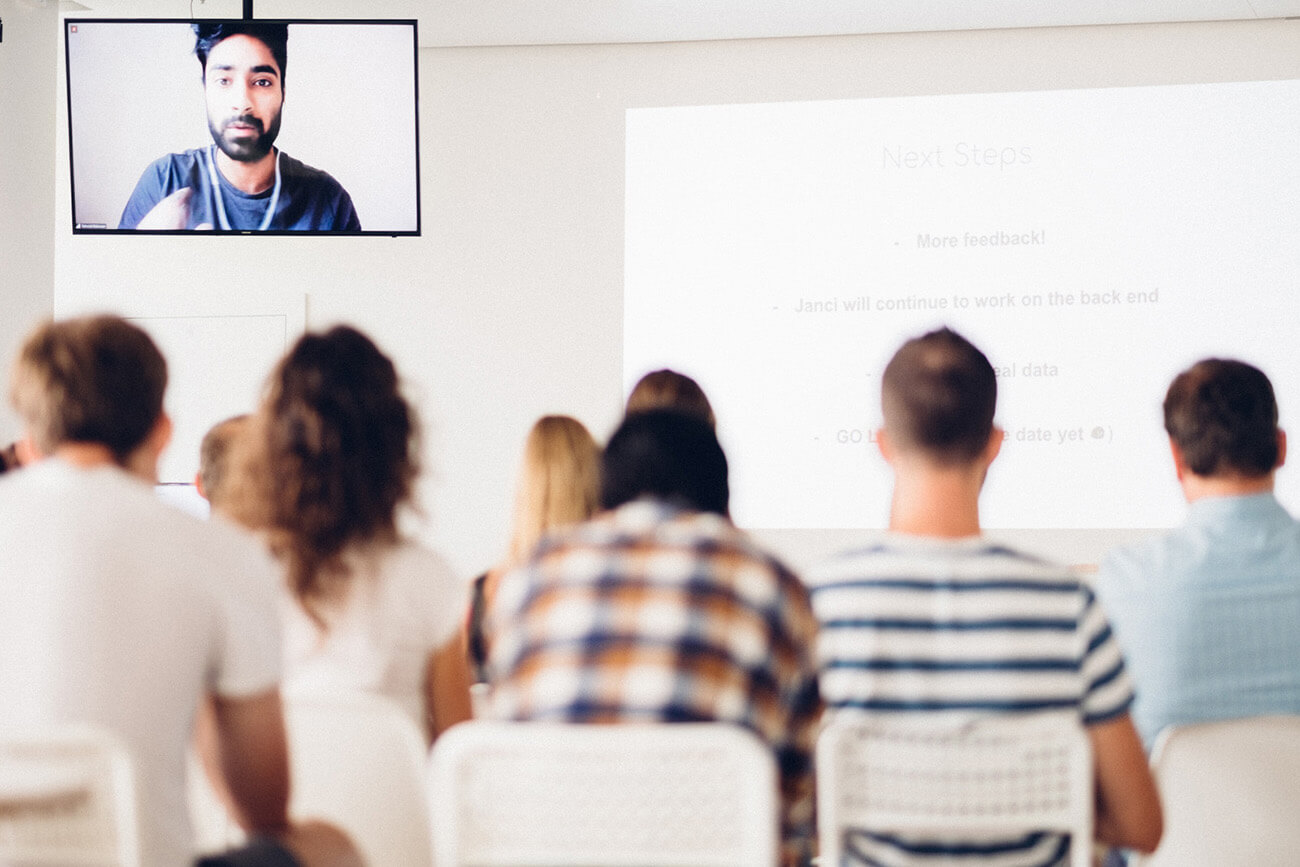
The process of managing projects can be confusing and time-consuming. This article will cover the basics of project management. Learn how to organize your project and stay on budget. This article will also help you communicate effectively with stakeholders. Anyone working on a project can benefit from this article. You will also gain an understanding of the various tools and techniques involved in project management. You'll be able to apply these skills in your own projects.
Resources
Resource management is the use of assets to support the completion of a project. These assets could include people, tools and finances. Most projects require a wide variety of resources. It is important to plan the resources well in advance of a project's start. Lack of resources can cause project failures or delays. There are many tools that can help you plan your resources.
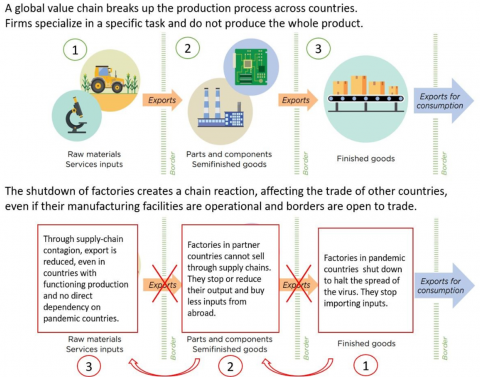
Communication
Project management involves many communication methods. Interactive communication allows for the exchange of ideas or thoughts. Interactive communication is best for situations where there is a need for a prompt response. This type of communication includes publishing information on a website or message board, as well as wikis, repository sites, and message boards. This is the preferred method of communication for project managers because they can see and hear the thoughts of participants.
Stakeholders
Individuals and organizations are considered stakeholder in project management if they have an interest or involvement in the project. The Project Management Institute defines a stakeholder as an individual or group with an interest in the project's outcome. There are many different types of stakeholder, so it's important to determine what each one of them has to say about the project. However, one common way to define a stakeholder is to look at the entire project life cycle, from the beginning to the end.
Budgeting
Budgeting is more than just calculating costs. It includes ethical and empathetic decision making, as well as consideration of the needs and interests of project participants. When planning a project, it is important to plan for future costs and changes in scope, as well as anticipated expenses. It is best to have a baseline budget. The baseline may not contain all the requirements. You might have to pay unexpected fees or visa restrictions.
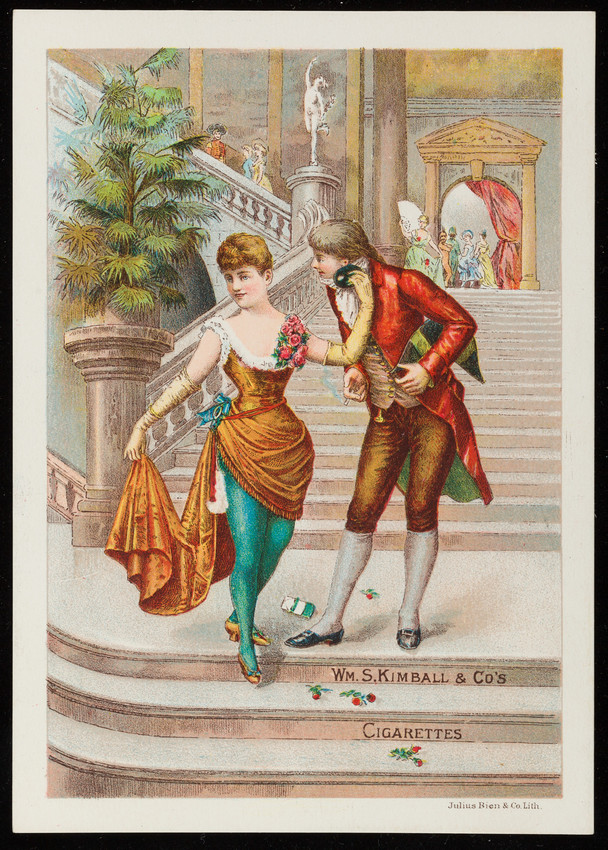
Quality control
Quality control in project management is important to ensure that the deliverables meet customer expectations and are accurate. It is important for project teams to be thorough in their efforts to ensure that they meet the customer's expectations and stay within the scope of their work. Implementing quality control can take time. This involves reviewing work and redoing it, which takes a lot of time. Additionally, not all project managers have the time or resources to go through every step. Yet, quality control in project supervision is essential for a successful venture.
FAQ
What is a basic management tool that can be used for decision-making?
A decision matrix is an easy but powerful tool to aid managers in making informed decisions. It helps them to think strategically about all options.
A decision matrix allows you to represent alternatives as columns and rows. It is easy to see how each option affects the other options.
In this example, we have four possible alternatives represented by the boxes on the left side of the matrix. Each box represents an option. The top row displays the current situation, and the bottom row shows what might happen if nothing is done.
The effect of Option 1 can be seen in the middle column. It would translate into an increase in sales from $2million to $3million.
The following columns illustrate the impact of Options 2 and 3. These are good changes, they increase sales by $1million or $500,000. These positive changes have their downsides. Option 2 increases the cost of goods by $100,000. Option 3 decreases profits and makes them less attractive by $200,000.
Finally, the last column shows the results of choosing Option 4. This results in a decrease of sales by $1,000,000
The best thing about a decision matrix is the fact that you don't have to remember which numbers go with what. You can just glance at the cells and see immediately if one given choice is better.
The matrix already does all the work. It's as easy as comparing numbers in the appropriate cells.
Here's an example showing how you might use a Decision Matrix in your business.
Advertising is a decision that you make. If you do this, you will be able to increase revenue by $5000 per month. But, you will also incur additional expenses of $10 thousand per month.
The net result of advertising investment can be calculated by looking at the cell below that reads "Advertising." It is 15 thousand. Advertising is more valuable than its costs.
What is the difference between Six Sigma Six Sigma and TQM?
The main difference between these two quality-management tools is that six-sigma concentrates on eliminating defects while total QM (TQM), focuses upon improving processes and reducing expenses.
Six Sigma is a methodology for continuous improvement. It emphasizes the elimination and improvement of defects using statistical methods, such as control charts, P-charts and Pareto analysis.
The goal of this method is to reduce variation in product output. This is done by identifying root causes and rectifying them.
Total quality management refers to the monitoring and measurement of all aspects in an organization. It also involves training employees to improve performance.
It is often used as a strategy to increase productivity.
What are the steps to take in order to make a management decision?
Managers are faced with complex and multifaceted decisions. It involves many elements, including analysis, strategy. planning. implementation. measurement. evaluation. feedback.
The key thing to remember when managing people is that they are human beings just as you are and therefore make mistakes. There is always room to improve, especially if your first priority is to yourself.
This video shows you how management makes decisions. We will discuss the various types of decisions, and why they are so important. Every manager should be able to make them. These topics are covered in this course:
What are the five management steps?
Planning, execution, monitoring and review are the five stages of any business.
Planning means setting goals for the long-term. It involves setting goals and making plans.
Execution occurs when you actually carry out the plans. It is important to ensure that everyone follows the plans.
Monitoring is the act of monitoring your progress towards achieving your targets. Regular reviews of performance against budgets and targets should be part of this process.
Every year, there are reviews. These reviews allow you to evaluate whether the year was successful. If not then, you can make changes to improve your performance next year.
After each year's review, evaluation occurs. It helps identify which aspects worked well and which didn't. It also provides feedback on how well people performed.
What are the three main management styles you can use?
The three basic management styles are: authoritarian, laissez-faire, and participative. Each style has its advantages and disadvantages. Which style do your prefer? Why?
Autoritarian - The leader sets direction and expects everyone else to follow it. This style works well if an organization is large and stable.
Laissez-faire – The leader gives each individual the freedom to make decisions for themselves. This style works best when an organization is small and dynamic.
Participative – Leaders are open to suggestions and ideas from everyone. This style works best in smaller organizations where everyone feels valued.
What is TQM, exactly?
The industrial revolution was when companies realized that they couldn't compete on price alone. This is what sparked the quality movement. If they wanted to stay competitive, they needed to improve their quality and efficiency.
In response to this need for improvement, management developed Total Quality Management (TQM), which focused on improving all aspects of an organization's performance. It included continuous improvement and employee involvement as well as customer satisfaction.
What is Six Sigma, exactly?
It's a method for quality improvement that focuses on customer service as well as continuous learning. The goal is to eradicate defects through statistical techniques.
Six Sigma was developed at Motorola in 1986 as part of its efforts to improve manufacturing processes.
The idea spread quickly throughout the industry, and today, many organizations are using six sigma methods to improve product design, production, delivery, and customer service.
Statistics
- UpCounsel accepts only the top 5 percent of lawyers on its site. (upcounsel.com)
- Your choice in Step 5 may very likely be the same or similar to the alternative you placed at the top of your list at the end of Step 4. (umassd.edu)
- The profession is expected to grow 7% by 2028, a bit faster than the national average. (wgu.edu)
- 100% of the courses are offered online, and no campus visits are required — a big time-saver for you. (online.uc.edu)
- The BLS says that financial services jobs like banking are expected to grow 4% by 2030, about as fast as the national average. (wgu.edu)
External Links
How To
How can you implement the Kaizen technique?
Kaizen means continuous improvement. Kaizen is a Japanese concept that encourages constant improvement by small incremental changes. This is a collaborative process in which people work together to improve their processes continually.
Kaizen is one the most important methods of Lean Manufacturing. This concept requires employees to identify and solve problems during manufacturing before they become major issues. This improves the quality of products, while reducing the cost.
Kaizen is a way to raise awareness about what's happening around you. Correct any errors immediately to avoid future problems. If someone is aware of a problem at work, he/she should inform his/her manager immediately.
Kaizen follows a set of principles. When working with kaizen, we always start with the end result and move towards the beginning. If we want to improve our factory for example, we start by fixing the machines that make the final product. First, we fix machines that produce components. Next, we fix machines that produce raw material. Then, we fix those who work directly with the machines.
This is why it's called "kaizen" because it works step-by-step to improve everything. We finish fixing the factory and then go back to the beginning. This continues until we achieve perfection.
Before you can implement kaizen into your business, it is necessary to learn how to measure its effectiveness. There are many ways to tell if kaizen is effective. One of these ways is to check the number of defects found on the finished products. Another way is determining how much productivity increased after implementing kaizen.
A good way to determine whether kaizen has been implemented is to ask why. Is it because the law required it or because you want to save money. You really believed it would make you successful?
Congratulations! You're now ready to get started with kaizen.