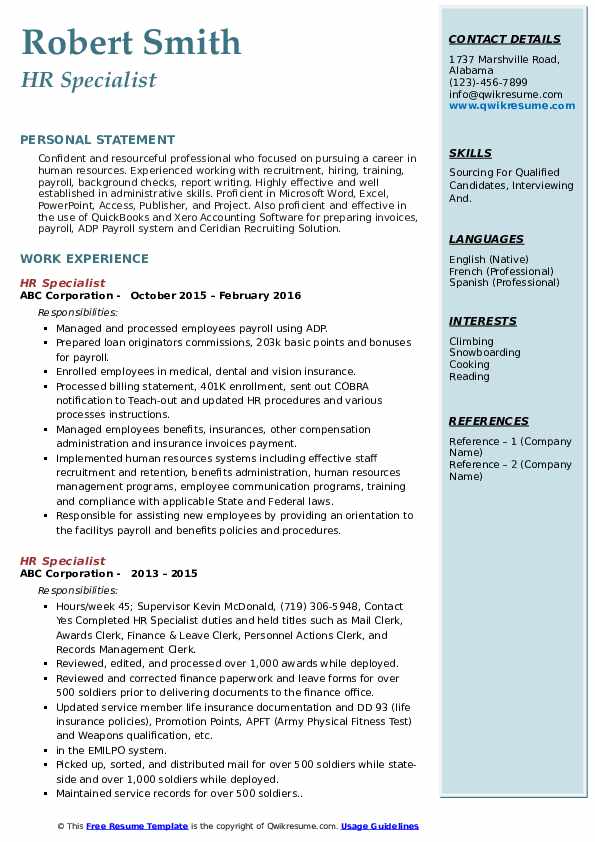
Inventory management is the act of purchasing, storing, using and packaging goods. It ensures that a company will always have enough finished goods to fulfill customer demands. It helps companies track buyer trends and improves time-to-market. It is essential to know how to efficiently use inventory to ensure effective inventory management.
Inventory management is the process for buying, storing or using goods and then packaging them to ship them.
It is essential to manage inventory. It is essential to running a successful company as it can prevent financial problems. It can be hard to manage inventory if you have multiple locations. For example, you might have multiple warehouses. This means that inventory levels must be monitored at all locations. While managing inventory can seem time-consuming, it is crucial for your company's success.
There are many ways to manage inventory. One method is economic order number (EOQ). This measurement is based on the total cost for production and consumer demand. It determines how much inventory a company should keep. EOQ can help a company remain profitable and release cash.
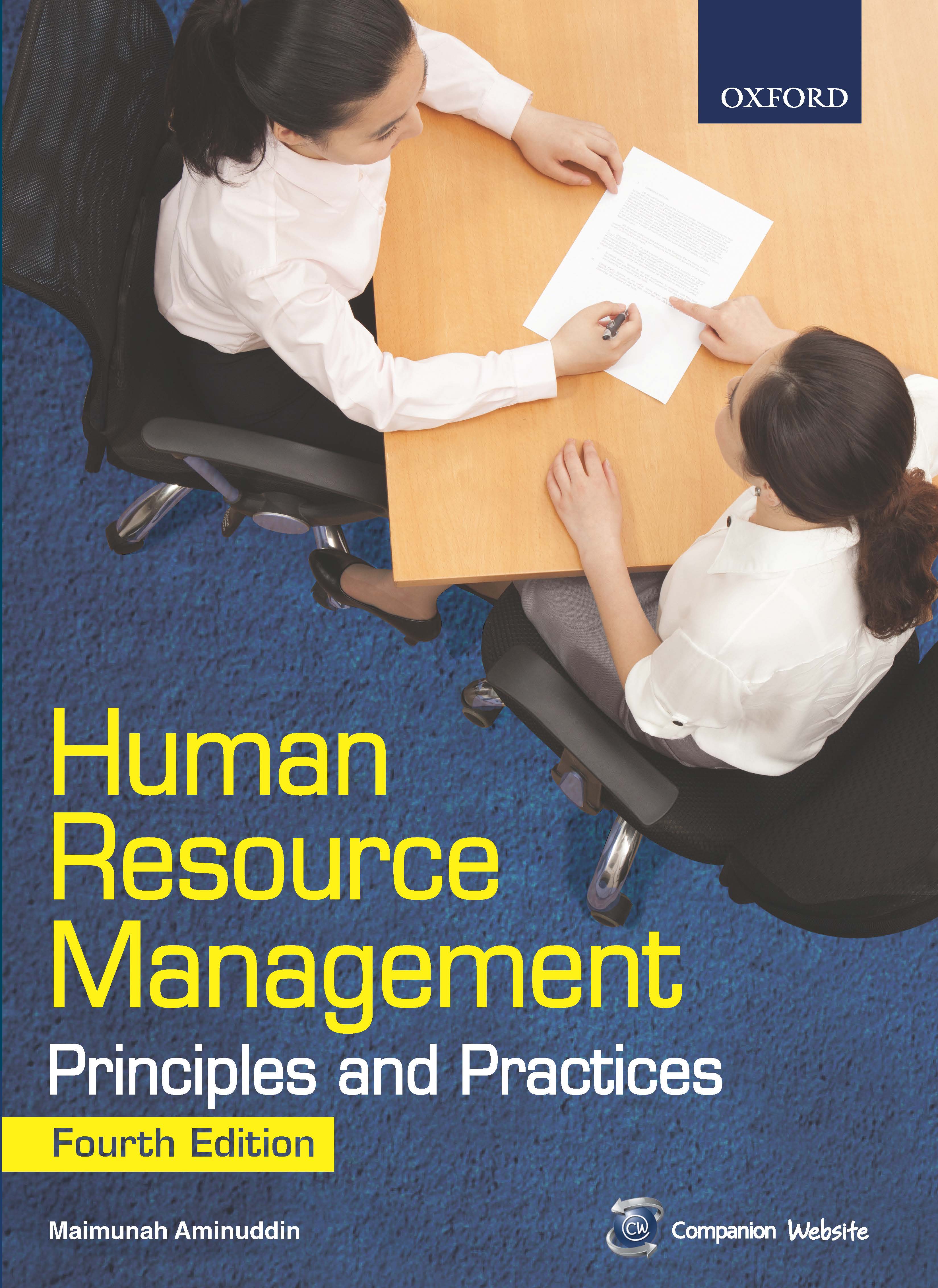
It ensures that finished goods are readily available
Companies that are able to manage their inventory effectively can be distinguished from their peers. It includes sorting products and storing them in accordance with demand. This could also include cross docking, dropshipping. Software systems can also help to manage inventory levels. The right software system can help businesses manage their stock levels to optimize inventory planning. Inventory management is usually initiated when a customer places orders online or at a storefront.
Another type of inventory management focuses on raw materials. These may be purchased from another business or manufactured in-house. This inventory includes parts in the process or manufacturing, such nuts, screws, washers and other parts. It may also include inventory in the process of manufacturing, such as parts needed for packaging finished goods or maintenance repairs. It can also include office supplies like paper or pencils.
It helps companies keep track of buyer trends over time
Inventory management is the act of keeping track of what items are in stock. It involves reviewing this data on a regular basis to determine which items should be stockpiled and when. This is vital because it allows companies to identify trends and patterns in buyer behaviour. Inventory tracking can also be useful in identifying shrinkage problems.
Inventory management also helps companies identify deadstock or obsolete products. These products are items that customers have discontinued buying or are at the end of their useful life. Inefficient warehouse organization also causes problems such as inadequate signage, inadequate walking spaces, and unsafe storage conditions. The inventory turnover ratio (ITR) can also be used to determine how often a company is replacing its inventory. The higher the ITR, the more likely the company is to sell the majority of its inventory during a cycle.
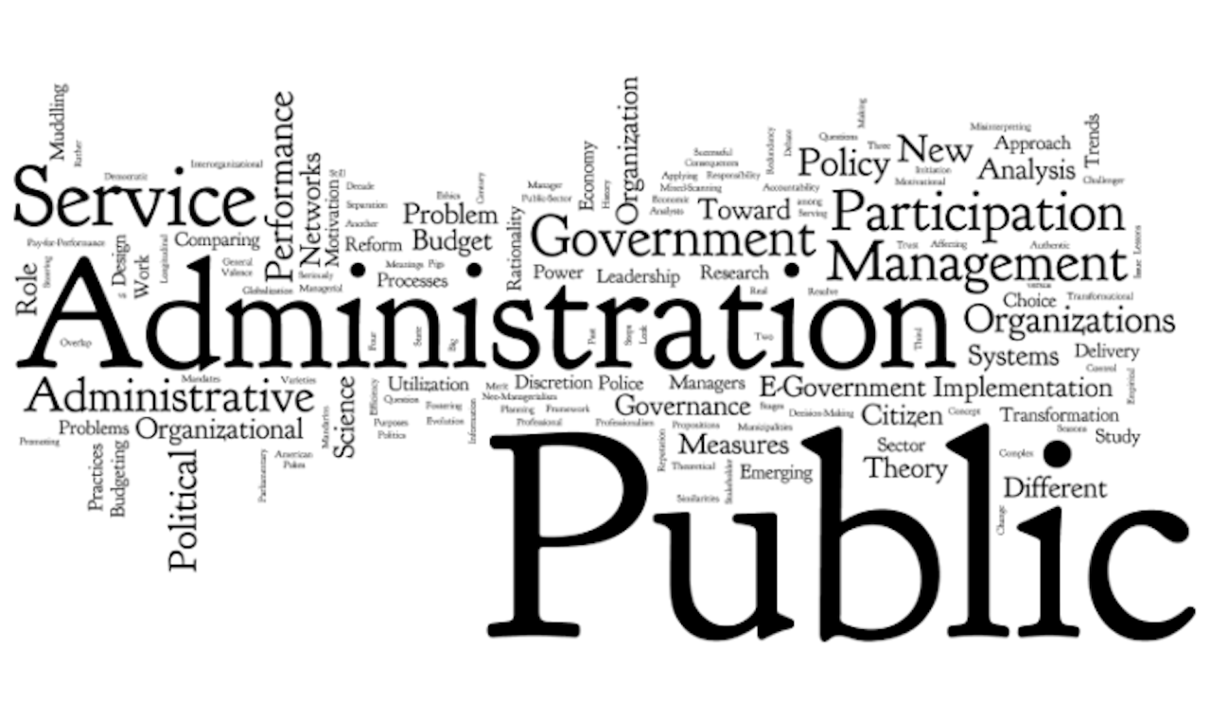
It improves time to market
Inventory management allows companies and organizations to ship items more quickly and ensures that they have sufficient stock. Inventory management also helps to reduce the chance of cancelled orders and out-of-stock products. Customers are often frustrated by out-of-stock products. Inventory management is a way to prevent this.
Every business needs to manage inventory, regardless of its size. This complex process requires many decisions and considerations. Excel formulas might be used by small companies to keep track and determine reorder point stock. Enterprise resource planning software can be used for larger businesses. Specialized SaaS applications may be available for large corporations.
FAQ
What is Kaizen?
Kaizen refers to a Japanese term that stands for "continuous improvements." It is a philosophy which encourages employees in continuously improving their work environment.
Kaizen is based upon the belief that each person should be capable of doing his or her job well.
What does Six Sigma mean?
Six Sigma uses statistical analysis for problems to be found, measured, analyzed root causes, corrected, and learned from.
The first step is to identify the problem.
Next, data will be collected and analyzed to determine trends and patterns.
Then corrective actions are taken to solve the problem.
Final analysis of data is done to determine if the problem has been solved.
This cycle will continue until the problem is solved.
It seems so difficult sometimes to make sound business decisions.
Businesses are complex systems, and they have many moving parts. The people who run them must juggle multiple priorities at once while also dealing with uncertainty and complexity.
Understanding the impact of these factors on the system is crucial to making sound decisions.
You must first consider what each piece of the system does and why. It's important to also consider how they interact with each other.
You need to ask yourself if your previous actions have led you to make unfounded assumptions. If they don't, you may want to reconsider them.
For help, ask someone else if you're still stumped after all the above. You may be able to see things from a different perspective than you are and gain insight that can help you find a solution.
What kind people use Six Sigma?
Six Sigma will most likely be familiar to people who have worked in statistics and operations research. However, anyone involved in any aspect of business can benefit from using it.
Because it requires a high level of commitment, only those with strong leadership skills will make an effort necessary to implement it successfully.
What is the difference in a project and program?
A project is temporary while a programme is permanent.
A project has usually a specified goal and a time limit.
It is often done in a team that reports to another.
A program often has a set goals and objectives.
It is often done by one person.
What are the 3 main management styles?
The three major management styles are authoritarian (left-faire), participative and laissez -faire. Each style has its own strengths and weaknesses. Which style do you prefer? Why?
Autoritarian - The leader sets direction and expects everyone else to follow it. This style is most effective when an organization is large, stable, and well-run.
Laissez-faire - The leader allows each individual to decide for him/herself. This style works best when the organization is small and dynamic.
Participative - Leaders listen to all ideas and suggestions. This style is most effective in smaller organizations, where everyone feels valued.
What are management concepts, you ask?
Management concepts are the principles and practices used by managers to manage people, resources. These topics include job descriptions, performance evaluations and training programs. They also cover human resource policies, job description, job descriptions, job descriptions, employee motivation, compensation systems, organizational structures, and many other topics.
Statistics
- The average salary for financial advisors in 2021 is around $60,000 per year, with the top 10% of the profession making more than $111,000 per year. (wgu.edu)
- Your choice in Step 5 may very likely be the same or similar to the alternative you placed at the top of your list at the end of Step 4. (umassd.edu)
- The profession is expected to grow 7% by 2028, a bit faster than the national average. (wgu.edu)
- As of 2020, personal bankers or tellers make an average of $32,620 per year, according to the BLS. (wgu.edu)
- Our program is 100% engineered for your success. (online.uc.edu)
External Links
How To
How do I do the Kaizen Method?
Kaizen means continuous improvement. This term was first used by Toyota Motor Corporation in the 1950s. It refers to the Japanese philosophy that emphasizes continuous improvement through small incremental changes. It is a process where people come together to improve their processes.
Kaizen is one method that Lean Manufacturing uses to its greatest advantage. This concept requires employees to identify and solve problems during manufacturing before they become major issues. This increases the quality of products and reduces the cost.
Kaizen is the idea that every worker should be aware of what is going on around them. So that there is no problem, you should immediately correct it if something goes wrong. If someone is aware of a problem at work, he/she should inform his/her manager immediately.
Kaizen is based on a few principles. The end product is always our starting point and we work toward the beginning. In order to improve our factory's production, we must first fix the machines producing the final product. Then, we fix the machines that produce components and then the ones that produce raw materials. We then fix the workers that work with those machines.
This approach is called 'kaizen' because it focuses on improving everything steps by step. Once we have finished fixing the factory, we return to the beginning and work until perfection.
To implement kaizen in your business, you need to find out how to measure its effectiveness. There are several ways that you can tell if your kaizen system is working. One method is to inspect the finished products for defects. Another way is to check how much productivity has grown since kaizen was implemented.
A good way to determine whether kaizen has been implemented is to ask why. You were trying to save money or obey the law? You really believed it would make you successful?
Congratulations! You're ready to start kaizen.