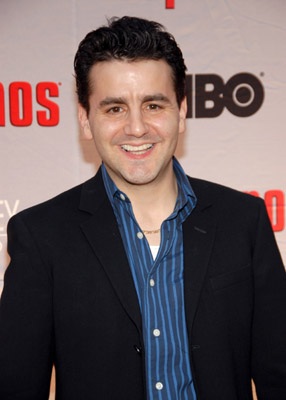
You're likely familiar with teamwork if you've ever been asked for leadership. Efficient leaders are able to see and plan for success, in addition to the skills that make teams work well. The best leaders give their staff specific steps to reach their goals. The eLearning courses available today can help you transform your boss from a servant leader. These skills can be applied to your career.
Leadership requires teamwork
Team success is dependent on the ability to communicate well and being committed to teamwork. Trust and respect are fostered by team leaders who empower others and hold them accountable. Leadership is an essential part of teamwork. You should practice listening skills if you are a leader of a team. You should make it easy for team members to share their ideas. These are the essential characteristics for effective teamwork:
Leadership skills include the ability to commit.
People look up to leaders for their commitment. Leaders who show commitment to a mission and/or task will inspire others. The key word here is "commitment". Commitment is contagious. When others see it, they will want to emulate it. The key leadership skill is commitment. How can you encourage commitment within your team? These are the three best ways to instill commitment in your group. All three require mental toughness.
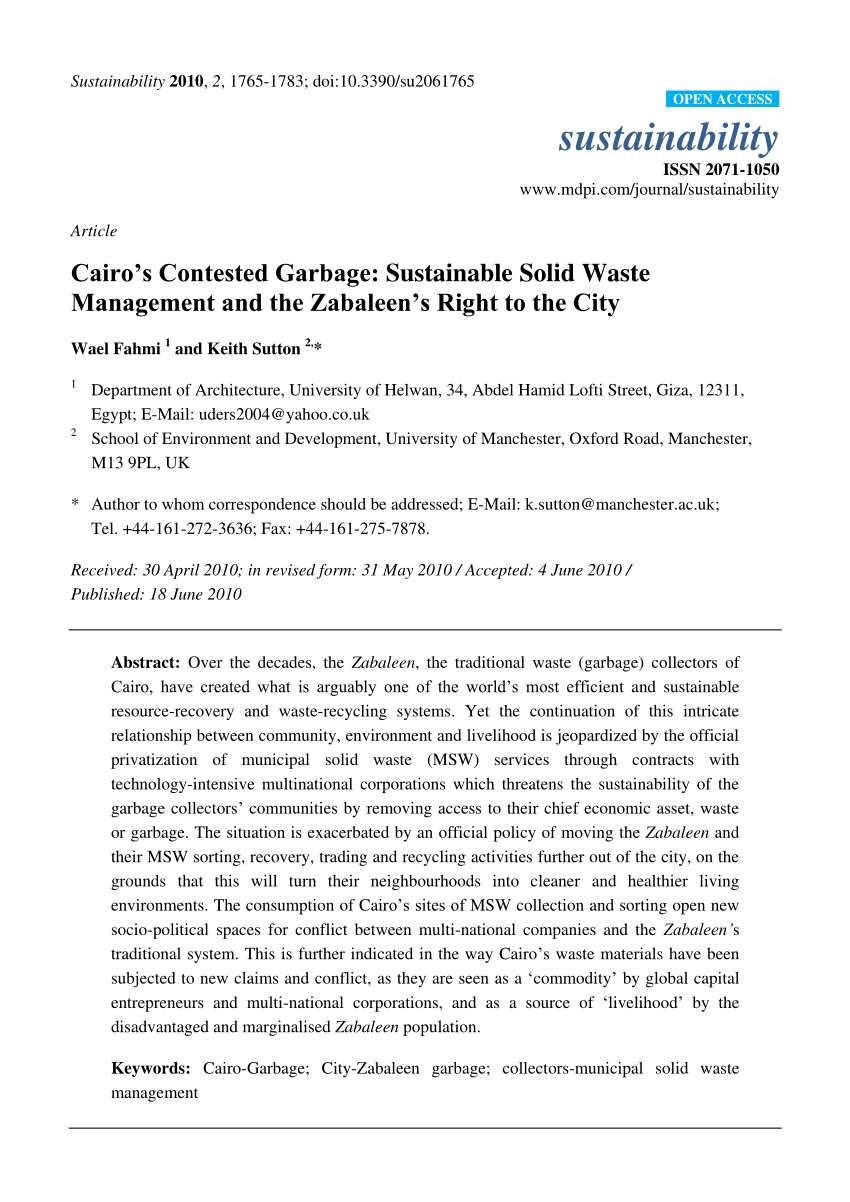
Leadership skills include creativity
Creative thinking is essential if you want to be a leader. According to the Cambridge dictionary creative is defined as the ability or ability to invent new ideas and solve problems. Many leaders throughout history have created books that restrict the way they can lead their teams. The 21st Century has seen creativity become more important due to the constant changes in the world. Many leaders still believe in the old rules of order and structure.
Integrity is a leadership ability
Leadership requires a high standard of integrity. Your actions and beliefs should reflect the values you hold as a leader. If you fail to do your part, the results will reflect poorly. Failing to listen can be just as detrimental as not speaking up for your beliefs. To retain employees and attract talent, you need to be trustworthy in your actions. Leaders who live up to their values will inspire their employees and help them achieve their goals.
Communication skills are essential for leadership.
Effective communication skills are vital for effective leadership. A leader who is able to motivate and inspire others toward a common goal will be a great leader. Without good communication skills, it's nearly impossible for you to reach your team members. For you to succeed as a leader, communication is key. These are tips to help you improve communication skills and be a better leader.
Leadership requires empathy
Leaders must be able to relate to others and understand their situations. Managers will be able to spot productivity issues and help employees thrive. Empathy is essential. Employees will follow managers who have empathy and are motivated by a common goal. Empathy among employees is a key leadership skill. Here are some reasons you should learn this skill. Here are some tips to help you and your team develop empathy.
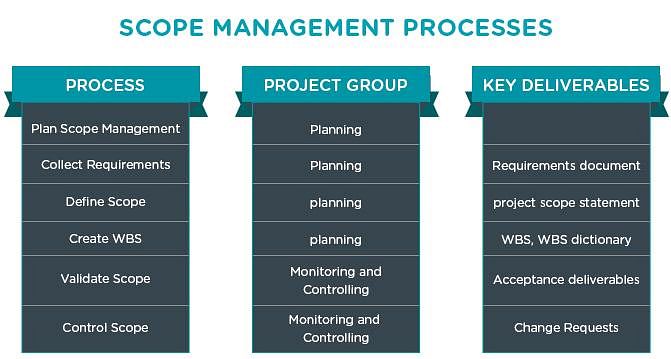
Leadership skills include time management
People who are skilled at managing their time have a clear idea of what they want. You can achieve your desired outcome by setting goals and breaking down the responsibilities. Good communication skills are key to time management. Effective time management means setting limits and saying "no” to things you don't have time for. This allows for you to put your focus on the most important tasks instead of wasting time on irrelevant activities. Another key to managing your time is keeping a current calendar.
Strategic thinking is a leadership skill
Discussions between team members are a great way for strategic thinking to be developed. These conversations help you refine your strategy and protect against biases and blind spots. Communication and trust are the keys to effective discussions. Jack Canfield once said, "Great preparation and strategy make your own luck." You can improve your leadership skills and create a cohesive team by learning from your team.
Conflict resolution is a leadership skill
Leaders must have the ability manage conflict. This skill can help you rise to the top of your profession and also allow you to disrupt the momentum within your team or company. A toxic workplace can emerge when a conflict festers unchecked for long. While conflict management may seem simple, it requires a high level of understanding of the broader ecosystem in which a conflict may exist. When a conflict does occur, a leader must recognize how his or her actions will impact other agendas.
FAQ
What does Six Sigma mean?
Six Sigma uses statistical analysis for problems to be found, measured, analyzed root causes, corrected, and learned from.
The first step is identifying the problem.
The next step is to collect data and analyze it in order to identify trends or patterns.
Next, corrective steps are taken to fix the problem.
Finally, the data are reanalyzed in order to determine if it has been resolved.
This continues until the problem has been solved.
How do you define Six Sigma?
Six-sigma will be well-known to anyone who has worked in operations research or statistics. Anyone involved in business can benefit.
Because it requires a high level of commitment, only those with strong leadership skills will make an effort necessary to implement it successfully.
What are the steps that management takes to reach a decision?
Managers are faced with complex and multifaceted decisions. It involves many elements, including analysis, strategy. planning. implementation. measurement. evaluation. feedback.
Management of people requires that you remember that they are just as human as you are, and can make mistakes. You can always improve your performance, provided you are willing to make the effort.
This video explains the process of decision-making in Management. We discuss the different types of decisions and why they are important, every manager should know how to navigate them. You'll learn about the following topics:
What is Six Sigma, exactly?
It's an approach to quality improvement that emphasizes customer service and continuous learning. It is a method that eliminates defects using statistical techniques.
Motorola's 1986 efforts to improve manufacturing process efficiency led to the creation of Six Sigma.
The idea spread quickly throughout the industry, and today, many organizations are using six sigma methods to improve product design, production, delivery, and customer service.
What are the five management process?
The five stages of any business are planning, execution, monitoring, review, and evaluation.
Planning means setting goals for the long-term. Planning includes setting goals for the future.
Execution occurs when you actually carry out the plans. They must be followed by all parties.
Monitoring is checking on progress towards achieving your objectives. Regular reviews of performance against budgets and targets should be part of this process.
At the end of every year, reviews take place. They give you an opportunity to review the year and assess how it went. If not, then it may be possible to make adjustments in order to improve performance next time.
Evaluation takes place after the annual review. It helps identify which aspects worked well and which didn't. It also provides feedback on the performance of people.
How can we make our company culture successful?
Successful company culture is one where people feel valued and respected.
It's based on three main principles:
-
Everyone has something valuable to contribute
-
Fair treatment of people is the goal
-
People and groups should respect each other.
These values can be seen in the behavior of people. They will show consideration and courtesy to others.
They will listen to other people's opinions respectfully.
And they will encourage others to share ideas and feelings.
In addition, the company culture encourages open communication and collaboration.
People feel comfortable expressing their opinions freely without fear of reprisal.
They are aware that mistakes can be accepted if they are treated honestly.
The company culture promotes honesty, integrity, and fairness.
Everyone knows that they must always tell the truth.
Everyone understands there are rules that they must follow.
Everyone does not expect to receive special treatment.
What is Kaizen, exactly?
Kaizen is a Japanese term for "continuous improvement." It encourages employees constantly to look for ways that they can improve their work environment.
Kaizen is a belief that everyone should have the ability to do their job well.
Statistics
- The BLS says that financial services jobs like banking are expected to grow 4% by 2030, about as fast as the national average. (wgu.edu)
- Our program is 100% engineered for your success. (online.uc.edu)
- This field is expected to grow about 7% by 2028, a bit faster than the national average for job growth. (wgu.edu)
- The profession is expected to grow 7% by 2028, a bit faster than the national average. (wgu.edu)
- Hire the top business lawyers and save up to 60% on legal fees (upcounsel.com)
External Links
How To
How is Lean Manufacturing done?
Lean Manufacturing techniques are used to reduce waste while increasing efficiency by using structured methods. They were developed by Toyota Motor Corporation in Japan during the 1980s. It was designed to produce high-quality products at lower prices while maintaining their quality. Lean manufacturing focuses on eliminating unnecessary steps and activities from the production process. It is composed of five fundamental elements: continuous improvement; pull systems, continuous improvements, just-in–time, kaizen, continuous change, and 5S. It is a system that produces only the product the customer requests without additional work. Continuous improvement is the continuous improvement of existing processes. Just-in-time is when components and other materials are delivered at their destination in a timely manner. Kaizen means continuous improvement. Kaizen involves making small changes and improving continuously. Five-S stands for sort. It is also the acronym for shine, standardize (standardize), and sustain. These five elements are combined to give you the best possible results.
Lean Production System
Six key concepts make up the lean manufacturing system.
-
Flow is about moving material and information as near as customers can.
-
Value stream mapping: This is a way to break down each stage into separate tasks and create a flowchart for the entire process.
-
Five S's - Sort, Set In Order, Shine, Standardize, and Sustain;
-
Kanban – visual signals like colored tape, stickers or other visual cues are used to keep track inventory.
-
Theory of constraints: identify bottlenecks in your process and eliminate them using lean tools, such as kanban board.
-
Just-in time - Get components and materials delivered right at the point of usage;
-
Continuous improvement - incremental improvements are made to the process, not a complete overhaul.