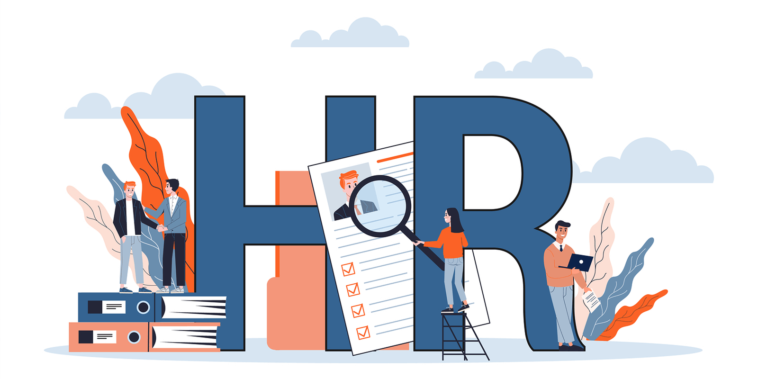
Crisis managers must have several skills. An effective leader can spot a crisis before its worst. In a slow-moving crisis, the effects may not be apparent until later. The best leadership styles recognize problems early. They study world events that may affect their organization, keep abreast of changing customer attitudes, and work with crisis managers to resolve the crisis as quickly as possible. A skilled crisis manager can assist a company in managing a crisis while ensuring normal business operations continue.
Priorities for crisis managers
Priorities for crisis managers must be clearly and precisely defined. A team should include people who can think clearly and take calm decisions. A team must also be made up of detail-oriented, process-oriented people. It is important that there is a clear line of command. It is important that the team receives proper training to perform their assigned tasks. In case of a crisis, the team should be restructured based on the needs of the crisis.
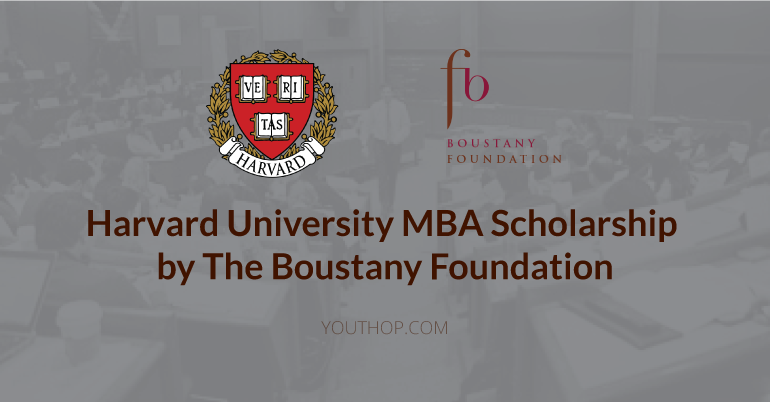
Characteristics of crisis management specialists
The right combination of experience and skill is essential to succeed as a crisis management specialist. Professionals in this field should have a lot of experience and be highly skilled. They also need to be competent at communicating and gathering input. Additionally, they should be able to actively listen. This type of person should be able to handle chaos and stress while remaining calm and focused. They should also be able work well with people from different departments and different roles.
Techniques that crisis managers use
A crisis manager can employ many strategies to handle a critical situation. It takes planning and preparation to manage crisis situations. The resilience concept is what top crisis managers use to guide their actions. It refers to being able to bounce back quickly after a difficult situation, and also to being vulnerable to potentially dangerous events. Top managers have excellent memory, are quick to take decisions and respond quicker. Additionally, top managers embrace vulnerability. This allows them to prepare for crisis before it happens.
Effect of crisis on organization
The Impact of Crisis on an Organization examines the ways in which a business can be damaged during a crisis and how it can be prevented or mitigated. This book examines factors that impact the value of an organisation and the possible consequences that a crisis may have on its viability or reputation. All commercial companies operate in a digital age. Trust is low and there are high expectations for good governance. Complex communication is required between companies and stakeholders. The traditional target audience is fragmented into smaller social communities. Issues can be quickly resolved.
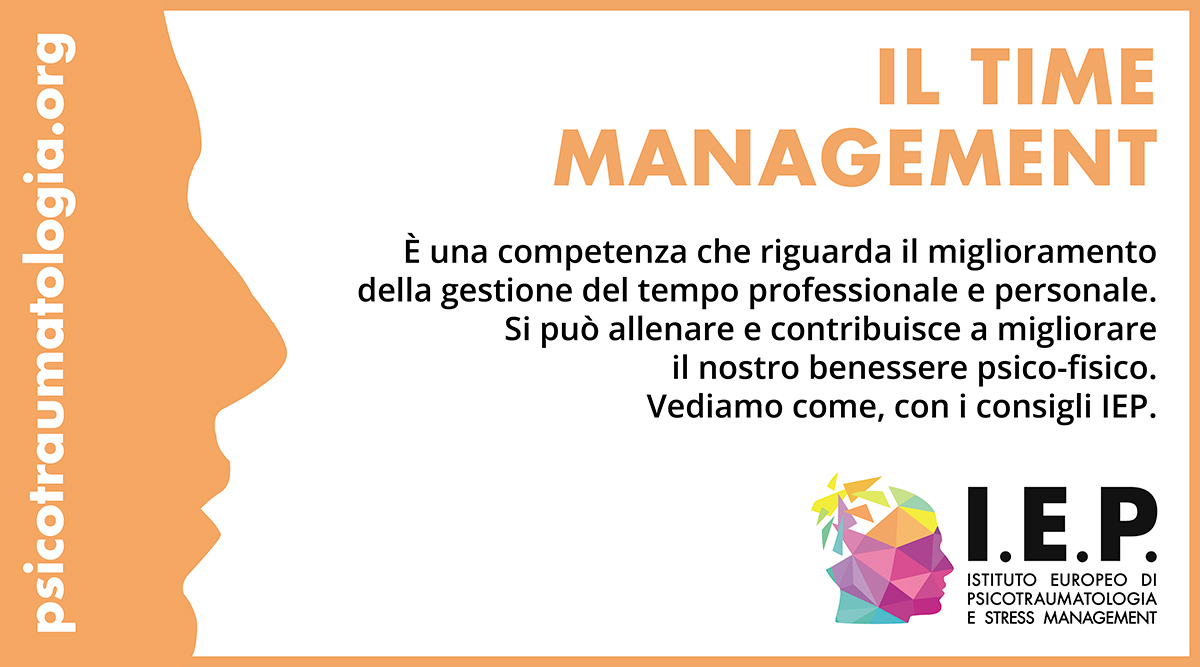
Management skills are required by crisis managers
A good crisis manager will have several important skills, including communication. These skills are vital for the management of any crisis no matter how big or small. The manager must be able communicate effectively and clearly to solve the problem as quickly and as smoothly as possible. These skills require that the manager is calm, can make quick decisions, and be able delegate tasks. These skills combine to increase the likelihood of crisis managers achieving a positive outcome.
FAQ
Six Sigma is so well-known.
Six Sigma can be implemented quickly and produce impressive results. It provides a framework that allows for improvement and helps companies concentrate on what really matters.
What are some common management mistakes?
Sometimes managers make it harder for their employees than is necessary.
They might not give enough support and delegate the right responsibilities to their staff.
A majority of managers lack the communication skills needed to motivate their team and lead them.
Managers set unrealistic expectations and make it difficult for their team.
Managers may attempt to solve all problems themselves, rather than delegating it to others.
What is Six Sigma and how can it help you?
It is a way to improve quality that places emphasis on customer service and continuous learning. It is a method that eliminates defects using statistical techniques.
Motorola developed Six Sigma in 1986 to help improve its manufacturing processes.
The idea spread quickly throughout the industry, and today, many organizations are using six sigma methods to improve product design, production, delivery, and customer service.
What is the difference in leadership and management?
Leadership is about inspiring others. Management is all about controlling others.
A leader inspires his followers while a manager directs the workers.
Leaders motivate people to succeed; managers keep workers on track.
A leader develops people; a manager manages people.
How does a manager develop his/her management skills?
Through demonstrating good management skills at every opportunity
Managers should monitor the performance and progress of their subordinates.
If you notice your subordinate isn't performing up to par, you must take action quickly.
You should be able pinpoint what needs to improve and how to fix it.
It can sometimes seem difficult to make business decisions.
Complex systems with many moving parts are the hallmark of businesses. It is difficult for people in charge of businesses to manage multiple priorities simultaneously and also deal with uncertainty.
Understanding how these factors impact the whole system is key to making informed decisions.
This requires you to think about the purpose and function of each component. Next, consider how each piece interacts with the others.
You should also ask yourself if there are any hidden assumptions behind how you've been doing things. If they don't, you may want to reconsider them.
Try asking for help from another person if you're still stuck. You might find their perspective is different from yours and they may have insight that can help you find the solution.
Statistics
- Our program is 100% engineered for your success. (online.uc.edu)
- As of 2020, personal bankers or tellers make an average of $32,620 per year, according to the BLS. (wgu.edu)
- The BLS says that financial services jobs like banking are expected to grow 4% by 2030, about as fast as the national average. (wgu.edu)
- Your choice in Step 5 may very likely be the same or similar to the alternative you placed at the top of your list at the end of Step 4. (umassd.edu)
- The average salary for financial advisors in 2021 is around $60,000 per year, with the top 10% of the profession making more than $111,000 per year. (wgu.edu)
External Links
How To
How can Lean Manufacturing be done?
Lean Manufacturing methods are used to reduce waste through structured processes. These processes were created by Toyota Motor Corporation, Japan in the 1980s. The main goal was to produce products at lower costs while maintaining quality. Lean manufacturing emphasizes removing unnecessary steps from the production process. It consists of five basic elements: pull systems, continuous improvement, just-in-time, kaizen (continuous change), and 5S. It is a system that produces only the product the customer requests without additional work. Continuous improvement is constantly improving upon existing processes. Just-in-time is when components and other materials are delivered at their destination in a timely manner. Kaizen refers to continuous improvement. It is achieved through small changes that are made continuously. Fifth, the 5S stand for sort, set up in order to shine, standardize, maintain, and standardize. To achieve the best results, these five elements must be used together.
Lean Production System
Six key concepts are the basis of lean production:
-
Flow - focus on moving material and information as close to customers as possible;
-
Value stream mapping is the ability to divide a process into smaller tasks, and then create a flowchart that shows the entire process.
-
Five S’s - Sorted, In Order. Shine. Standardize. And Sustain.
-
Kanban – visual signals like colored tape, stickers or other visual cues are used to keep track inventory.
-
Theory of constraints: Identify bottlenecks and use lean tools such as kanban boards to eliminate them.
-
Just-in time - Get components and materials delivered right at the point of usage;
-
Continuous improvement - Make incremental improvements rather than overhauling the entire process.