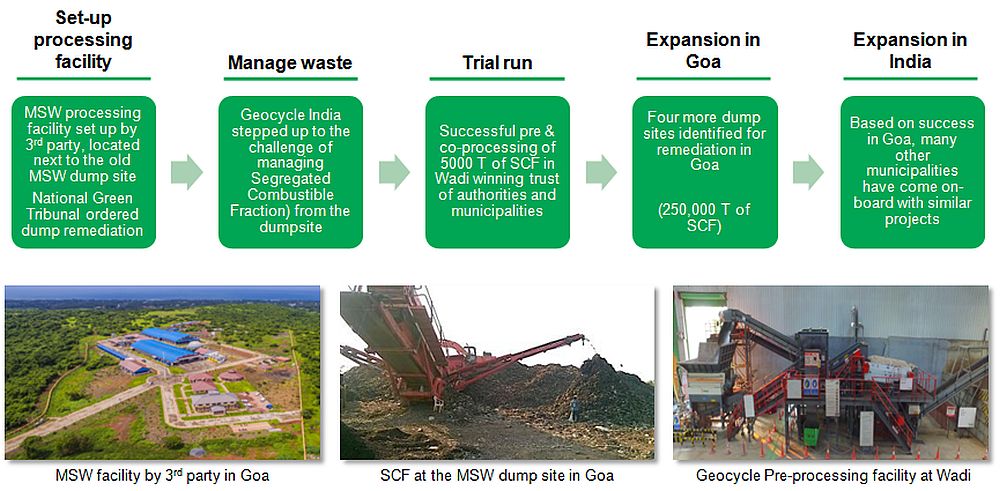
Demand planning assists businesses to plan their supply chains and manage sales. The goal is to reduce costs while improving service levels. It involves three components: inventory management, sales forecasting, and supply chain management. It can be an invaluable tool for businesses to improve their planning and can even help reduce inventory.
Demand planning is a combination of sales forecasting, inventory management and supply chain management
Demand planning is a crucial component of supply chain management and involves the systematic study of customer demand and inventory levels. It involves the analysis of a number of factors, including seasonal shifts. Economic conditions. And environmental changes. When done correctly demand planning will help retailers stay competitive while taking advantage of sales opportunities. Additionally, it helps retailers allocate resources more efficiently and make adjustments in real time. To accurately forecast demand, it is necessary to have a lot of data. Retailers must have the infrastructure and tools to collect and analyze this data.
To develop a demand strategy, you need to collect data from all departments and monitor market changes. In order for success, demand management must be integrated with supply chains management, inventory management, or other processes.
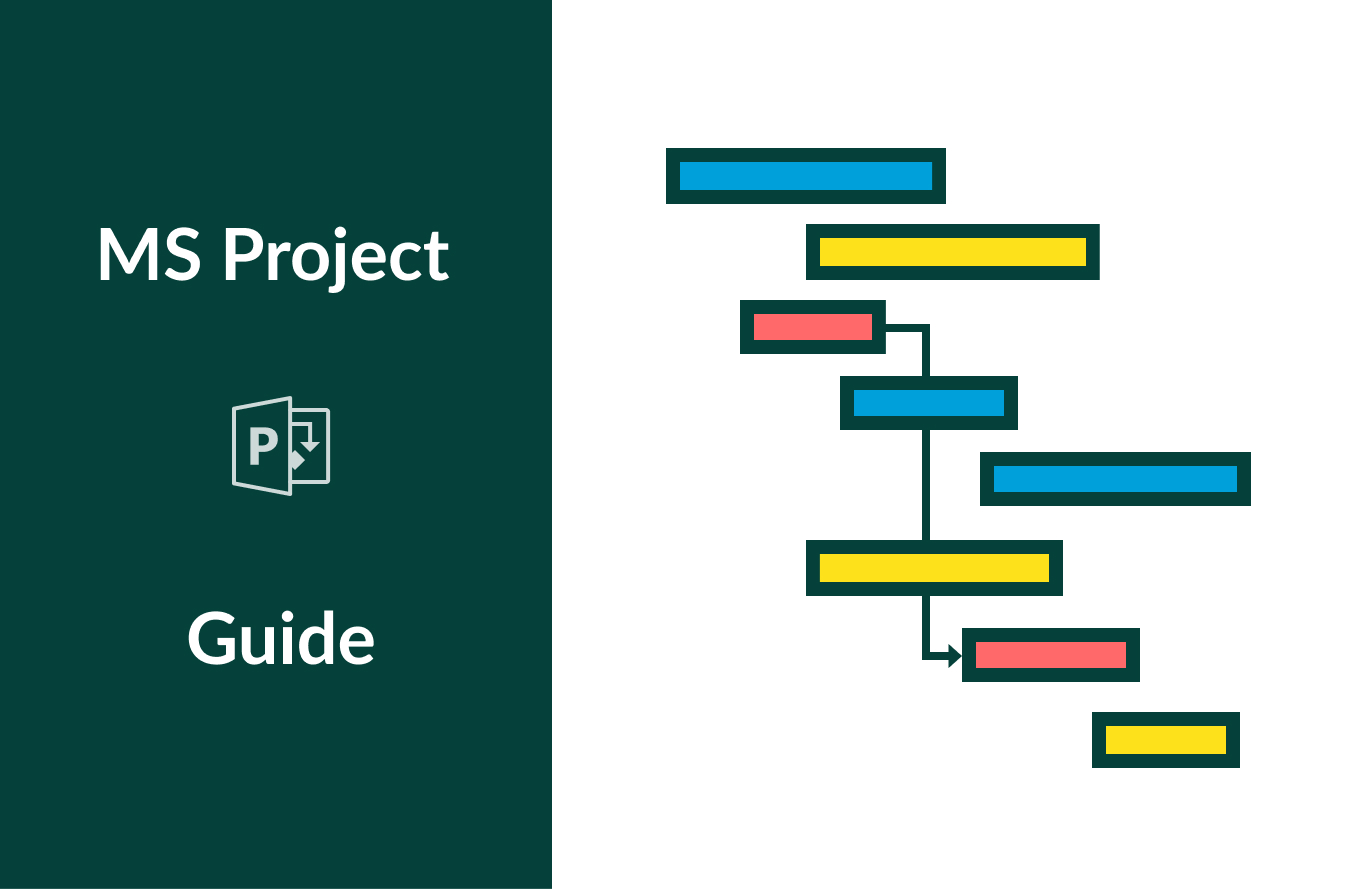
It makes it easier for companies to plan their operations.
Businesses need to plan their demand in order to maintain a balance between stock levels and customer demand. This requires coordination throughout the entire organization. Inventory that is not needed can result in lower revenue and higher inventory costs. It also increases the risk of obsolete or low-value inventory. Poor demand planning can cause supply chain disruptions, stockouts and costly scrambles to find raw materials. This can result in dissatisfied clients.
Companies need to analyze and collect data on past sales, seasonality, customer trends and other factors in order to properly plan their demand. This information, together with inventory management data, can be used to predict future demand and help make purchase decisions.
It lowers your costs
Cost cutting can be achieved by demand planning. It can reduce production costs and save money on warehousing. Companies can also keep inventory levels lower by having fewer items in stock. How to implement demand planning in your company. Don't overlook the importance of communication.
Demand planning is essential to find the right balance between inventory and customer demands. This requires coordination from all levels of your company. Excess inventory can cause your company to lose working capital and increase inventory cost. It could also lead your company to have low-value inventory, or even obsolete products. Poor planning can also result in disruptions to the supply chain, stockouts, and costly scrambles just to get raw materials. This can lead to customer dissatisfaction and even cause delays.
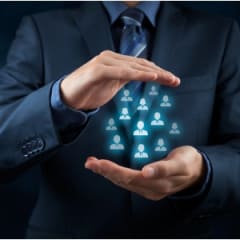
It increases service levels
The key to helping retailers meet consumer demand is to plan for the demand. By considering the types and quantities of the products that are expected, demand planning helps retailers manage inventory, purchasing, and storage processes. It also helps with forecasting, as it indicates how many stock is needed for a particular product. Once a company has established a process for planning demand, it is possible to use that information to guide sales or operations planning.
FAQ
What is the difference between a project and a program?
A program is permanent, whereas a project is temporary.
A project usually has a specific goal and deadline.
It is usually done by a group that reports back to another person.
A program is usually defined by a set or goals.
It is often done by one person.
What is Kaizen?
Kaizen, a Japanese term that means "continuous improvement," is a philosophy that encourages employees and other workers to continuously improve their work environment.
Kaizen is a belief that everyone should have the ability to do their job well.
How does Six Sigma work?
Six Sigma uses statistical analyses to locate problems, measure them, analyze root cause, fix problems and learn from the experience.
The first step in solving a problem is to identify it.
The data is then analyzed and collected to identify trends.
The problem can then be fixed by taking corrective measures.
Finally, data is reanalyzed to determine whether the problem has been eliminated.
This continues until you solve the problem.
Statistics
- UpCounsel accepts only the top 5 percent of lawyers on its site. (upcounsel.com)
- The BLS says that financial services jobs like banking are expected to grow 4% by 2030, about as fast as the national average. (wgu.edu)
- Hire the top business lawyers and save up to 60% on legal fees (upcounsel.com)
- 100% of the courses are offered online, and no campus visits are required — a big time-saver for you. (online.uc.edu)
- The profession is expected to grow 7% by 2028, a bit faster than the national average. (wgu.edu)
External Links
How To
How do I get my Six Sigma license?
Six Sigma is a quality management tool to improve processes and increase efficiency. It's a system that allows companies to get consistent results from operations. The name derives its meaning from the "sigmas" Greek word, which is composed of two letters that mean six. Motorola was the first to develop this process. Motorola recognized that they had to standardize their manufacturing processes to produce faster and more affordable products. Due to the different workers involved, there was a lack of consistency. To resolve this issue, they used statistical tools like Pareto analysis and control charts. Then they would apply the techniques to all parts of the operation. This would allow them to make any necessary changes. The Six Sigma certification process involves three major steps. The first step is to find out if you're qualified. You will need to complete some classes before you can start taking the tests. Once you've passed those classes, you'll start taking the tests. You'll want to study everything you learned during the class beforehand. Next, you'll be ready for the test. You will be certified if you pass the test. Final, your certifications can be added to you resume.