
It is important to keep a RAID log for project management. It can be used to help you understand your assumptions and identify risks. It can help you manage problems and improve your project.
RAID logs can be used to communicate between project managers with stakeholders. It provides a detailed record of decisions and activities that have occurred during the project. This helps project managers to keep track of important information, make consistent decisions, and keep their teams informed. RAID logs also serve as a useful reference document. By keeping a RAID log, you can monitor your project's progress, learn from past mistakes, and improve your next project.
RAID logs can be used to assist project managers in identifying risks, assessing the impact of those risks, and deciding on a course for action. You can use them to prevent potential problems from arising, or to aid you in understanding the implications of any issues. This is an important step you need to make before your project gets underway.
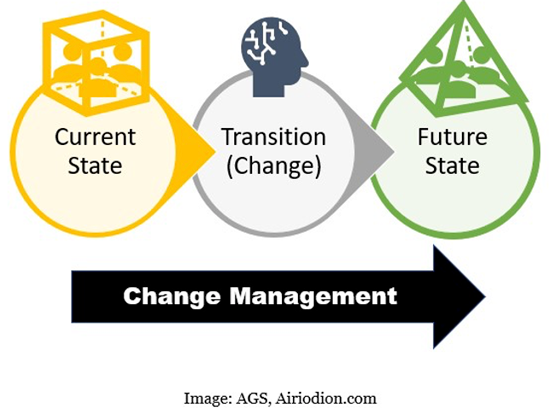
Risks are unavoidable in projects. They are often the most difficult part of a project's management and identification. Failure to take the appropriate steps could lead to poor delivery and a project failure. It is important to recognize risks early on in a project and to devise a plan for minimizing them.
Most risks can be divided into High Impact items (which have a very low impact on projects) and Low Impact, which has a significantly negative effect on them. The best way to assess the potential impact of a particular risk is to measure its severity and likelihood. A reduction in either of these factors will increase the chances that a risk is being addressed. If either factor is increased, the risk becomes more severe. You should therefore monitor the severity and impact of any risks.
Assumptions are another major component of projects. Even though you might not be able to prove a point, it is still a good idea to record your assumptions. You have many options to record your assumptions. The RAID log is one of the best places to start. Some Project/Program managers prefer to be the sole authors of their RAID log. Others prefer to use other tools, such as an issues log. It is important to properly document your assumptions. However, these are often better used for long term projects.
RAID logs are important tools for evaluating risk. They should be kept up-to-date throughout the project. It serves as a useful reference document, and can also be used for communication purposes. This is particularly important for status reports and audits. The RAID log should be updated with new risks and issues as they arise, or with additional details about existing issues. It's a great way to track your team's progress.
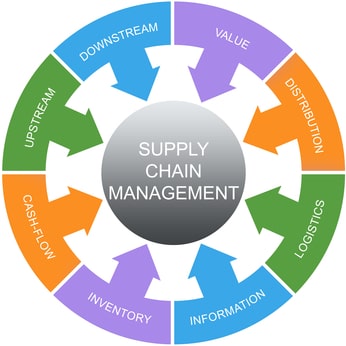
Project managers can use a RAID log, especially during the initial stages of a project. It can help project managers to stay more organized and maintain all important information in one location. RAID logs are also useful for collecting data, explaining project issues and tracking assumptions.
FAQ
What is TQM?
The quality movement was born during the industrial revolution when manufacturing companies realized they could not compete on price alone. They needed to improve the quality and efficiency of their products if they were to be competitive.
Management developed Total Quality Management to address the need for improvement. It focused on all aspects of an organisation's performance. It included continual improvement processes, employee involvement, customer satisfaction, and customer satisfaction.
Six Sigma is so popular.
Six Sigma is easy to use and can lead to significant improvements. It provides a framework that allows for improvement and helps companies concentrate on what really matters.
What kind people use Six Sigma?
Six-sigma will be well-known to anyone who has worked in operations research or statistics. However, anyone involved in any aspect of business can benefit from using it.
It requires high levels of commitment and leadership skills to be successful.
What's the difference between Six Sigma and TQM?
The main difference in these two quality management tools lies in the fact that six sigma is focused on eliminating defects and total quality management (TQM), emphasizes improving processes and reducing costs.
Six Sigma is a methodology for continuous improvement. This method emphasizes eliminating defects using statistical methods such p-charts, control charts, and Pareto analysis.
This method seeks to decrease variation in product output. This is accomplished through identifying and correcting root causes.
Total quality management is the measurement and monitoring of all aspects within an organization. Training employees is also part of total quality management.
It is commonly used as a strategy for increasing productivity.
What are management concepts?
Management concepts are the principles and practices used by managers to manage people, resources. These include topics such as human resource policies and job descriptions, performance assessments, training programs and employee motivation.
What is a management tool to help with decision-making?
A decision matrix is an easy but powerful tool to aid managers in making informed decisions. They can think about all options and make informed decisions.
A decision matrix represents alternatives in rows and columns. It is easy to see how each option affects the other options.
The boxes on the left hand side of this matrix represent four possible choices. Each box represents an option. The top row shows the status quo (the current situation), and the bottom row shows what would happen if nothing was done at all.
The effect of choosing Option 1 can be seen in column middle. In this case, it would mean increasing sales from $2 million to $3 million.
The next two columns show the effects of choosing Options 2 and 3. These are positive changes - they increase sales by $1 million and $500 thousand respectively. These changes can also have negative effects. Option 2 increases the cost of goods by $100,000. Option 3 decreases profits and makes them less attractive by $200,000.
The last column displays the results of selecting Option 4. This would result in a reduction of sales of $1 million.
The best thing about using a decision matrix is that you don't need to remember which numbers go where. You can just glance at the cells and see immediately if one given choice is better.
This is because the matrix has already taken care of the hard work for you. It is as simple as comparing the numbers within the relevant cells.
Here's a sample of how you might use decision matrixes in your business.
It is up to you to decide whether to spend more money on advertising. You'll be able increase your monthly revenue by $5000 if you do. You will still have to pay $10000 per month in additional expenses.
If you look at the cell that says "Advertising", you can see the number $15,000. Advertising is worth more than its cost.
What are the 3 main management styles?
There are three types of management: participative, laissez faire, and authoritarian. Each style has its own strengths and weaknesses. Which style do yo prefer? Why?
Autoritarian – The leader sets the direction for everyone and expects them to follow. This style works best if the organization is large and stable.
Laissez-faire is a leader who allows everyone to make their own decisions. This style works best when the organization is small and dynamic.
Participative – Leaders are open to suggestions and ideas from everyone. This style works best in smaller organizations where everyone feels valued.
Statistics
- 100% of the courses are offered online, and no campus visits are required — a big time-saver for you. (online.uc.edu)
- The profession is expected to grow 7% by 2028, a bit faster than the national average. (wgu.edu)
- As of 2020, personal bankers or tellers make an average of $32,620 per year, according to the BLS. (wgu.edu)
- UpCounsel accepts only the top 5 percent of lawyers on its site. (upcounsel.com)
- Your choice in Step 5 may very likely be the same or similar to the alternative you placed at the top of your list at the end of Step 4. (umassd.edu)
External Links
How To
How can Lean Manufacturing be done?
Lean Manufacturing uses structured methods to reduce waste, increase efficiency and reduce waste. They were created in Japan by Toyota Motor Corporation during the 1980s. The goal was to produce quality products at lower cost. Lean manufacturing seeks to eliminate unnecessary steps and activities in the production process. It includes five main elements: pull systems (continuous improvement), continuous improvement (just-in-time), kaizen (5S), and continuous change (continuous changes). It is a system that produces only the product the customer requests without additional work. Continuous improvement means continuously improving on existing processes. Just-in–time refers when components or materials are delivered immediately to their intended destination. Kaizen means continuous improvement, which is achieved by implementing small changes continuously. Finally, 5S stands for sort, set in order, shine, standardize, and sustain. These five elements can be combined to achieve the best possible results.
Lean Production System
Six key concepts underlie the lean production system.
-
Flow: The goal is to move material and information as close as possible from customers.
-
Value stream mapping - break down each stage of a process into discrete tasks and create a flowchart of the entire process;
-
Five S's – Sort, Put In Order Shine, Standardize and Sustain
-
Kanban: Use visual signals such stickers, colored tape, or any other visual cues, to keep track your inventory.
-
Theory of Constraints - Identify bottlenecks in the process, and eliminate them using lean tools such kanban boards.
-
Just-in-time - deliver components and materials directly to the point of use;
-
Continuous improvement - Make incremental improvements rather than overhauling the entire process.