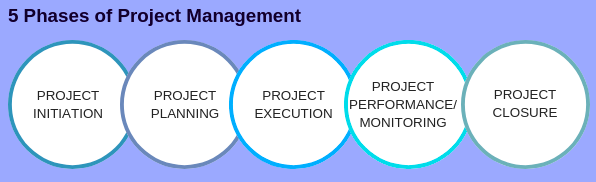
Business process management is a discipline which focuses on improving business processes, and automating them. There are many ways to achieve this goal. There are three main concepts to business process management: modeling, automation, observability. This article will help you learn more about business process management.
Business process management
BPM (business process management) is a method that helps companies manage complexity and make flexible changes to improve customer service. It uses data-driven information for business processes improvement and is an effective method to help companies succeed over the long-term. Ultimately, BPM helps a company digitally transform and stand out from competitors.
A business procedure is a collection of repeatable tasks or events that occur in a business. It is an integral part in running a company. A standardized onboarding workflow can be implemented by an organization to facilitate a smooth transition into a new job. This would include documents, training materials and checklists. It could also automate these tasks.
Business process modeling
Business process modeling allows you to automate and analyze business processes. This process is useful for many reasons. It allows you to identify waste and optimize the flow of processes. It also helps you better understand the business and determine where improvements can be made. It is a process that will save you time and money.
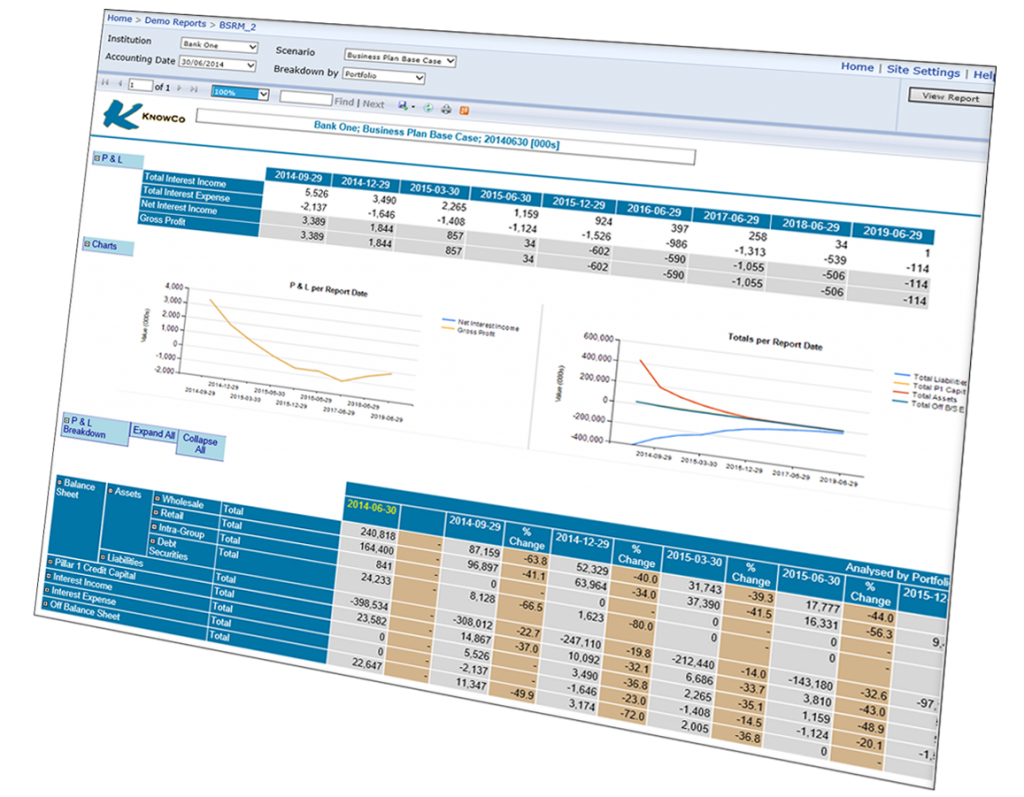
You have many options for facilitating process modeling. Value stream mapping is one of these tools. It highlights key steps and the flow information and materials. This is also known input-process-output modelling. The process flow is, in essence, a functional diagram with inputs, outputs, and relations to the input.
Organisation of business processes
Orchestration is a method for coordinating different processes. Orchestration is a team effort. All participants must be aware of the business process, its operations, and the messages they need to exchange. The process coordinator plays a central role in orchestration. This technique is also used to incorporate web-services into larger business process. This allows you to prepare alternate scenarios in the event of faults.
Process orchestration is still a relatively new technology. Only a few automation products are considered orchestration engine tools. These tools are able to manage many different processes. This is the key difference. Some orchestration tools include REST API adapters which allow for reusable tasks.
Business process monitoring
Business process monitoring software is designed to monitor business processes. It is an application installed in computer systems. The software program helps organizations detect and correct problems in business processes. The software program can help to improve the quality and efficiency of any service or product. The software is available for purchase and can be installed on most computer systems.
Monitoring business processes is a great way for companies to determine the root cause of any problem. They can also identify the processes that are affected and inform all relevant parties about the solutions. Monitoring business processes increases productivity and efficiency for companies.
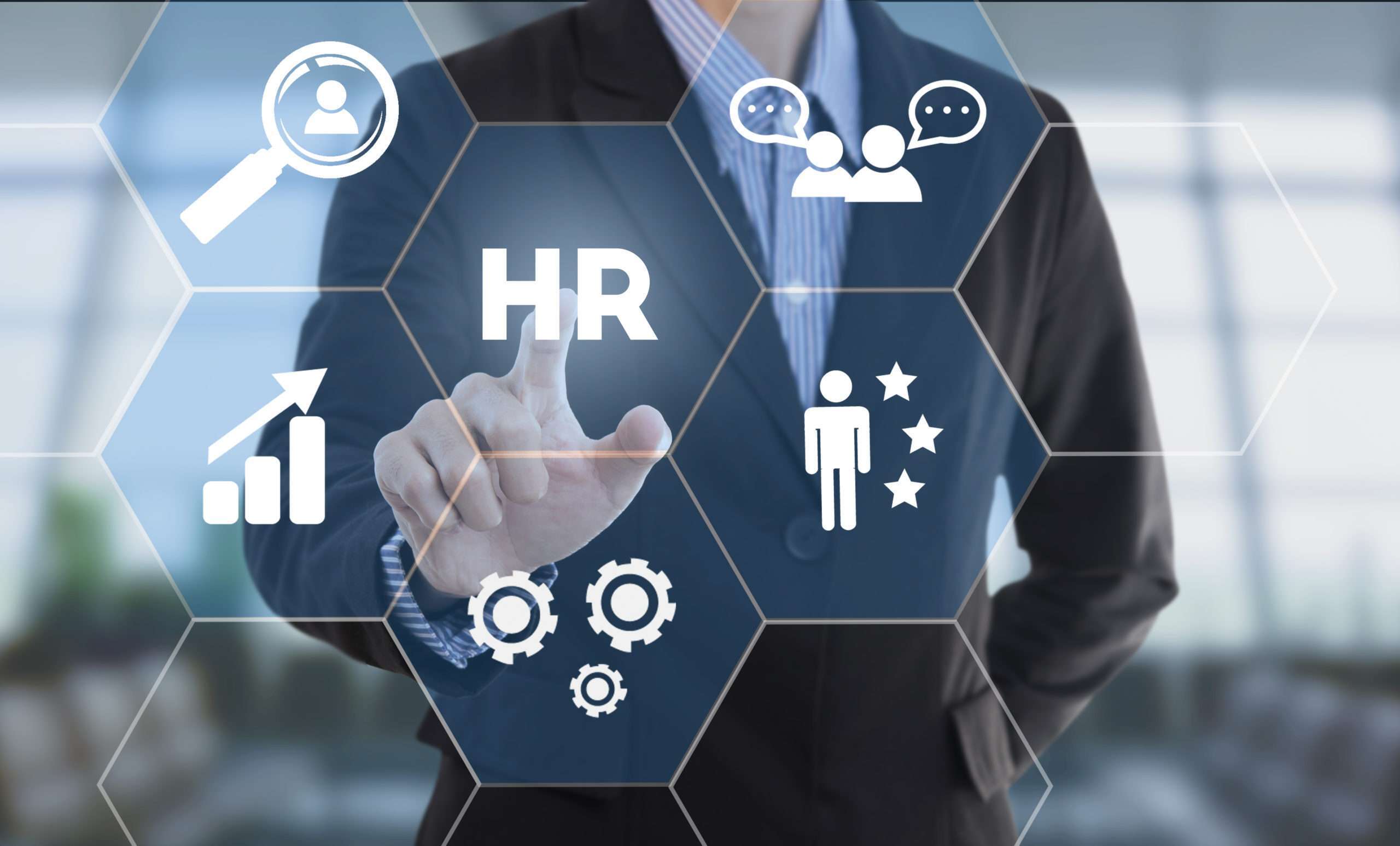
Business process improvement
Business process improvement refers to a method of improving the business's efficiency. The fundamental principles of business process improvement are to minimize inefficiencies and increase performance time. The first step is to identify the problem areas and identify solutions. The involvement of employees as well as stakeholders is essential for business process improvement. This may include introducing new teams, systems or redesigning existing processes. It is essential to test any changes to minimize the risk.
Companies can improve their business processes to increase the quality and value of their products. Customers who are satisfied with their products will be more likely to buy from them again, which leads to increased sales. A happy customer is more likely be a repeat customer, which in turn leads to increased revenue.
FAQ
What is the difference between leadership and management?
Leadership is about inspiring others. Management is about controlling others.
A leader inspires others while a manager directs them.
Leaders motivate people to succeed; managers keep workers on track.
A leader develops people; a manager manages people.
What is Six Sigma?
It's a method for quality improvement that focuses on customer service as well as continuous learning. The objective is to eliminate all defects through statistical methods.
Motorola created Six Sigma as part of their efforts to improve manufacturing processes in 1986.
This idea quickly spread throughout the industry. Today, many organizations use six sigma methods for product design, production and delivery.
What are some of the common mistakes made by managers?
Sometimes managers make it harder for their employees than is necessary.
They may not delegate enough responsibilities to staff and fail to give them adequate support.
In addition, many managers lack the communication skills required to motivate and lead their teams.
Managers set unrealistic expectations and make it difficult for their team.
Managers may prefer to solve every problem for themselves than to delegate responsibility.
What are the three basic management styles?
These are the three most common management styles: participative (authoritarian), laissez-faire (leavez-faire), and authoritarian. Each style has its advantages and disadvantages. Which style do your prefer? Why?
Autoritarian - The leader sets direction and expects everyone else to follow it. This style is best when the organization has a large and stable workforce.
Laissez-faire - The leader allows each individual to decide for him/herself. This style works best when an organization is small and dynamic.
Participative: The leader listens to everyone's ideas and suggestions. This style is best for small organizations where everyone feels valued.
What role does a manager have in a company's success?
The role of a manager varies from one industry to another.
Managers generally oversee the day-today operations of a business.
He/she is responsible for ensuring that the company meets all its financial obligations and produces the goods or services customers want.
He/she will ensure that employees follow all rules and regulations, and adhere to quality standards.
He/she plans and oversees marketing campaigns.
How does Six Sigma work
Six Sigma uses statistical analysis to find problems, measure them, analyze root causes, correct problems, and learn from experience.
The first step in solving a problem is to identify it.
The data is then analyzed and collected to identify trends.
The problem can then be fixed by taking corrective measures.
Final analysis of data is done to determine if the problem has been solved.
This cycle continues until there is a solution.
Statistics
- The profession is expected to grow 7% by 2028, a bit faster than the national average. (wgu.edu)
- 100% of the courses are offered online, and no campus visits are required — a big time-saver for you. (online.uc.edu)
- Our program is 100% engineered for your success. (online.uc.edu)
- As of 2020, personal bankers or tellers make an average of $32,620 per year, according to the BLS. (wgu.edu)
- The average salary for financial advisors in 2021 is around $60,000 per year, with the top 10% of the profession making more than $111,000 per year. (wgu.edu)
External Links
How To
How can Lean Manufacturing be done?
Lean Manufacturing uses structured methods to reduce waste, increase efficiency and reduce waste. These processes were created by Toyota Motor Corporation, Japan in the 1980s. The main goal was to produce products at lower costs while maintaining quality. Lean manufacturing is about eliminating redundant steps and activities from the manufacturing process. It is composed of five fundamental elements: continuous improvement; pull systems, continuous improvements, just-in–time, kaizen, continuous change, and 5S. Pull systems allow customers to get exactly what they want without having to do extra work. Continuous improvement involves constantly improving upon existing processes. Just-in–time refers when components or materials are delivered immediately to their intended destination. Kaizen stands for continuous improvement. Kaizen can be described as a process of making small improvements continuously. Five-S stands for sort. It is also the acronym for shine, standardize (standardize), and sustain. These five elements are used together to ensure the best possible results.
Lean Production System
Six key concepts form the foundation of the lean production system:
-
Flow - focus on moving material and information as close to customers as possible;
-
Value stream mapping- This allows you to break down each step of a process and create a flowchart detailing the entire process.
-
Five S's - Sort, Set In Order, Shine, Standardize, and Sustain;
-
Kanban - use visual signals such as colored tape, stickers, or other visual cues to keep track of inventory;
-
Theory of Constraints - Identify bottlenecks in the process, and eliminate them using lean tools such kanban boards.
-
Just-intime - Order components and materials at your location right on the spot.
-
Continuous improvement - incremental improvements are made to the process, not a complete overhaul.