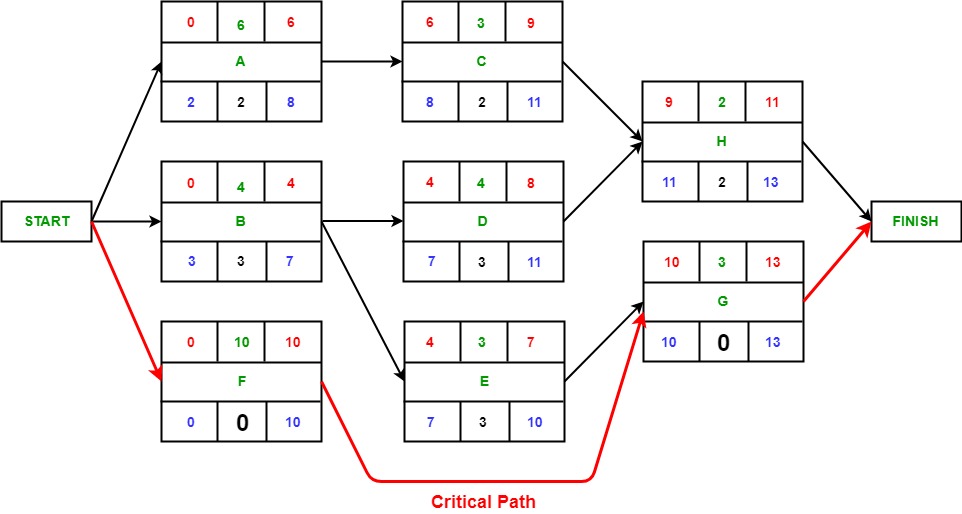
Power dynamics is the unwritten rules that guide how people interact with each others in the workplace. There are many different ways that people can interact with each other. People desire to be in control of large projects and to have the ability to make decisions. Power dynamics puts employees in direct competition.
It is important to remember that power dynamics in an organization are often harmful to the organization's interest. In the Sears catalog case, for example, the all-powerful employee's preferences might not be in line with the company's best interests. A manager should be careful not to allow power relationships to develop in such cases. It is possible to end power relationships by not keeping promises from the past, but it comes with a price.
FAQ
What is Kaizen?
Kaizen refers to a Japanese term that stands for "continuous improvements." It is a philosophy which encourages employees in continuously improving their work environment.
Kaizen is a belief that everyone should have the ability to do their job well.
What kind people use Six Sigma?
Six Sigma will most likely be familiar to people who have worked in statistics and operations research. However, anyone involved in any aspect of business can benefit from using it.
Because it requires a high level of commitment, only those with strong leadership skills will make an effort necessary to implement it successfully.
Six Sigma is so well-known.
Six Sigma is easy and can deliver significant results. Six Sigma also gives companies a framework for measuring improvement and helps them focus on what is most important.
What are the key management skills?
Management skills are essential for any business owner, whether they're running a small local store or an international corporation. They are the ability to manage people and finances, space, money, and other factors.
You will need management skills to set goals and objectives, plan strategies, motivate employees, resolve problems, create policies and procedures, and manage change.
As you can see, there are many managerial responsibilities!
What role should a manager play within a company
Different industries have different roles for managers.
In general, a manager controls the day-to-day operations of a company.
He/she is responsible for ensuring that the company meets all its financial obligations and produces the goods or services customers want.
He/she is responsible for ensuring that employees comply with all regulations and follow quality standards.
He/she oversees marketing campaigns and plans new products.
Why is it so hard to make smart business decisions?
Complex systems and many moving parts make up businesses. It is difficult for people in charge of businesses to manage multiple priorities simultaneously and also deal with uncertainty.
Understanding the impact of these factors on the system is crucial to making sound decisions.
To do this, you must think carefully about what each part of the system does and why. It's important to also consider how they interact with each other.
You should also ask yourself if there are any hidden assumptions behind how you've been doing things. If so, it might be worth reexamining them.
You can always ask someone for help if you still have questions after all of this. They may see things differently from you and have insights that could help you find a solution.
Statistics
- Your choice in Step 5 may very likely be the same or similar to the alternative you placed at the top of your list at the end of Step 4. (umassd.edu)
- 100% of the courses are offered online, and no campus visits are required — a big time-saver for you. (online.uc.edu)
- UpCounsel accepts only the top 5 percent of lawyers on its site. (upcounsel.com)
- The BLS says that financial services jobs like banking are expected to grow 4% by 2030, about as fast as the national average. (wgu.edu)
- The average salary for financial advisors in 2021 is around $60,000 per year, with the top 10% of the profession making more than $111,000 per year. (wgu.edu)
External Links
How To
What is Lean Manufacturing?
Lean Manufacturing methods are used to reduce waste through structured processes. They were created by Toyota Motor Corporation in Japan in the 1980s. The primary goal was to make products with lower costs and maintain high quality. Lean manufacturing emphasizes removing unnecessary steps from the production process. It consists of five basic elements: pull systems, continuous improvement, just-in-time, kaizen (continuous change), and 5S. Pull systems involve producing only what the customer wants without any extra work. Continuous improvement is the continuous improvement of existing processes. Just-in–time refers when components or materials are delivered immediately to their intended destination. Kaizen is continuous improvement. This can be achieved by making small, incremental changes every day. Fifth, the 5S stand for sort, set up in order to shine, standardize, maintain, and standardize. To achieve the best results, these five elements must be used together.
Lean Production System
Six key concepts are the basis of lean production:
-
Flow - The focus is on moving information and material as close as possible to customers.
-
Value stream mapping- This allows you to break down each step of a process and create a flowchart detailing the entire process.
-
Five S's - Sort, Set In Order, Shine, Standardize, and Sustain;
-
Kanban - visual cues such as stickers or colored tape can be used to track inventory.
-
Theory of constraints: Identify bottlenecks and use lean tools such as kanban boards to eliminate them.
-
Just-in Time - Send components and material directly to the point-of-use;
-
Continuous improvement - incremental improvements are made to the process, not a complete overhaul.