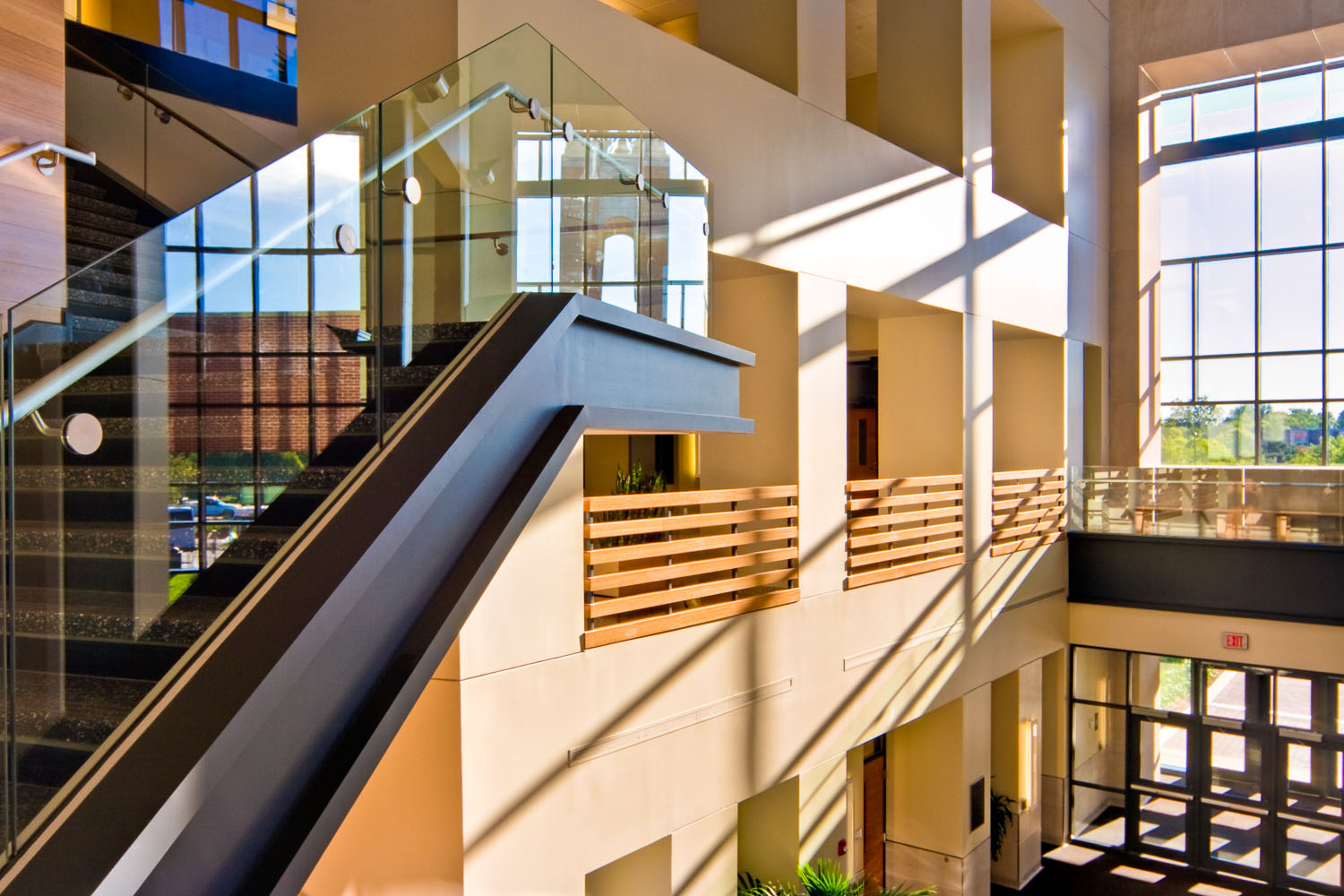
Before you can determine the acceptable level of risk for your organization, it is necessary to first identify what that level is. Then you must reduce that risk to an acceptable limit. This must be an ongoing process. It must also be balanced. If a risk can be tolerated, then no further actions or control steps are required. However, if the risk is too high, you must take further control measures or actions. This is known as risk management.
Precautionary principle
Precautionary Principle is an idea that promotes the prevention, detection and treatment of all types of harm. This principle is used to guide government policy and to develop specific laws. Although it is not without its critics, the principle has received significant international support. It emphasizes certain aspects of good decisionmaking that are often overlooked in both practice and formal decision theory. It also gives guidelines for formulating decisions problems. It focuses on costs and benefits in order to minimize harm.
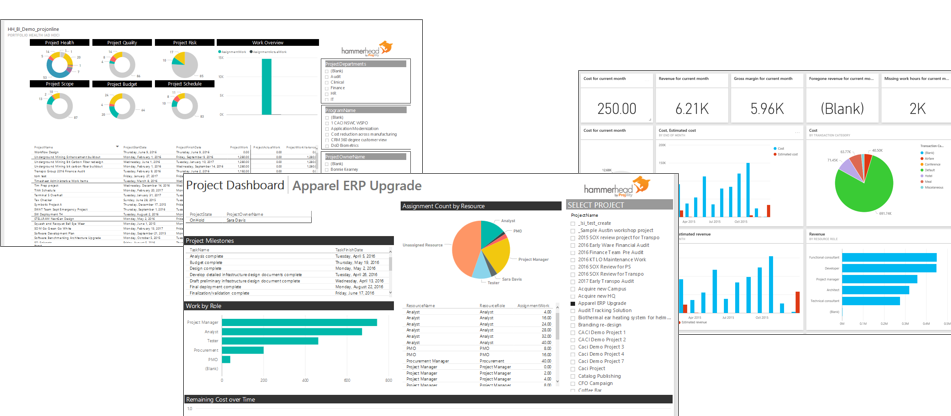
Duplication
Duplication and controlling risk are two important elements of a risk management plan. Duplication involves the creation of backups and spares of an item or process. These items are not used if the primary item becomes damaged or destroyed. A police department might have a backup car or an emergency operation center. The goal of the duplication effort, while reducing potential losses, may lead to lower efficiency.
Monitoring
The first step in monitoring and controlling risk is to identify the risks and create a plan that will manage them. The monitoring phase evaluates the effect of the plan and its impact on the risks. In some cases, monitoring may occur without a formal plan. For example, a team of risk managers may discuss weather concerns while deciding the best course. This is why the monitoring process becomes so important. This will ensure that risks are managed and allow for the team's monitoring of new risks.
You should choose the control that minimizes or eliminates any hazard.
There are many ways to reduce hazards and risk. Controls that reduce the risk and eliminate the hazard are most effective. Personal protective equipment and administrative controls are two other options. There are a number of controls that can be used to control a specific hazard. The best one is the one that eliminates the risk. You can combine some controls with others. The best combination depends on the situation. It is also important to consider the cost of each control.
Prices
A company's financial analysis should include the cost of managing risks. Each financial period is assigned a cost that is calculated annually and must be returned by the company. Companies give a portion to their risk management department. It is charged with managing the risks and identifying them. The employees of the Risk Management Department are charged with determining which risk is most expensive and how they can best be managed.
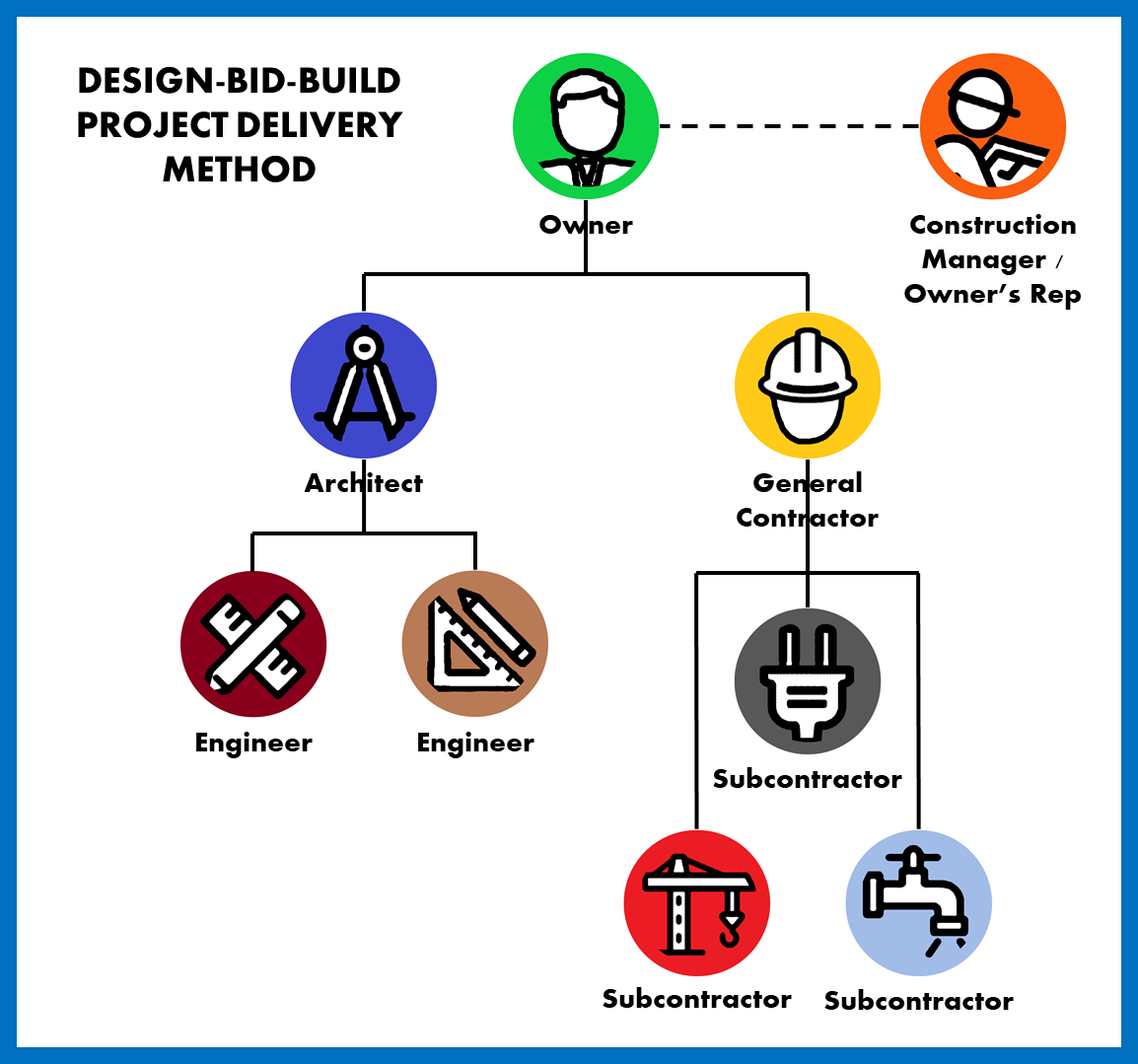
Internal control system
A solid internal control system will reduce risk, increase process performance, and protect against fraud. Internal and external communication is essential for effective internal control. This means that employees should know the goals, responsibilities, expectations, and limitations of internal control activities. It is important to ensure that internal controls are implemented consistently. Communication is key to ensuring that business owners and managers are accountable across departments and business units. It will increase confidence in the financial statements of an organization.
FAQ
What are the steps involved in making a decision in management?
Managers have to make complex decisions. It involves many factors, such as analysis and strategy, planning, execution, measurement, evaluation, feedback etc.
When managing people, the most important thing to remember is that they are just human beings like you and make mistakes. You are always capable of improving yourself, and there's always room for improvement.
This video will explain how decision-making works in Management. We will discuss the various types of decisions, and why they are so important. Every manager should be able to make them. You'll learn about the following topics:
Why is it important that companies use project management methods?
Project management techniques can be used to ensure smooth project execution and meeting deadlines.
This is due to the fact that most businesses rely heavily upon project work in order to produce goods, and services.
These projects require companies to be efficient and effective managers.
Companies that do not manage their projects effectively risk losing time, money, or reputation.
What are the five management processes?
The five stages of any business are planning, execution, monitoring, review, and evaluation.
Planning is about setting goals for your future. Planning includes setting goals for the future.
Execution takes place when you actually implement the plans. You need to make sure they're followed by everyone involved.
Monitoring is checking on progress towards achieving your objectives. Regular reviews of performance against budgets and targets should be part of this process.
At the end of every year, reviews take place. They provide an opportunity to assess whether everything went well during the year. If not then, you can make changes to improve your performance next year.
Evaluation takes place after the annual review. It helps to identify what went well and what didn’t. It also provides feedback on the performance of people.
Statistics
- UpCounsel accepts only the top 5 percent of lawyers on its site. (upcounsel.com)
- The BLS says that financial services jobs like banking are expected to grow 4% by 2030, about as fast as the national average. (wgu.edu)
- This field is expected to grow about 7% by 2028, a bit faster than the national average for job growth. (wgu.edu)
- Our program is 100% engineered for your success. (online.uc.edu)
- The profession is expected to grow 7% by 2028, a bit faster than the national average. (wgu.edu)
External Links
How To
How can you use the Kaizen method?
Kaizen means continuous improvement. The term was coined in the 1950s at Toyota Motor Corporation and refers to the Japanese philosophy emphasizing constant improvement through small incremental changes. It's a team effort to continuously improve processes.
Kaizen is one the most important methods of Lean Manufacturing. Kaizen is a concept where employees in charge of the production line are required to spot problems during the manufacturing process before they become major issues. This increases the quality of products and reduces the cost.
Kaizen is an approach to making every worker aware and alert to what is happening around them. To prevent problems from happening, any problem should be addressed immediately. Report any problem you see at work to your manager.
When doing kaizen, there are some principles we must follow. When working with kaizen, we always start with the end result and move towards the beginning. We can improve the factory by first fixing the machines that make it. Then, we fix the machines that produce components and then the ones that produce raw materials. And finally, we fix the workers who work directly with those machines.
This approach is called 'kaizen' because it focuses on improving everything steps by step. When we are done fixing the whole factory, we go back to the beginning and continue until we reach perfection.
To implement kaizen in your business, you need to find out how to measure its effectiveness. There are many ways to tell if kaizen is effective. Another method is to see how many defects are found on the products. Another way is determining how much productivity increased after implementing kaizen.
A good way to determine whether kaizen has been implemented is to ask why. Is it because the law required it or because you want to save money. Did you really believe that it would be a success factor?
Suppose you answered yes to any of these questions, congratulations! You're ready to start kaizen.