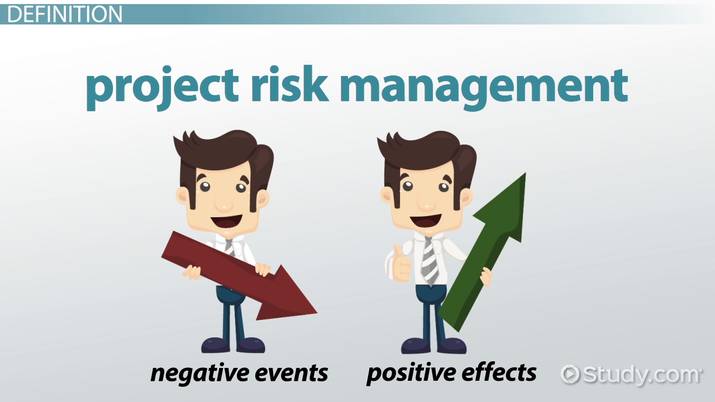
If you are looking for practical and strategic approach to managing global supply chains, this book will prove to be a useful guide for you. This book provides a comprehensive, systematic and easy-to-understand guide for both practitioners and researchers. Highly recommended. It explains the fundamental concepts and processes that underpin strategic supply chain management. The authors have provided a step-by-step methodology for achieving strategic supply chain objectives. Practitioners and researchers alike will enjoy this book.
Demand-driven supply chain
Demand-driven supply chains are strategic supply chains that respond to changes in demand. This allows companies to anticipate and satisfy customer requests immediately. It differs from the traditional model, where the supplier announces the availability of a new product and the retailer takes delivery. This model helps companies increase efficiency and keep their inventory under control. Demand-driven supply chains allow companies to respond faster and more efficiently to customer needs.
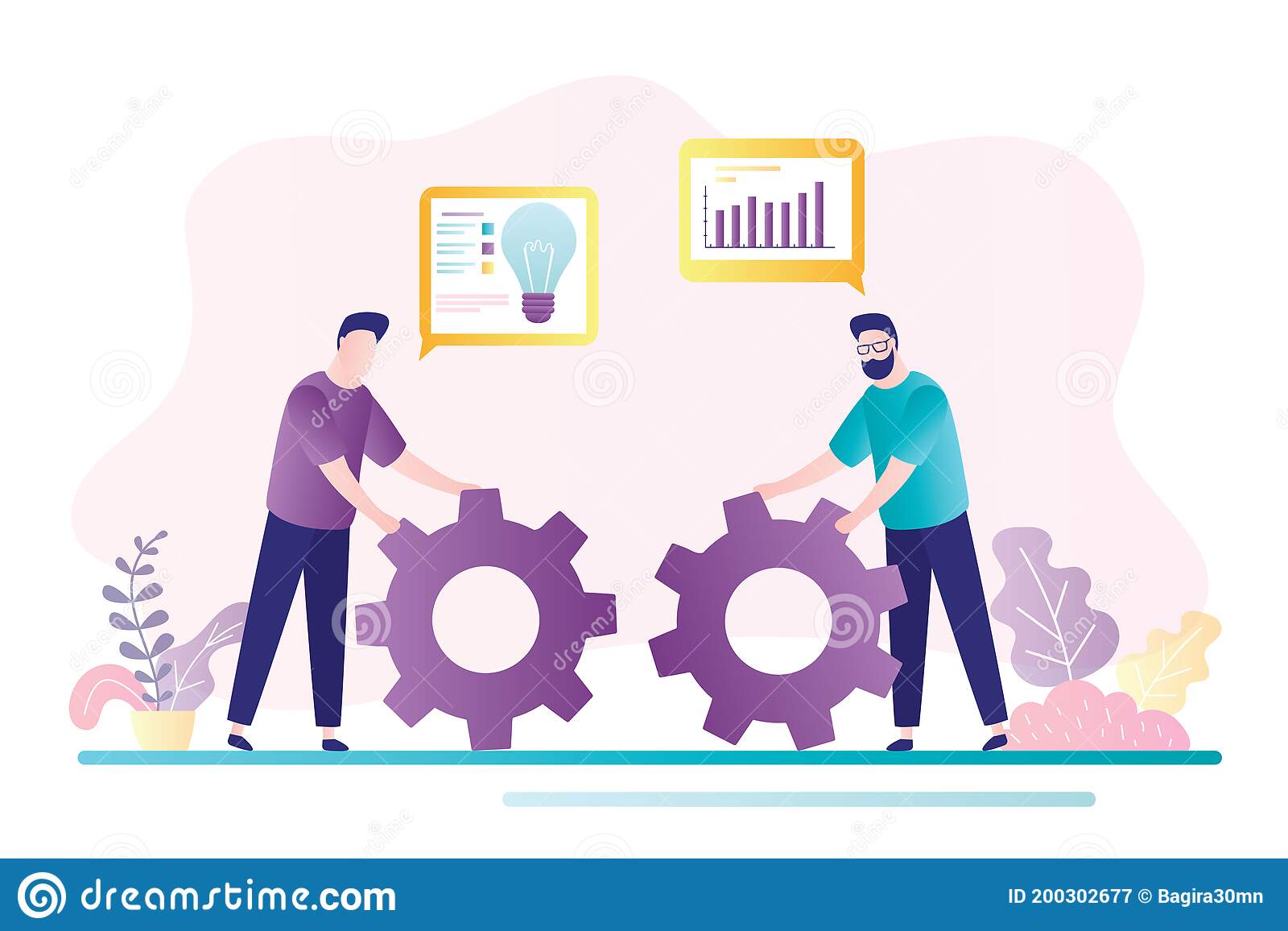
Planning
To optimize and plan the supply chain, tools that are organization-based are used. The planning approaches differ in the extent of decision-making that they support. Successful companies should develop annual strategic business plans that identify potential growth opportunities. Supply chain planning software is used by many organizations to plan and optimize their supply networks. This article outlines the many types of planning. You can choose the one that suits your preference.
Execution
The formal management of a company's supply chain network is called strategic supply chain management. The strategy is developed by the supply chain manager to maximize value, efficiency, reliability. This strategy must align with the company’s overall business strategy. It takes careful planning and execution to manage your supply chain. Understanding your supply chain is key to your business strategy. Here are some suggestions for supply chain management success. To begin, create a strategic vision of your supply chain.
Monitoring
Effective management depends on information. Managers that lack the right data and tools will fail to make effective decisions. As supply chains continue to grow in complexity, managers that are not diligent about monitoring the process are unprepared to handle disruptions and potential hazards. Supply chain monitoring is crucial. Monitoring your supply chain can have many benefits. Here are a few. Find out how you can get started.
Sustainability
It's not easy to create true sustainability within a strategic supply chain. The more complex the supply chain is, the more difficult it is. To ensure sustainability, the procurement department should designate a sustainability point individual who will oversee the process and evaluate the progress of major suppliers. The procurement team should also establish specific sustainability goals and demand that suppliers meet them. Transparency will be a key part of the entire process. An excellent way to assess supplier performance is to count the number products or services that are in line with the company's sustainability objectives.
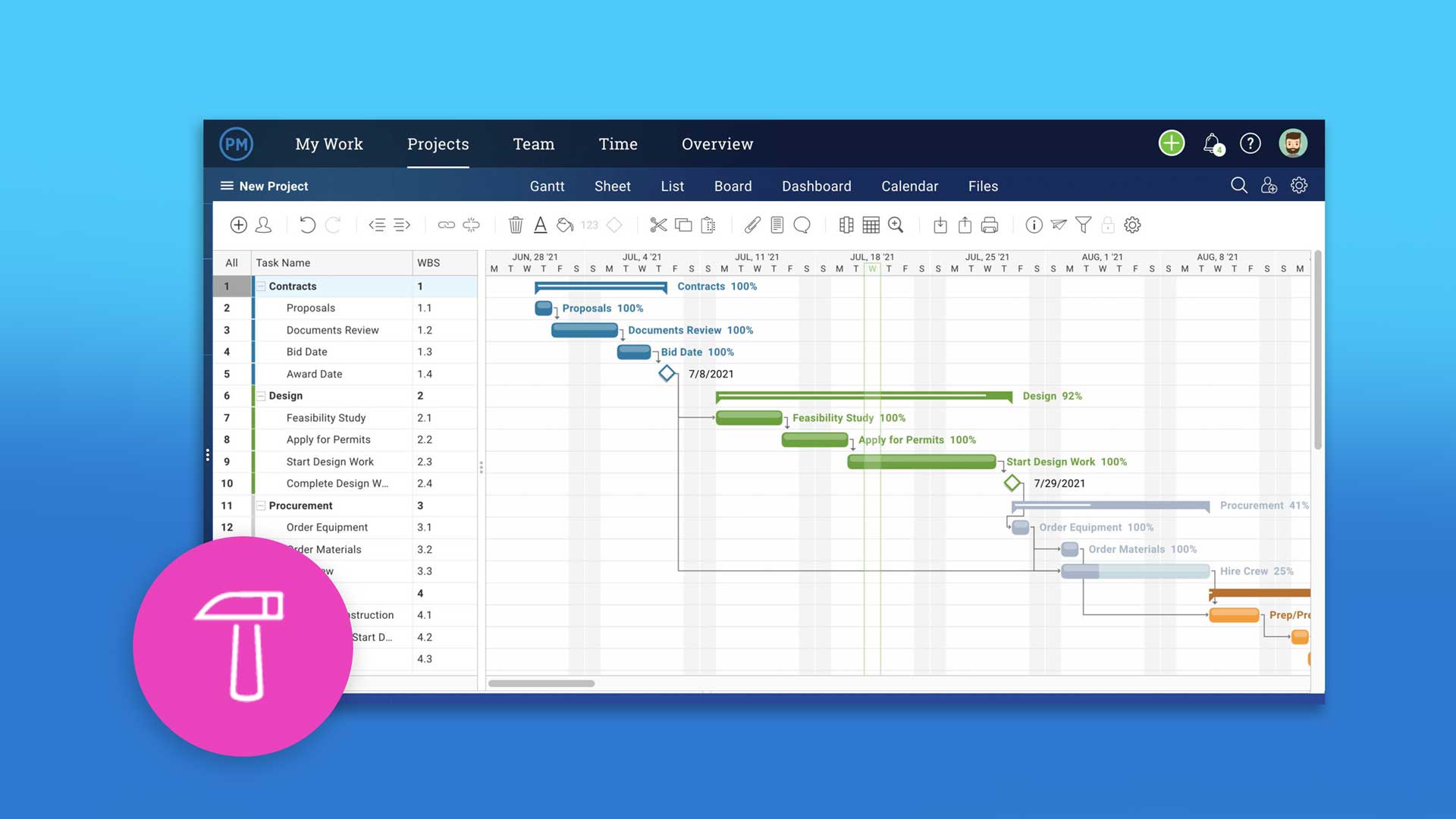
Variations according to product type
Companies should offer a broad range of products to consumers in order to maximize their performance. However, they often launch product variations without knowing whether they will add complexity to their supply chains. Consumer-goods companies saw a 60 percent increase in the number of new products that they introduced each year from 2002 to 2011. Although this increased demand led to an increase in sales, it also led to higher costs for the supply chain. For example, U.S. consumer goods companies increased their annual number of new products by 60 percent during the same period. This inevitably pushed up costs in many areas of the company's supply chain, but at a steady rate of only 2.8 percent per year.
FAQ
What can a manager do to improve his/her management skillset?
Through demonstrating good management skills at every opportunity
Managers need to monitor their subordinates' performance.
You should immediately take action if you see that your subordinate is not performing as well as you would like.
It is important to be able identify areas that need improvement and what can be done to improve them.
Six Sigma is so beloved.
Six Sigma is easy and can deliver significant results. It also provides a framework for measuring improvements and helps companies focus on what matters most.
What is the meaning of "project management?"
We mean managing the activities involved in carrying out a project.
These include planning the scope and identifying the needs, creating the budget, organizing the team, scheduling the work and monitoring progress. Finally, we close down the project.
How can a manager motivate employees?
Motivation can be defined as the desire to achieve success.
It is possible to be motivated by doing something you enjoy.
Or you can get motivated by seeing yourself making a contribution to the success of the organization.
If you are a doctor and want to be one, it will likely be more rewarding to see patients than to read medical books every day.
Another type of motivation comes from within.
One example is a strong sense that you are responsible for helping others.
Maybe you like working hard.
Ask yourself why you aren't feeling motivated.
Next, think of ways you can improve your motivation.
What is the difference in Six Sigma and TQM?
The key difference between the two quality management tools is that while six-sigma focuses its efforts on eliminating defects, total quality management (TQM), focuses more on improving processes and reducing cost.
Six Sigma is an approach for continuous improvement. This method emphasizes eliminating defects using statistical methods such p-charts, control charts, and Pareto analysis.
This method seeks to decrease variation in product output. This is done by identifying and correcting the root causes of problems.
Total quality management refers to the monitoring and measurement of all aspects in an organization. Training employees is also part of total quality management.
It is used to increase productivity.
What is TQM, exactly?
The industrial revolution saw the realization that prices alone were not sufficient to sustain manufacturing companies. This led to the birth of quality. They had to improve efficiency and quality if they were to remain competitive.
Management realized the need to improve and created Total Quality Management, which focused on improving all aspects within an organization's performance. It included continuous improvement, employee involvement and customer satisfaction.
Statistics
- As of 2020, personal bankers or tellers make an average of $32,620 per year, according to the BLS. (wgu.edu)
- 100% of the courses are offered online, and no campus visits are required — a big time-saver for you. (online.uc.edu)
- The average salary for financial advisors in 2021 is around $60,000 per year, with the top 10% of the profession making more than $111,000 per year. (wgu.edu)
- The profession is expected to grow 7% by 2028, a bit faster than the national average. (wgu.edu)
- Hire the top business lawyers and save up to 60% on legal fees (upcounsel.com)
External Links
How To
How do I do the Kaizen Method?
Kaizen means continuous improvement. Kaizen is a Japanese concept that encourages constant improvement by small incremental changes. This is a collaborative process in which people work together to improve their processes continually.
Kaizen, a Lean Manufacturing method, is one of its most powerful. The concept involves employees responsible for manufacturing identifying problems and trying to fix them before they become serious issues. This will increase the quality and decrease the cost of the products.
Kaizen is a way to raise awareness about what's happening around you. It is important to correct any problems immediately if they are discovered. It is important that employees report any problems they see while on the job to their managers.
Kaizen has a set of basic principles that we all follow. When working with kaizen, we always start with the end result and move towards the beginning. To improve our factory, for example, we need to fix the machines that produce the final product. Next, we repair the machines that make components. Then, the machines that make raw materials. Then, we fix those who work directly with the machines.
This approach is called 'kaizen' because it focuses on improving everything steps by step. After we're done with the factory, it's time to go back and fix the problem.
You need to know how to measure the effectiveness of kaizen within your business. There are several ways that you can tell if your kaizen system is working. Another method is to see how many defects are found on the products. Another method is to determine how much productivity has improved since the implementation of kaizen.
A good way to determine whether kaizen has been implemented is to ask why. It was because of the law, or simply because you wanted to save some money. It was a way to save money or help you succeed.
If you answered yes to any one of these questions, congratulations! You are ready to start kaizen.