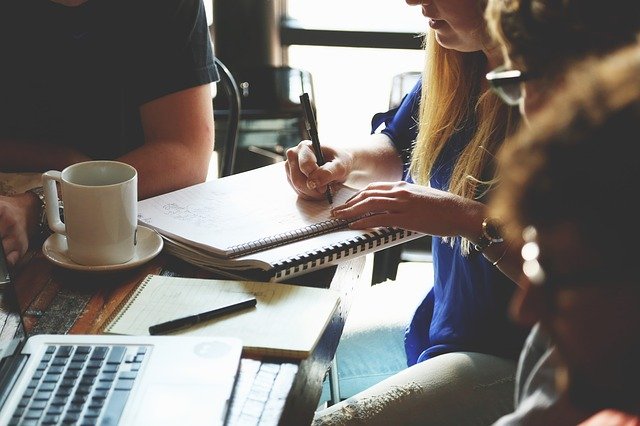
A certificate program in building management can help you be a leader of the construction industry. Its innovative curriculum gives students a range of skills that are essential in today's fast-paced business. Construction law, scheduling and BIM are all topics that students can study. The program will also help them build strong leadership and interpersonal skills. A construction management certificate will help you start your own business, or work for an established construction company.
Coursework
This course is intended to improve the skills of construction managers. It covers topics such as project planning, scheduling, budgeting, manpower allocation, and code compliance. The course also covers topics like the critical path method, scheduling tools, and other relevant topics. Students will also learn the importance of Cash flow diagrams. If one is interested in working as a contractor, this course will be a must.
A student must complete all courses within four years of admittance to the U of M in order to be awarded a construction manager certificate. The student must have a minimum grade of C or a cumulative GPA of 2.50. The certificate can be earned concurrently with an undergraduate degree. The program is open to individuals who have previous experience in the building industry. However, applicants must be admitted to this program as soon possible.
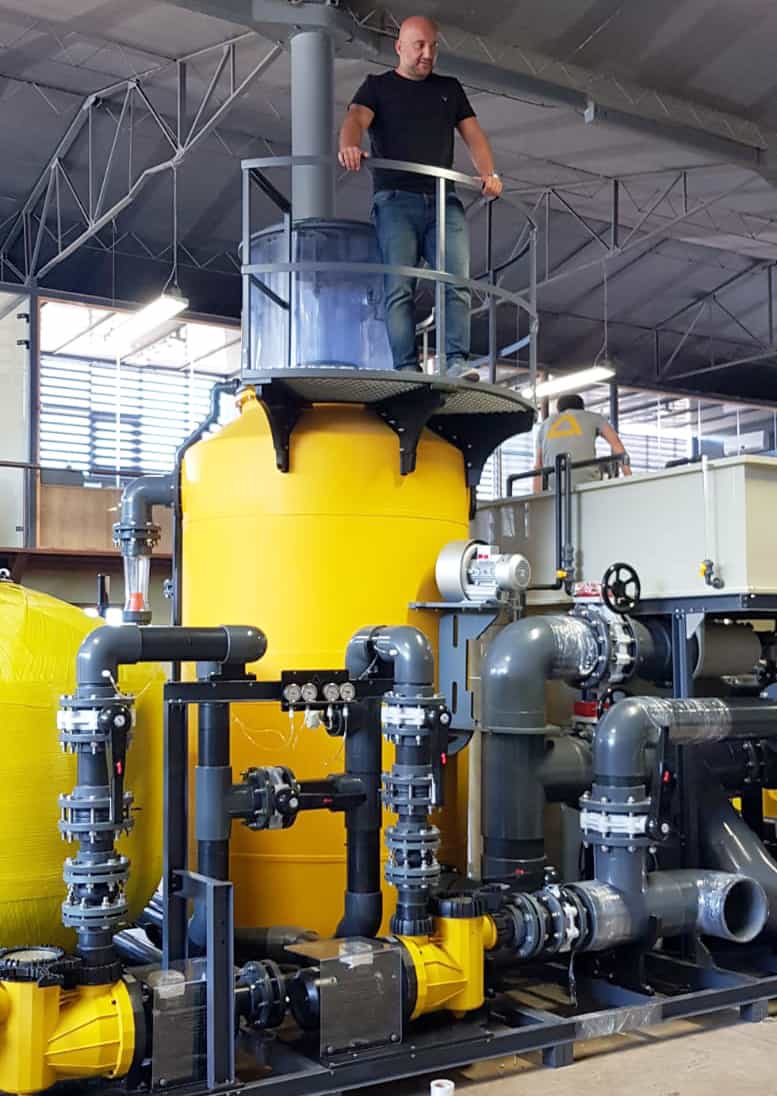
Credentials
A certificate in construction management is an important credential that you can have if you want to work in construction. Having this certification shows potential employers that you are serious about your future in this field. This certification is a professional advantage for those looking to start a business or work as a freelancer in this field. Credentials for construction management certificate are available from various colleges and universities. It is a constantly evolving industry and highly desired skills.
Construction certifications have many benefits for all those involved in the construction industry. These programs can improve the professional practices of each individual, as well as the brand and quality of the workers' services. They also demonstrate that a worker is highly skilled and understands the construction industry. This certification will allow you to earn a higher rate of pay for your services. A certification in construction is a great way for you to stand out.
Requirements
While a certificate in construction management does not guarantee employment, it can help you improve your job prospects. Students who complete certificate programs typically acquire knowledge in project delivery and building information modeling. Certificate programs are usually two-year long and do not require additional coursework. It will help you grow your career by proving your expertise in the field. It is not necessary to be an industry expert to earn a certificate.
A certificate that is exam-like is also possible. This type of certificate is available for between $500 to $1,100. You will need to pass a final examination. The cost of the certificate is payable once you pass the exam. You will need to meet certain requirements in order to earn a certificate. This depends on your education and background. You should learn as much as you can about each option before making a decision to pursue one.
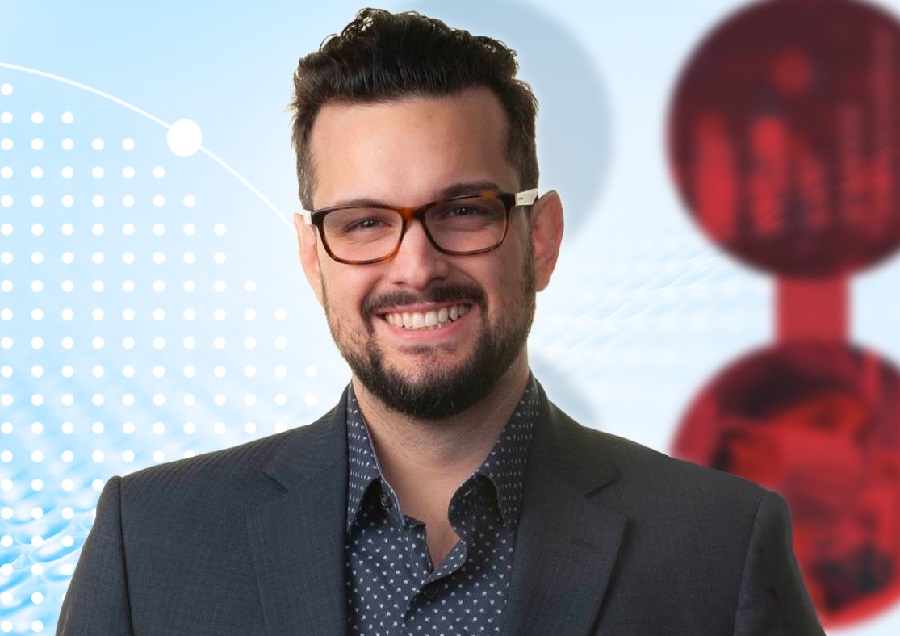
Online programs
A certificate in construction management can be earned online, which will help you stand out among other job candidates. This certificate allows you to show employers that you are capable of taking on a high-level role in a construction company. Ashworth College offers online certificates in construction management at affordable tuition rates. The links below will take you to more information about the program. We hope this information proves useful. Construction is highly competitive. Earning your online certificate in construction management will help you get that job.
A construction management certificate allows you to become more effective in supervising employees and coordinating projects. This course provides cutting-edge knowledge in project management and scheduling, BIM construction law, as well as green building practices. It also promotes leadership and interpersonal skills. This program is great for people who are interested in a career in construction but don't have enough time or education.
FAQ
What is Six Sigma?
It's an approach to quality improvement that emphasizes customer service and continuous learning. The goal is to eliminate defects by using statistical techniques.
Motorola invented Six Sigma in 1986 as part its efforts to improve manufacturing.
The idea spread quickly in the industry. Today many organizations use six-sigma techniques to improve product design.
How can a manager enhance his/her leadership skills?
Good management skills are essential for success.
Managers must continuously monitor the performance levels of their subordinates.
You must act quickly if you notice that your subordinate isn’t performing to their standards.
It is essential to know what areas need to be improved and how to do it.
What are the five management processes?
These five stages are: planning, execution monitoring, review and evaluation.
Planning means setting goals for the long-term. This includes setting goals for the future and defining what you want.
Execution takes place when you actually implement the plans. These plans must be adhered to by everyone.
Monitoring allows you to monitor your progress towards achieving your goals. This should involve regular reviews of performance against targets and budgets.
Review events take place at each year's end. They give you an opportunity to review the year and assess how it went. If not there are changes that can be made to improve the performance next year.
After the annual review is complete, evaluations are conducted. It helps identify which aspects worked well and which didn't. It also provides feedback on the performance of people.
What is Kaizen and how can it help you?
Kaizen is a Japanese term which means "continuous improvement." This philosophy encourages employees to continually look for ways to improve the work environment.
Kaizen is based on the belief that every person should be able to do his or her job well.
How does Six Sigma work?
Six Sigma uses statistical analysis for problems to be found, measured, analyzed root causes, corrected, and learned from.
The first step to solving the problem is to identify it.
The data is then analyzed and collected to identify trends.
The problem is then rectified.
The data are then reanalyzed to see if the problem is solved.
This cycle continues until there is a solution.
Statistics
- As of 2020, personal bankers or tellers make an average of $32,620 per year, according to the BLS. (wgu.edu)
- This field is expected to grow about 7% by 2028, a bit faster than the national average for job growth. (wgu.edu)
- The BLS says that financial services jobs like banking are expected to grow 4% by 2030, about as fast as the national average. (wgu.edu)
- Your choice in Step 5 may very likely be the same or similar to the alternative you placed at the top of your list at the end of Step 4. (umassd.edu)
- The average salary for financial advisors in 2021 is around $60,000 per year, with the top 10% of the profession making more than $111,000 per year. (wgu.edu)
External Links
How To
How do you do the Kaizen method?
Kaizen means continuous improvement. The Japanese philosophy emphasizes small, incremental improvements to achieve continuous improvement. This term was created by Toyota Motor Corporation in 1950. This is a collaborative process in which people work together to improve their processes continually.
Kaizen, a Lean Manufacturing method, is one of its most powerful. The concept involves employees responsible for manufacturing identifying problems and trying to fix them before they become serious issues. This increases the quality of products and reduces the cost.
Kaizen is the idea that every worker should be aware of what is going on around them. So that there is no problem, you should immediately correct it if something goes wrong. Report any problem you see at work to your manager.
When doing kaizen, there are some principles we must follow. When working with kaizen, we always start with the end result and move towards the beginning. We can improve the factory by first fixing the machines that make it. Then, we fix the machines that produce components and then the ones that produce raw materials. We then fix the workers that work with those machines.
This approach is called 'kaizen' because it focuses on improving everything steps by step. When we are done fixing the whole factory, we go back to the beginning and continue until we reach perfection.
You need to know how to measure the effectiveness of kaizen within your business. There are several ways that you can tell if your kaizen system is working. Another way to determine if kaizen is working well is to look at the quality of the products. Another way is to check how much productivity has grown since kaizen was implemented.
You can also find out if kaizen works by asking yourself why you decided to implement it. Is it because the law required it or because you want to save money. You really believed it would make you successful?
Congratulations if you answered "yes" to any of the questions. You are now ready to begin kaizen.