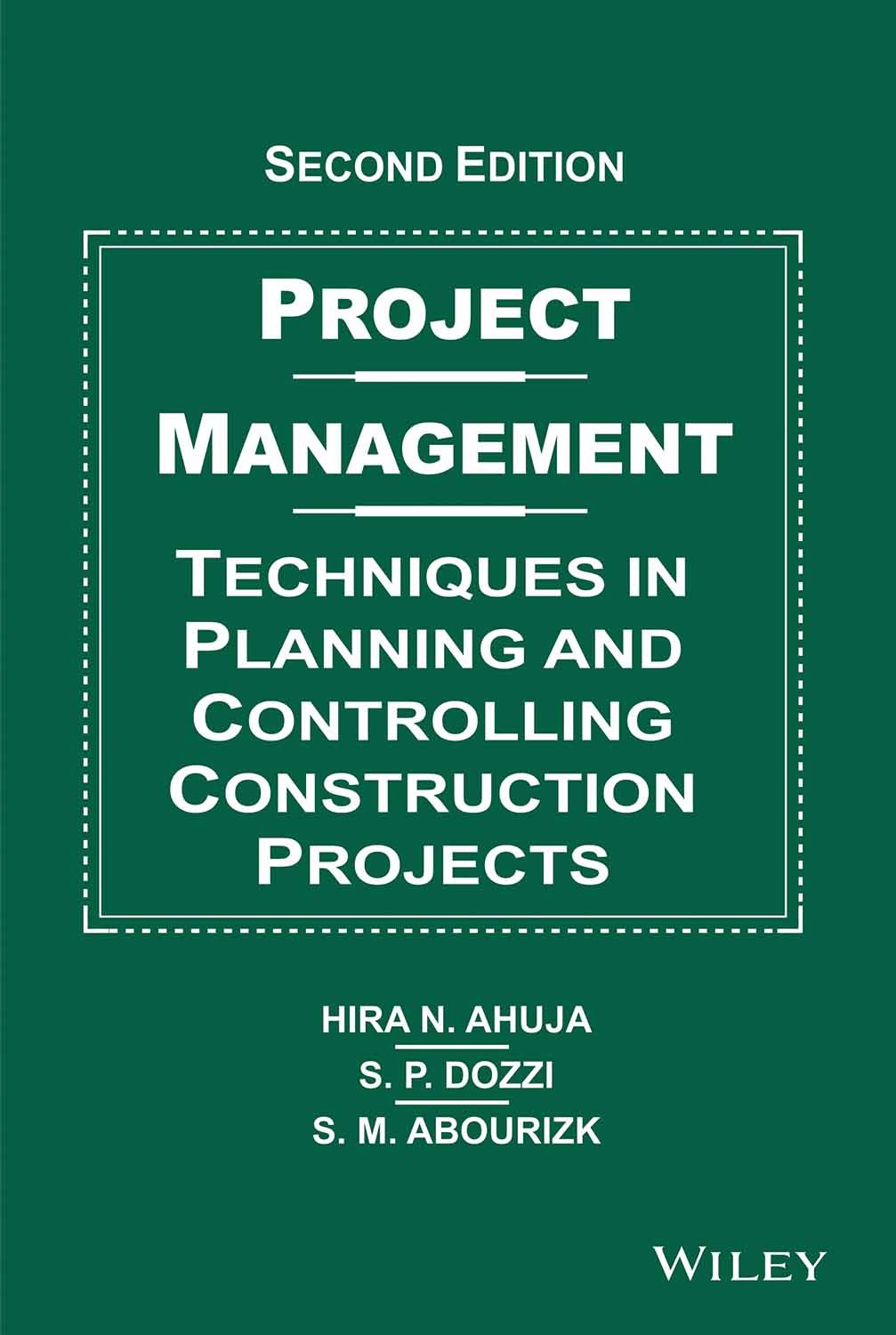
Business process management refers to a discipline that is focused on automating business processes and improving their efficiency. You can use a variety methods to achieve your goal. The three fundamental concepts of business process administration are modeling, automation and observability. Learn more about the benefits of business process management by reading this article.
Management of business processes
Business process management (BPM) helps organizations manage complexity and achieve flexible changes in a way that benefits customers. BPM uses data-driven information to improve business process and it is a great way to ensure a company's long-term success. BPM ultimately helps a company to digitally transform and stand apart from other companies.
A business procedure is a collection of repeatable tasks or events that occur in a business. This is an integral part of managing a business and can be used across all industries. To ensure smooth transitions to new positions, an organization could implement a standard onboarding process. This could include documentation, training materials checklists and agreements as well as automating these tasks.
Business process modeling
Business process modeling allows you to automate and analyze business processes. This process can be useful for many purposes. It allows you find waste and optimize the flow. It can also help you gain a better understanding of your business and determine areas that need improvement. It will save you money and time.
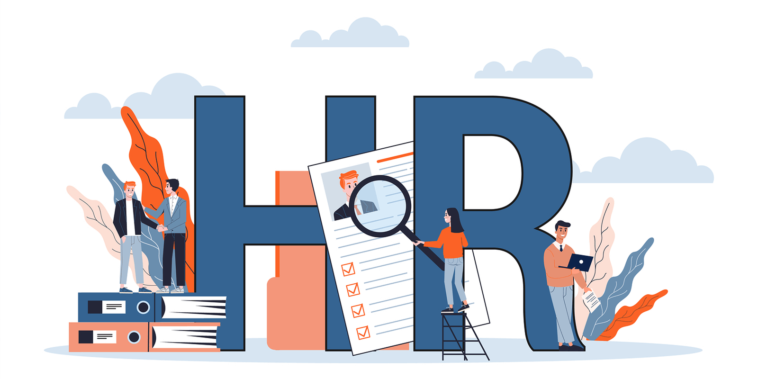
There are many tools and techniques that can be used to facilitate process modeling. One of these is value stream mapping. It highlights the crucial steps of a process, as well the flow materials and information. This technique is also known by input-process–output modeling. The process flow is basically a functional graph with inputs and outputs related to the input.
Orchestration of business processes
Orchestration is a method for coordinating different processes. Orchestration is a team effort. All participants must be aware of the business process, its operations, and the messages they need to exchange. The orchestration's central component is the process coordinator. This technique can also be used to integrate web services into larger business processes. It makes it possible to plan alternate scenarios in the case of mishaps.
Process orchestration technology is relatively new. Only a few automation products are considered orchestration engine tools. The key differentiator of these tools is their ability to manage multiple disparate processes. Some orchestration programs include REST API adapters. This allows for reusable tasks.
Monitoring business processes
A software program that monitors business processes is called Business Process Monitoring. It is an app that is installed in computers. The software program helps organizations detect and correct problems in business processes. It can also improve the quality of products and services. The software can also be purchased and installed on most systems.
A company can identify the root causes of problems, identify affected processes, and inform the relevant stakeholders about solutions. In turn, business process monitoring increases a company's productivity and efficiency.
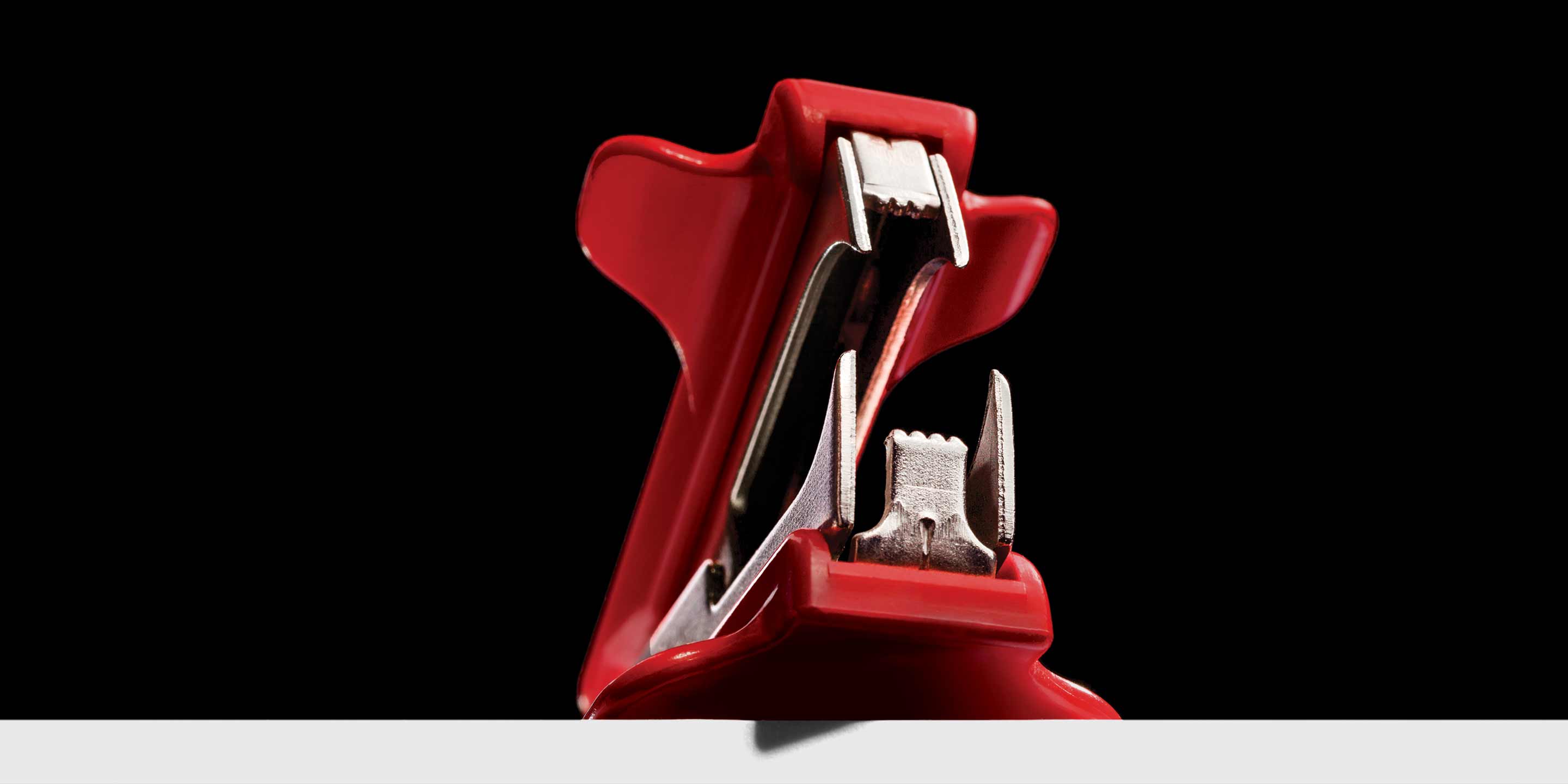
Business process improvement
Business process improvement can be used to improve the efficiency and effectiveness of a business's operations. The fundamental principles of business process improvement are to minimize inefficiencies and increase performance time. The first step is to identify the problem areas and identify solutions. Stakeholders and employees must be involved in business process improvement. It may involve introducing new systems or teams or re-designing existing processes. It is important to test changes in order minimize risks.
Companies can improve business processes to increase quality. Customers who are satisfied with their products will be more likely to buy from them again, which leads to increased sales. Also, satisfied customers are more likely than not to become repeat customers. This leads to greater revenue.
FAQ
What is the difference between TQM and Six Sigma?
The major difference between the two tools for quality management is that six Sigma focuses on eliminating defect while total quality control (TQM), on improving processes and decreasing costs.
Six Sigma is a methodology for continuous improvement. It emphasizes the elimination of defects by using statistical methods such as control charts, p-charts, and Pareto analysis.
This method has the goal to reduce variation of product output. This is done by identifying and correcting the root causes of problems.
Total quality management refers to the monitoring and measurement of all aspects in an organization. Training employees is also part of total quality management.
It is used to increase productivity.
What are some common mistakes managers make?
Managers can make their jobs more difficult than necessary.
They may not be able to delegate enough responsibility to staff or provide adequate support.
Many managers lack the communication skills to motivate and lead their employees.
Managers can set unrealistic expectations for their employees.
Managers may attempt to solve all problems themselves, rather than delegating it to others.
What is the best way to motivate your employees as a manager?
Motivation refers to the desire to perform well.
Doing something that is enjoyable can help you get motivated.
You can also feel motivated by making a positive contribution to the success in the organization.
For example, if your goal is to become a physician, you will probably find it more motivational to see patients rather than to read a lot of medicine books.
Another type of motivation comes from within.
Perhaps you have a strong sense to give back, for example.
You might even enjoy the work.
If you don’t feel motivated, find out why.
Then think about how you can make your life more motivating.
What is the difference in leadership and management?
Leadership is about being a leader. Management is about controlling others.
Leaders inspire followers, while managers direct workers.
A leader inspires others to succeed, while a manager helps workers stay on task.
A leader develops people; a manager manages people.
What are the steps involved in making a decision in management?
Managers have to make complex decisions. This involves many factors including analysis, strategy and planning, implementation, measurement and evaluation, feedback, feedback, and others.
Remember that people are humans just like you, and will make mistakes. This is the key to managing them. You can always improve your performance, provided you are willing to make the effort.
This video shows you how management makes decisions. We'll discuss the different types and reasons they are important. Managers should also know how to navigate them. You'll learn about the following topics:
What is the difference in a project and program?
A project is temporary while a programme is permanent.
A project has usually a specified goal and a time limit.
It is often done in a team that reports to another.
A program is usually defined by a set or goals.
It is typically done by one person.
How to effectively manage employees
Achieving employee happiness and productivity is key to managing them effectively.
This includes setting clear expectations for their behavior and tracking their performance.
Managers must be clear about their goals and those of their teams in order to succeed.
They should communicate clearly to staff members. They need to communicate clearly with their staff.
They should also keep records of all activities within their team. These include:
-
What was the result?
-
What was the work involved?
-
Who did it and why?
-
How did it get done?
-
Why was it done?
This data can be used to evaluate and monitor performance.
Statistics
- This field is expected to grow about 7% by 2028, a bit faster than the national average for job growth. (wgu.edu)
- As of 2020, personal bankers or tellers make an average of $32,620 per year, according to the BLS. (wgu.edu)
- Hire the top business lawyers and save up to 60% on legal fees (upcounsel.com)
- The average salary for financial advisors in 2021 is around $60,000 per year, with the top 10% of the profession making more than $111,000 per year. (wgu.edu)
- 100% of the courses are offered online, and no campus visits are required — a big time-saver for you. (online.uc.edu)
External Links
How To
What is Lean Manufacturing?
Lean Manufacturing is a method to reduce waste and increase efficiency using structured methods. They were developed in Japan by Toyota Motor Corporation (in the 1980s). The primary goal was to make products with lower costs and maintain high quality. Lean manufacturing is about eliminating redundant steps and activities from the manufacturing process. It is made up of five elements: continuous improvement, continuous improvement, just in-time, continuous change, and 5S. Pull systems allow customers to get exactly what they want without having to do extra work. Continuous improvement means continuously improving on existing processes. Just-in–time refers when components or materials are delivered immediately to their intended destination. Kaizen stands for continuous improvement. Kaizen can be described as a process of making small improvements continuously. The 5S acronym stands for sort in order, shine standardize and maintain. These five elements are used together to ensure the best possible results.
The Lean Production System
Six key concepts form the foundation of the lean production system:
-
Flow - focuses on moving information and materials as close to customers as possible.
-
Value stream mapping - break down each stage of a process into discrete tasks and create a flowchart of the entire process;
-
Five S's – Sort, Put In Order Shine, Standardize and Sustain
-
Kanban is a visual system that uses visual cues like stickers, colored tape or stickers to keep track and monitor inventory.
-
Theory of constraints: identify bottlenecks in your process and eliminate them using lean tools, such as kanban board.
-
Just-in-time - deliver components and materials directly to the point of use;
-
Continuous improvement - make incremental improvements to the process rather than overhauling it all at once.