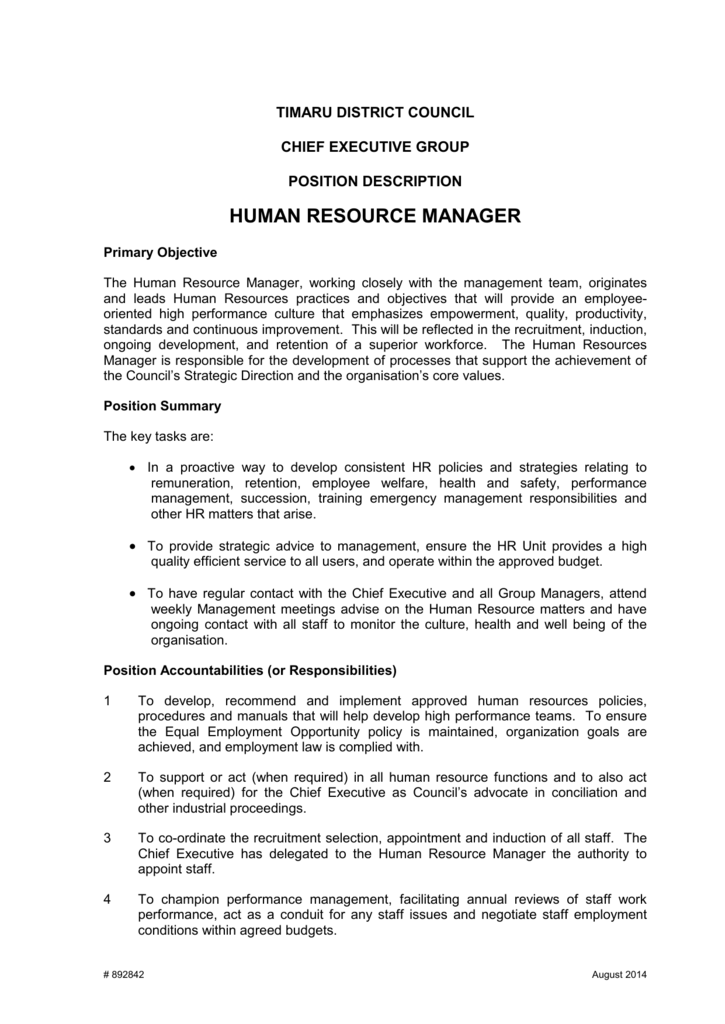
The key elements of a strategic change management plan must include the following. These are communication, adaptability, SWOT analysis, and adaptation. An initial step is to assess all existing materials. Once you have this information, you can begin planning your change management strategy. Next, you need to identify your target audiences and message.
A strategic management plan for change is based on key elements
A strategic change management plan has several elements, and a key element is stakeholder engagement. Engaging key stakeholders, such as employees, to discuss the reasons for a change is important, is a key part of this process. This involves communicating the benefits and pitfalls of a new approach to doing business. The plan should be measured and have a baseline that can measure the success or failure of the change.
It should include the necessary resources to implement the change. The change management process works in the same way as a general project plan. Once the planning phase is complete, the documented roadmap will emerge. By creating a change management strategy, scope creep can be controlled and risks minimized. Plan should include roadblocks and unanticipated events. The plan should be flexible enough that it can accommodate unexpected obstacles.
Adaptability
The ability to adapt and change quickly is what adaptive change refers to. It involves the creation flexible structures as well as dispersed decisions rights. It begins by identifying the organizational needs and then choosing, amplifying, refining and refining the best solutions. This approach requires that organizations create an environment which encourages free and open communication as well constructive conflict and risk-taking.
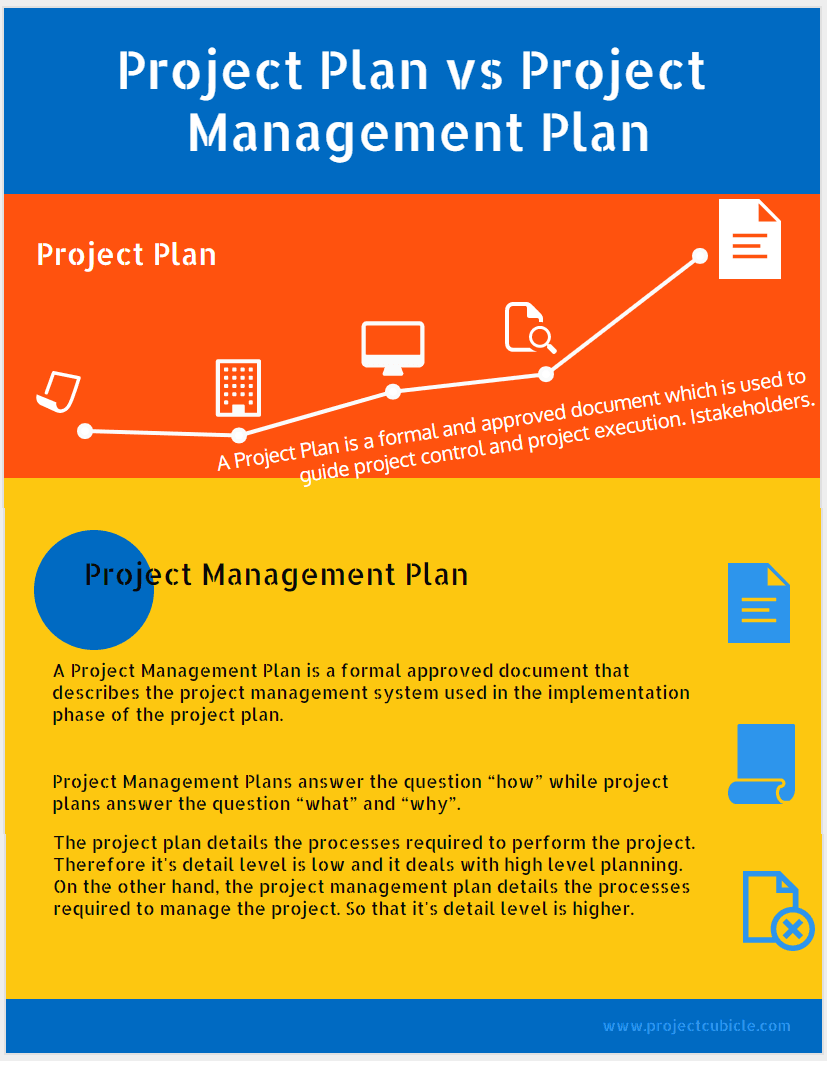
An organization must be able to identify signs of change and interpret them quickly to adapt. Companies need to be able change quickly in order to adapt their strategy and business models or to alter the information landscape.
Communication
Communication is one of the most crucial aspects of managing strategic changes. Employees should be able communicate their opinions. Communicating your changes and policies through the appropriate channels will ensure that they are fully committed to the new direction of business. There are many channels to communicate changes, including email and face-to-face meetings. To ensure the message is remembered, it's important to know which channels are preferred by your employees.
Video content can be used to explain changes depending on the nature of them. It is possible to create a dedicated intranet area for information about change. This space could host training materials, information sheets, discussion forums, employee feedback, as well as fact sheets.
SWOT analysis
SWOT analysis allows you to identify weaknesses and potential opportunities for change in an organization. This helps identify external factors that can make an organization vulnerable, such as bad credit and cash-flow issues. It can also show how even a slight change in the market can impact a business' bottom line. Although Albert S. Humphrey is often credited with the creation of this type analysis, it has been debated and the TOWS Matrix also claimed to be its creator.
An organization's ability to achieve its strategic goals can be assessed using a SWOT analysis. This is a great tool to develop a broad perspective and a detailed strategic evaluation. The Stanford Research Institute performed research in the 1960s that resulted in the SWOT framework. This research was commissioned by several Fortune 500 companies. Its authors were Robert Stewart, Marion Dosher and Albert Humphrey. Du Pont also completed a SWOT analysis. It was this analysis that paved the way for corporate planning. Soon thereafter, every Fortune 500 firm had a corporate planner and there were long-range strategic planning organizations across the USA.
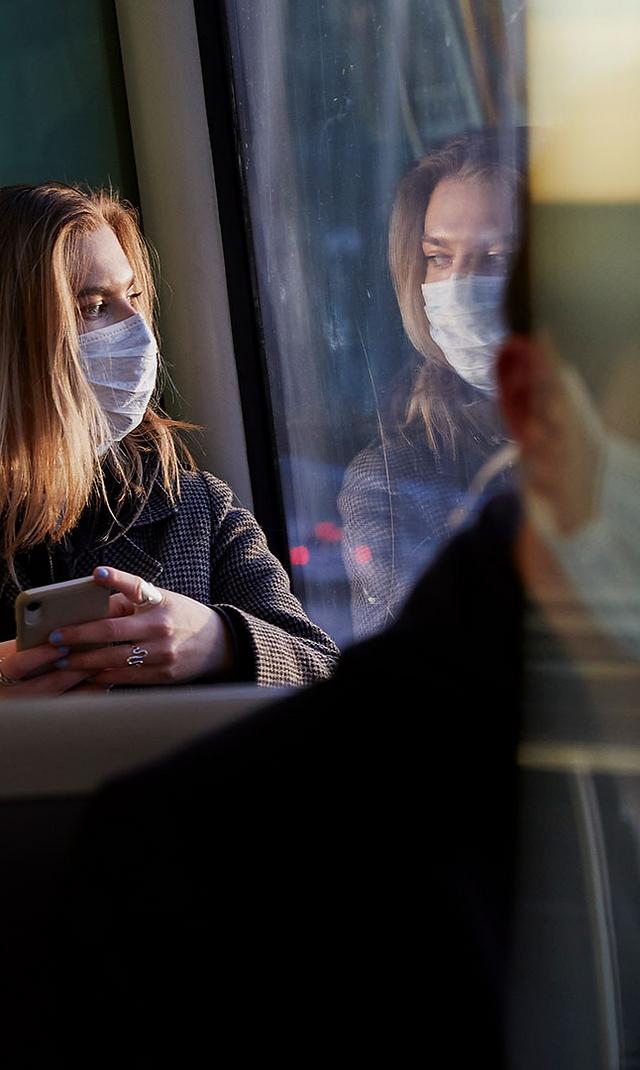
Employee engagement
Engaging employees is essential to strategic change management. Without employee engagement, it is possible to make the change process more difficult. It can also lead to lower morale, decreased adoption of the change, and increased attrition. Organisations must therefore take proactive steps to ensure employee engagement throughout the change process to avoid this negative outcome. Employee engagement is defined as their overall emotional reaction to their job and their employer. This will translate into employees' behavior at work.
Managers must get to understand their employees. This will help them achieve high levels in engagement. Managers must know their employees' strengths and weaknesses so they can give them opportunities to showcase them. They should discuss the value of each member of the team and how they contribute to the company's success. They should also be able to align their work with the strengths of each team member. This will maximize the contributions of each employee to the company.
FAQ
How does Six Sigma work
Six Sigma uses statistical analyses to locate problems, measure them, analyze root cause, fix problems and learn from the experience.
The first step in solving a problem is to identify it.
The data is then analyzed and collected to identify trends.
The problem is then rectified.
Final analysis of data is done to determine if the problem has been solved.
This cycle continues until there is a solution.
What are the 5 management processes?
These five stages are: planning, execution monitoring, review and evaluation.
Setting goals for the future is part of planning. This includes setting goals for the future and defining what you want.
Execution happens when you actually do the plan. These plans must be adhered to by everyone.
Monitoring is a way to track progress towards your objectives. Regular reviews of performance against budgets and targets should be part of this process.
Each year, reviews are held at the end. They are a chance to see if everything went smoothly during the year. If not, then it may be possible to make adjustments in order to improve performance next time.
Following the annual review, evaluation is done. It helps you identify the successes and failures. It also provides feedback on the performance of people.
What can a manager do to improve his/her management skillset?
It is important to have good management skills.
Managers must monitor the performance of subordinates constantly.
You must quickly take action if your subordinate fails to perform.
It is important to be able identify areas that need improvement and what can be done to improve them.
What is the difference between a project and a program?
A project is temporary; a program is permanent.
Projects usually have a goal and a deadline.
It is often carried out by a team of people who report back to someone else.
A program is usually defined by a set or goals.
It is usually done by one person.
Statistics
- Our program is 100% engineered for your success. (online.uc.edu)
- UpCounsel accepts only the top 5 percent of lawyers on its site. (upcounsel.com)
- Hire the top business lawyers and save up to 60% on legal fees (upcounsel.com)
- Your choice in Step 5 may very likely be the same or similar to the alternative you placed at the top of your list at the end of Step 4. (umassd.edu)
- The profession is expected to grow 7% by 2028, a bit faster than the national average. (wgu.edu)
External Links
How To
How can Lean Manufacturing be done?
Lean Manufacturing uses structured methods to reduce waste, increase efficiency and reduce waste. They were created by Toyota Motor Corporation in Japan in the 1980s. The main goal was to produce products at lower costs while maintaining quality. Lean manufacturing seeks to eliminate unnecessary steps and activities in the production process. It has five components: continuous improvement and pull systems; just-in time; continuous change; and kaizen (continuous innovation). Pull systems are able to produce exactly what the customer requires without extra work. Continuous improvement involves constantly improving upon existing processes. Just-in time refers to components and materials being delivered right at the place they are needed. Kaizen means continuous improvement. Kaizen involves making small changes and improving continuously. Finally, 5S stands for sort, set in order, shine, standardize, and sustain. To achieve the best results, these five elements must be used together.
Lean Production System
Six key concepts form the foundation of the lean production system:
-
Flow - focuses on moving information and materials as close to customers as possible.
-
Value stream mapping: This is a way to break down each stage into separate tasks and create a flowchart for the entire process.
-
Five S’s - Sorted, In Order. Shine. Standardize. And Sustain.
-
Kanban: Use visual signals such stickers, colored tape, or any other visual cues, to keep track your inventory.
-
Theory of Constraints - Identify bottlenecks in the process, and eliminate them using lean tools such kanban boards.
-
Just-intime - Order components and materials at your location right on the spot.
-
Continuous improvement - Make incremental improvements rather than overhauling the entire process.