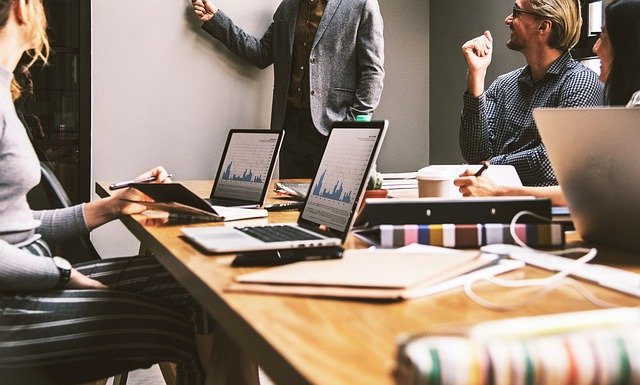
Companies that manage waste are responsible for disposing of it. Many companies offer this service. Some of these include Republic Service, Advanced Disposal, and Casella. One of these companies is a good choice for you if your looking for a waste management company. They can provide you with the services that you need.
Republic Service
For over four decades, Republic Service has been a leading waste management company in the North Texas region, employing more than 1,300 people. Republic Service is actively involved in the community by supporting local fire departments as well as donating resources for many causes. It is also an award-winning organization, having been included in the Dow Jones Sustainability World Indices third consecutive year. Barron's has recently named it one the 100 most sustainable corporations. RobecoSAM's Sustainability Handbook awarded the Gold Class Award to the company. It was also included in the Ethisphere Institute’s World’s Most Ethical Businesses list, a distinction it has earned for the second year.
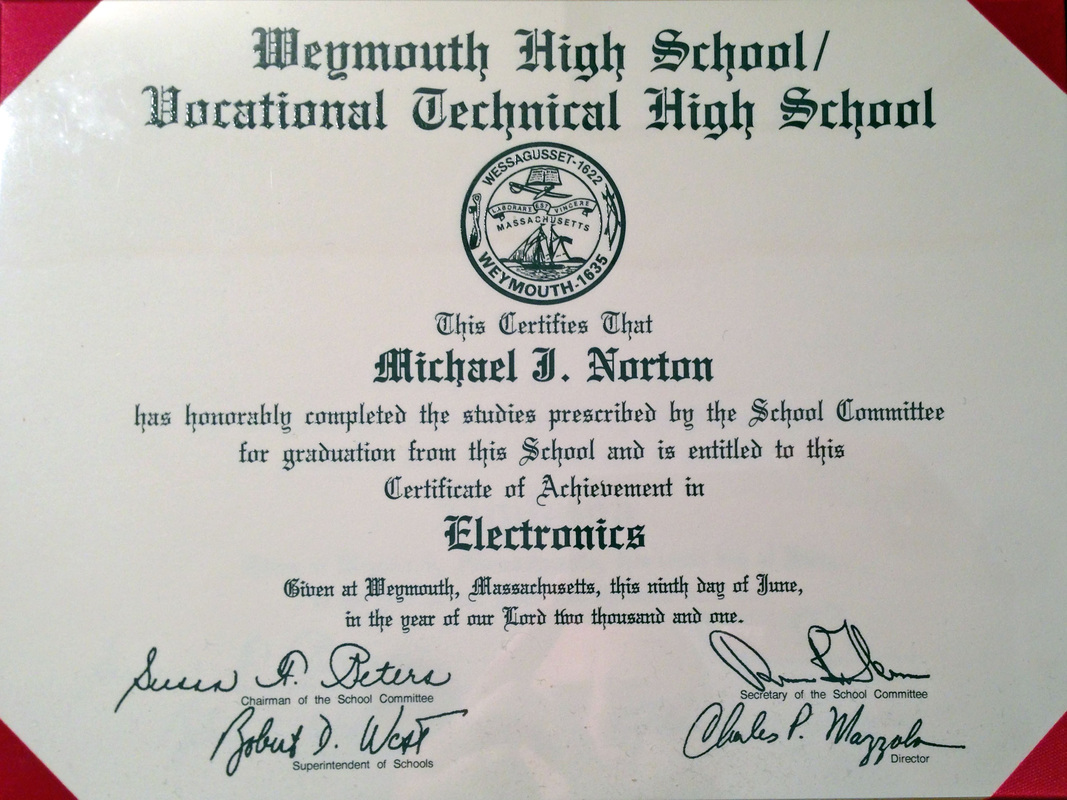
Both Republic Services and Waste Management have been undervalued by some investors. However, there are some key differences. Both companies offer similar solutions to waste management, but Republic Services has grown its revenues, operating cash flow, free cash flow, and cash flow quicker than Waste Management. Furthermore, Wall Street expects it to grow faster than Waste Management, with earnings projected to rise by 12% per year over the next five years. The company's growth is also being driven by tuck-in acquisitions.
Advanced Disposal
Advanced Disposal specializes as a waste management firm that recycles, composts, and disposes of recyclable materials. They have been in operation for more than 50 years and are located in Houston, Texas. Their corporate headquarters are located at the Bank of America Tower. They also have offices across the country.
The deal is expected close in 2020's first quarter. Both boards of directors approved this deal unanimously. Both companies anticipate that they will maintain their strong balances and investment-grade credit scores.
Casella
Casella has been a leader in the industry of waste management. In June, Casella announced the acquisition of three New England solid waste firms. It is currently the fifth-largest solid refuse company in the United States. It also invests in other companies. Its stock has risen more than 55% since then, and its revenues grew by 10% last year.
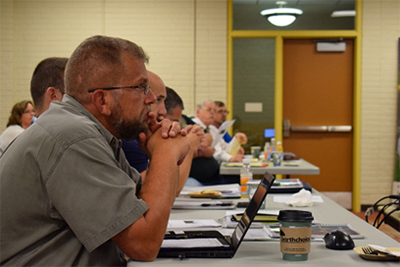
Casella's headquarters is in rural Vermont. It serves six northeastern states and residents. Its network comprises nine landfills, eighty-eight transfer stations, 49 solid waste collection operations, four landfill gas to energy facilities, 20 recycling centers, and four landfill gas-to–energy facilities. It collects approximately 4 million tons of waste each year, and it makes $30 million in profit.
FAQ
What is the difference between TQM and Six Sigma?
The main difference in these two quality management tools lies in the fact that six sigma is focused on eliminating defects and total quality management (TQM), emphasizes improving processes and reducing costs.
Six Sigma stands for continuous improvement. It emphasizes the elimination or minimization of defects through statistical methods such control charts and p charts.
This method has the goal to reduce variation of product output. This is done by identifying root causes and rectifying them.
Total quality management is the measurement and monitoring of all aspects within an organization. It also includes the training of employees to improve performance.
It is used to increase productivity.
What kind people use Six Sigma?
People who have worked with statistics and operations research will usually be familiar with the concepts behind six sigma. It can be used by anyone in any business aspect.
It requires high levels of commitment and leadership skills to be successful.
What is Six Sigma?
Six Sigma uses statistical analyses to locate problems, measure them, analyze root cause, fix problems and learn from the experience.
The first step to solving the problem is to identify it.
Next, data is collected and analyzed to identify trends and patterns.
Then corrective actions are taken to solve the problem.
Final analysis of data is done to determine if the problem has been solved.
This continues until the problem has been solved.
How do you manage your employees effectively?
The key to effective management of employees is ensuring their happiness and productivity.
This also involves setting clear expectations and monitoring their performance.
Managers must be clear about their goals and those of their teams in order to succeed.
They need to communicate clearly and openly with staff members. They need to communicate clearly with their staff.
They must also keep records of team activities. These include:
-
What was achieved?
-
How much work was put in?
-
Who did it?
-
What was the moment it was completed?
-
Why?
This information is useful for monitoring performance and evaluating the results.
What are management principles?
Management concepts are the fundamental principles and practices that managers use when managing people and their resources. They cover topics such as job descriptions and performance evaluations, human resource policies, training programs, employee motivation, compens systems, organizational structure, among others.
What are the most common errors made by managers?
Managers sometimes make their own job harder than necessary.
They may not delegate enough responsibilities and not provide sufficient support.
Managers often lack the communication skills necessary to motivate and guide their teams.
Some managers create unrealistic expectations for their teams.
Some managers may try to solve every problem themselves instead of delegating responsibility to others.
Statistics
- The profession is expected to grow 7% by 2028, a bit faster than the national average. (wgu.edu)
- Your choice in Step 5 may very likely be the same or similar to the alternative you placed at the top of your list at the end of Step 4. (umassd.edu)
- Hire the top business lawyers and save up to 60% on legal fees (upcounsel.com)
- 100% of the courses are offered online, and no campus visits are required — a big time-saver for you. (online.uc.edu)
- This field is expected to grow about 7% by 2028, a bit faster than the national average for job growth. (wgu.edu)
External Links
How To
How is Lean Manufacturing done?
Lean Manufacturing is a method to reduce waste and increase efficiency using structured methods. They were created in Japan by Toyota Motor Corporation during the 1980s. The primary goal was to make products with lower costs and maintain high quality. Lean manufacturing eliminates unnecessary steps and activities from a production process. It consists of five basic elements: pull systems, continuous improvement, just-in-time, kaizen (continuous change), and 5S. Pull systems involve producing only what the customer wants without any extra work. Continuous improvement means continuously improving on existing processes. Just-in-time refers to when components and materials are delivered directly to the point where they are needed. Kaizen means continuous improvement, which is achieved by implementing small changes continuously. Five-S stands for sort. It is also the acronym for shine, standardize (standardize), and sustain. These five elements are used together to ensure the best possible results.
Lean Production System
Six key concepts make up the lean manufacturing system.
-
Flow - The focus is on moving information and material as close as possible to customers.
-
Value stream mapping is the ability to divide a process into smaller tasks, and then create a flowchart that shows the entire process.
-
Five S's – Sort, Put In Order Shine, Standardize and Sustain
-
Kanban – visual signals like colored tape, stickers or other visual cues are used to keep track inventory.
-
Theory of constraints - identify bottlenecks during the process and eliminate them with lean tools like Kanban boards.
-
Just-intime - Order components and materials at your location right on the spot.
-
Continuous improvement: Make incremental improvements to the process instead of overhauling it completely.