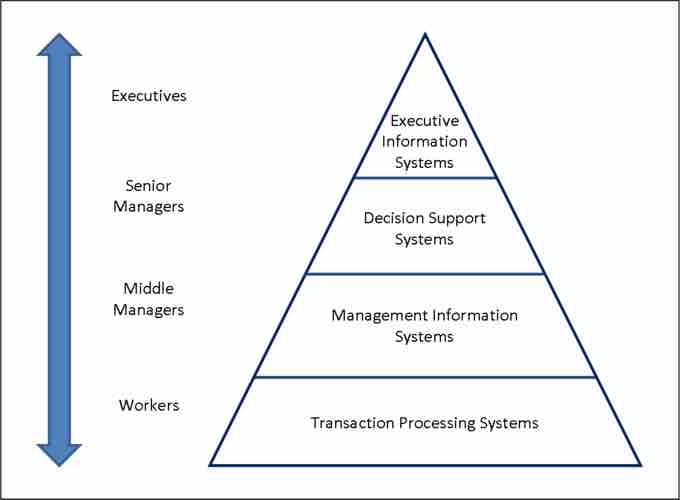
A supply chain framework is a process to help companies make better business decisions. Communication is a key component. The rational process includes five steps: identifying the problem, understanding its potential solutions and gathering data. Next, analyze the possible outcomes. Finally, choose the best solution and put it into practice.
Supply chain drivers are key factors in inventory
Management of inventory is a key function of manufacturing firms. It allows for the supply of the correct product at the right moment at the right place. This function is increasingly important in a global economy, when a product can be manufactured anywhere. It is crucial to a company’s efficiency as well as responsiveness.
Inventory management requires the ability to anticipate customer needs and respond to changing conditions. The data that companies share about their production schedules or inventory levels must be shared with their partners. This allows them quickly respond to market changes. Inventory management is critical in today's highly dynamic world to ensure companies meet their customers needs.
Collaboration and communication is key
Communication and collaboration are key ingredients in today's fast-paced global supply chain. These relationships can help companies increase their ability to meet new market demands and differentiate themselves. Collaboration can be a great way for organisations to gain new resources, increase their capabilities and remain competitive. It can also help businesses expand their customer base.
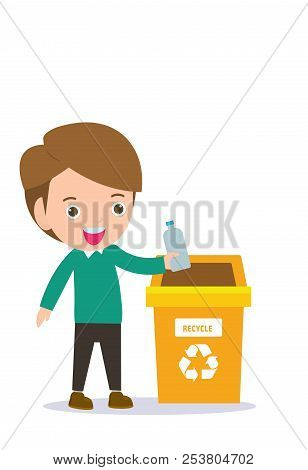
Trust and high levels of commitment are key to successful collaboration relationships. A culture that encourages collaboration is also essential.
Financial attributes
A framework for supply chain decision making must consider both financial and ecological factors. It is important to increase the cash flow throughout the supply chain. These attributes will impact the working capital levels at both the suppliers and the buyers. This is significant because cash flow directly relates to suppliers' level of finance leverage, capital access, and financial stability. SCF is improved through financial attributes. Additionally, they play an important role when it comes to investment in green technologies and policy. Additionally, environmental and financial policies are directly related to social values.
The framework proposed provides a framework for decision-making in the supply chain and interlinks all components. It also provides open research questions. The framework is universally applicable to all industries and sectors.
Attributes to the environment
The growing acceptance of environmental concerns is driving the trend to include environmental attributes in supply chain decision making. Companies often adopt environmental performance measurements for a variety of reasons, including to identify potential opportunities for improvement and achieve better co-operation with suppliers. Although environmental performance measurement is a complicated issue, both the parties and the environment can reap substantial benefits.
These are financial, environmental, and social criteria. The framework should help enterprises select the most environmentally-friendly suppliers for their business. It should also assist them in adopting environmental practices within their companies.
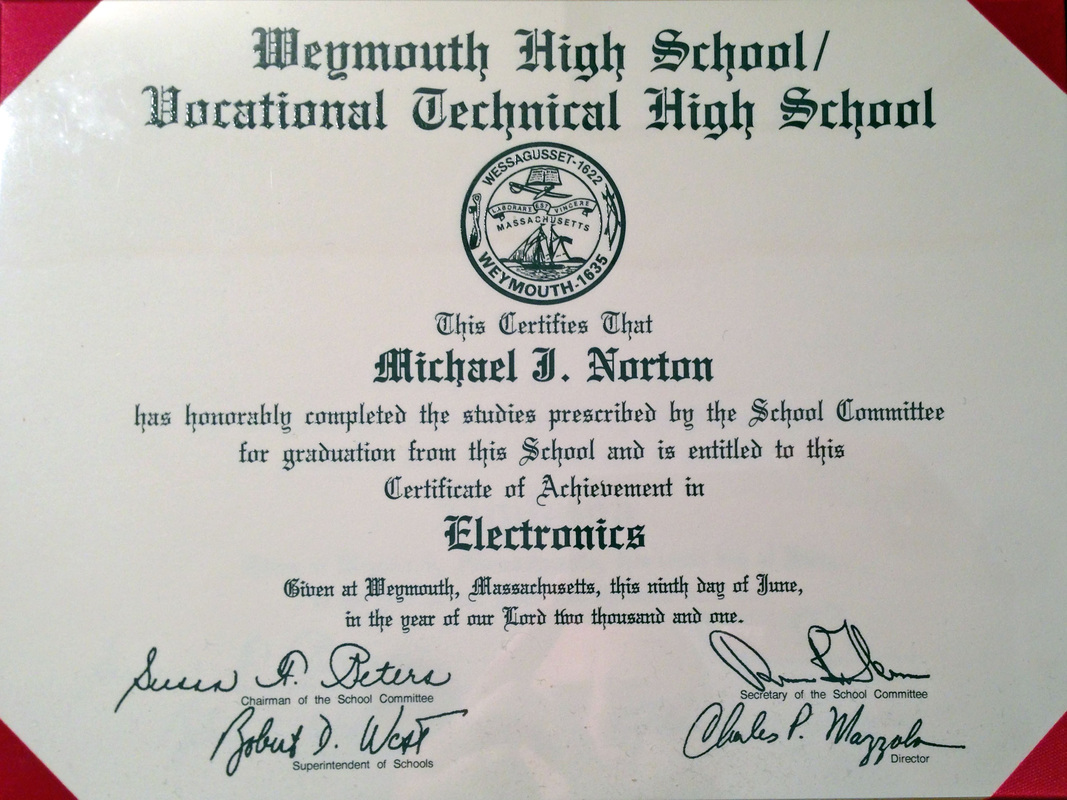
Prioritizing
Demand Prioritization is an important aspect of supply chain decision making. It is critical to identify the highest-profitable demand and allocate resources to meet it. In some cases, this means delaying other orders or offering a substitute product. To manage risk, all levels of management should be made aware of the process and it should be documented. While the supply side should input costs, the demand side should have more information about customers' needs and goals.
The next step of the process is to identify and secure potential raw materials, capacity, and labor pool opportunities. A company might look at alternative sources for raw materials that offer lower prices and longer lead times. However, it should also be noted that this can erode margin and working capital. Similar to the above, you may need to expand your operations during off-peak hours and to secure additional transport capacity.
FAQ
What does the term "project management” mean?
It refers to the management of activities related to a project.
Our services include the definition of the scope, identifying requirements, preparing a budget, organizing project teams, scheduling work, monitoring progress and evaluating the results before closing the project.
What is Six Sigma?
Six Sigma uses statistical analysis for problems to be found, measured, analyzed root causes, corrected, and learned from.
First, identify the problem.
The data is then analyzed and collected to identify trends.
Then corrective actions are taken to solve the problem.
Finally, data is reanalyzed to determine whether the problem has been eliminated.
This cycle will continue until the problem is solved.
How does a manager motivate their employees?
Motivation refers to the desire or need to succeed.
It is possible to be motivated by doing something you enjoy.
Or you can get motivated by seeing yourself making a contribution to the success of the organization.
You might find it more rewarding to treat patients than to study medical books if you plan to become a doctor.
Another source of motivation is within.
One example is a strong sense that you are responsible for helping others.
You may even find it enjoyable to work hard.
Ask yourself why you feel so motivated.
Then, consider ways you could improve your motivation.
What is the difference between a project and a program?
A project is temporary, while a program lasts forever.
A project is usually defined by a clear goal and a set deadline.
It is often carried out by a team of people who report back to someone else.
A program usually has a set of goals and objectives.
It is often implemented by one person.
What are management concepts, you ask?
Management concepts are the fundamental principles and practices that managers use when managing people and their resources. They cover topics such as job descriptions and performance evaluations, human resource policies, training programs, employee motivation, compens systems, organizational structure, among others.
What are the five management processes?
These five stages are: planning, execution monitoring, review and evaluation.
Setting goals for the future is part of planning. Planning includes setting goals for the future.
Execution happens when you actually do the plan. You need to make sure they're followed by everyone involved.
Monitoring is the process of evaluating your progress toward achieving your objectives. Monitoring should include regular reviews of performance against goals and budgets.
Review events take place at each year's end. They give you an opportunity to review the year and assess how it went. If not there are changes that can be made to improve the performance next year.
Following the annual review, evaluation is done. It helps identify which aspects worked well and which didn't. It also provides feedback on how well people performed.
What role can a manager fill in a company’s management?
Different industries have different roles for managers.
In general, a manager controls the day-to-day operations of a company.
He/she ensures the company meets its financial commitments and produces goods/services that customers demand.
He/she will ensure that employees follow all rules and regulations, and adhere to quality standards.
He/she is responsible for the development of new products and services, as well as overseeing marketing campaigns.
Statistics
- This field is expected to grow about 7% by 2028, a bit faster than the national average for job growth. (wgu.edu)
- Our program is 100% engineered for your success. (online.uc.edu)
- UpCounsel accepts only the top 5 percent of lawyers on its site. (upcounsel.com)
- As of 2020, personal bankers or tellers make an average of $32,620 per year, according to the BLS. (wgu.edu)
- 100% of the courses are offered online, and no campus visits are required — a big time-saver for you. (online.uc.edu)
External Links
How To
How do I do the Kaizen Method?
Kaizen means continuous improvement. This Japanese term refers to the Japanese philosophy of continuous improvement that emphasizes incremental improvements and constant improvement. It's a process where people work together to improve their processes continuously.
Kaizen is one the most important methods of Lean Manufacturing. Employees responsible for the production line should identify potential problems in the manufacturing process and work together to resolve them. This way, the quality of products increases, and the cost decreases.
Kaizen is an approach to making every worker aware and alert to what is happening around them. Correct any errors immediately to avoid future problems. So, if someone notices a problem while working, he/she should report it to his/her manager.
When doing kaizen, there are some principles we must follow. Start with the end product, and then move to the beginning. For example, if we want to improve our factory, we first fix the machines that produce the final product. Then, we fix the machines that produce components and then the ones that produce raw materials. And finally, we fix the workers who work directly with those machines.
This method is known as kaizen because it focuses upon improving every aspect of the process step by step. Once the factory is fixed, we return to the original site and work our way back until we get there.
To implement kaizen in your business, you need to find out how to measure its effectiveness. There are many methods to assess if kaizen works well. Another way to determine if kaizen is working well is to look at the quality of the products. Another way to find out how productive your company has been since you implemented kaizen is to measure the increase in productivity.
To determine if kaizen is effective, you should ask yourself why you chose to implement kaizen. It was because of the law, or simply because you wanted to save some money. You really believed it would make you successful?
Suppose you answered yes to any of these questions, congratulations! You're now ready to get started with kaizen.