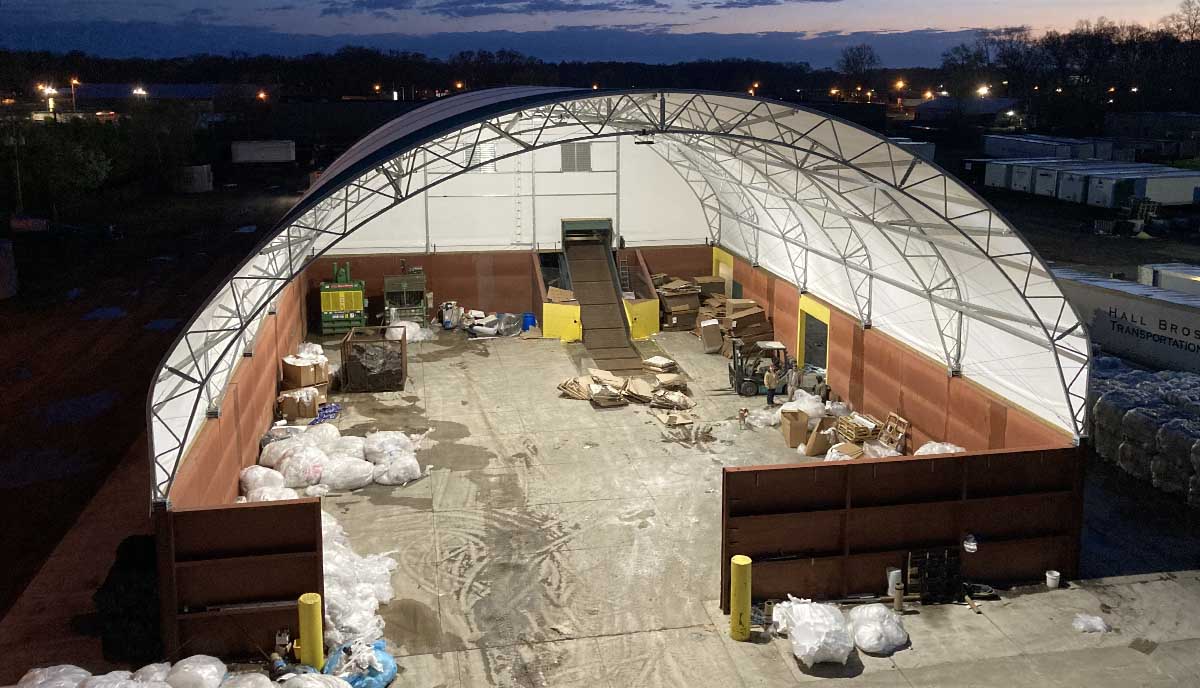
Micromanaging at work is unacceptable and can even be dangerous. It is a sign of a toxic workplace. Micromanagement is also a violation of basic human rights. Avoid working for such toxic bosses by being aware of your rights and not compromising them. If you feel that a micromanager is violating your basic rights, it's possible to call him out. You should not allow it to become a stressful and frightening experience to confront a boss. You have many options to handle bosses like these.
Disadvantages of micromanaging
Micromanagement can be a destructive work style and undermine trust between the bosses. Employees who lack trust lose motivation and perform less well than they would otherwise. This can lead to high-performing employees being fired. This is a negative workplace environment that must be avoided if you want employees who work well.
Micromanaging creates distrust. Micromanaging will make you look like a despot and can cause a breakdown in the relationships between employees. This can negatively impact both productivity as well as the longevity of an employee’s employment. Trust is a twoway street. It is critical for building a positive working relationship.
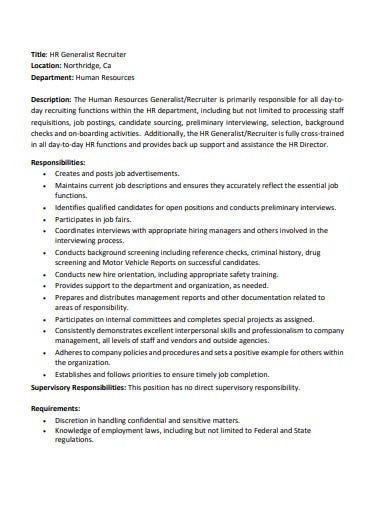
Signs of micromanaging
Micromanaging is a management style that focuses on the smallest details while constantly monitoring the progress of employees. This management style can lead to dissatisfaction and a decrease in productivity. Micromanagers often require detailed progress reports from employees and criticize them for their work without taking into account the context.
Micromanaging can also cause a lack of trust in employees, as a micromanager often refuses to delegate. They might need more frequent updates or meetings.
Micromanaging's effects on employees
Micromanagement can negatively impact employees' morale. It makes employees feel like failures which causes them to quit trying. Ultimately, employees will lose motivation and initiative, and their job satisfaction will plummet. Micromanagement can also negatively impact an employee's personal life, damaging relationships.
Employee innovation can be stifled by micromanagement. This discourages employees to come up with new ideas or step outside their job descriptions. It can also make employees feel unsafe, which can result in increased staff turnover.
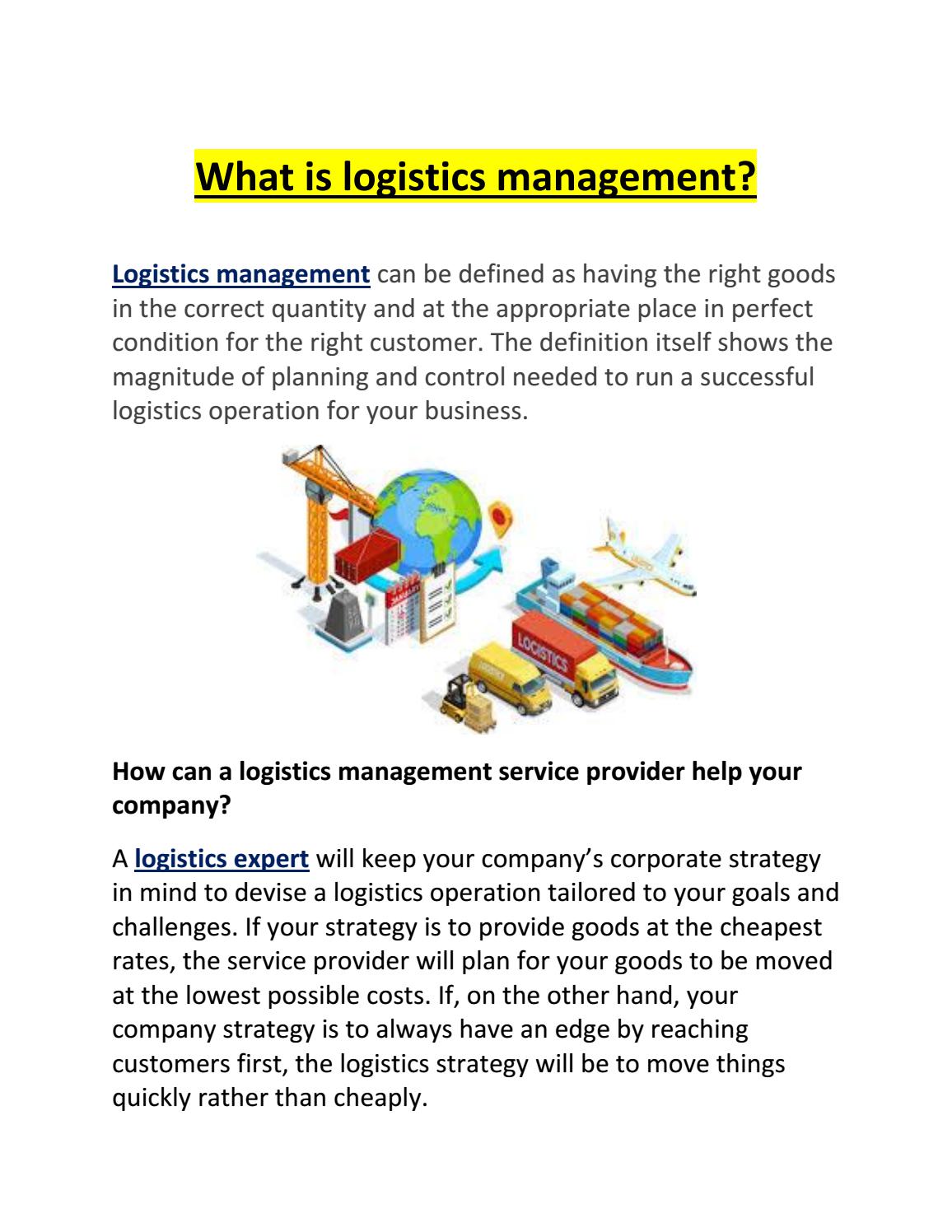
How to deal with micromanaging bosses
Dealing with a micromanaging boss can be stressful, but there are many ways to deal with this type of boss. First, remember that micromanagers often do what they do because of their own anxieties. Don't be afraid to share details, even if you feel that doing so could delay the project.
A good way to approach a micromanager is by questioning their motives. Many micromanagers are good-hearted and care about the work of their employees. You can ask them questions to find out if they are being unreliable or trusting.
FAQ
Why is project management so important?
Project management techniques ensure that projects run smoothly while meeting deadlines.
This is because many businesses depend heavily upon project work to produce products and services.
These projects must be managed efficiently and effectively by companies.
Companies can lose time, money, and reputation if they don't have a good project management system.
What is the difference between TQM and Six Sigma?
The major difference between the two tools for quality management is that six Sigma focuses on eliminating defect while total quality control (TQM), on improving processes and decreasing costs.
Six Sigma is an approach for continuous improvement. This approach emphasizes eliminating defects through statistical methods like control charts, Pareto analysis, and p-charts.
The goal of this method is to reduce variation in product output. This is done by identifying root causes and rectifying them.
Total quality management involves measuring and monitoring all aspects of the organization. It also involves training employees to improve performance.
It is often used to increase productivity.
What do we mean when we say "project management"?
That is the management of all activities associated with a project.
This includes defining the scope, identifying the requirements and preparing the budget. We also organize the project team, schedule the work, monitor progress, evaluate results, and close the project.
What are the five management process?
The five stages of any business are planning, execution, monitoring, review, and evaluation.
Planning means setting goals for the long-term. Planning includes setting goals for the future.
Execution is the actual execution of the plans. They must be followed by all parties.
Monitoring is a way to track progress towards your objectives. Regular reviews should be done of your performance against targets or budgets.
Every year, there are reviews. They are a chance to see if everything went smoothly during the year. If not, it is possible to make improvements for next year.
Following the annual review, evaluation is done. It helps you identify the successes and failures. It also provides feedback on the performance of people.
Statistics
- The average salary for financial advisors in 2021 is around $60,000 per year, with the top 10% of the profession making more than $111,000 per year. (wgu.edu)
- As of 2020, personal bankers or tellers make an average of $32,620 per year, according to the BLS. (wgu.edu)
- UpCounsel accepts only the top 5 percent of lawyers on its site. (upcounsel.com)
- The BLS says that financial services jobs like banking are expected to grow 4% by 2030, about as fast as the national average. (wgu.edu)
- 100% of the courses are offered online, and no campus visits are required — a big time-saver for you. (online.uc.edu)
External Links
How To
How can you implement the Kaizen technique?
Kaizen means continuous improvement. This term was first used by Toyota Motor Corporation in the 1950s. It refers to the Japanese philosophy that emphasizes continuous improvement through small incremental changes. It's a team effort to continuously improve processes.
Kaizen is one of the most effective methods used in Lean Manufacturing. This concept requires employees to identify and solve problems during manufacturing before they become major issues. This improves the quality of products, while reducing the cost.
Kaizen is an approach to making every worker aware and alert to what is happening around them. If something is wrong, it should be corrected immediately so that no problem occurs. Report any problem you see at work to your manager.
When doing kaizen, there are some principles we must follow. We always start from the end product and move toward the beginning. To improve our factory, for example, we need to fix the machines that produce the final product. First, we fix machines that produce components. Next, we fix machines that produce raw material. Finally, we repair the workers who are directly involved with these machines.
This is known as "kaizen", because it emphasizes improving each step. Once we have finished fixing the factory, we return to the beginning and work until perfection.
Before you can implement kaizen into your business, it is necessary to learn how to measure its effectiveness. There are many methods to assess if kaizen works well. One of these ways is to check the number of defects found on the finished products. Another way to find out how productive your company has been since you implemented kaizen is to measure the increase in productivity.
If you want to find out if your kaizen is actually working, ask yourself why. It was because of the law, or simply because you wanted to save some money. Did you really believe it would lead to success?
If you answered yes to any one of these questions, congratulations! Now you're ready for kaizen.