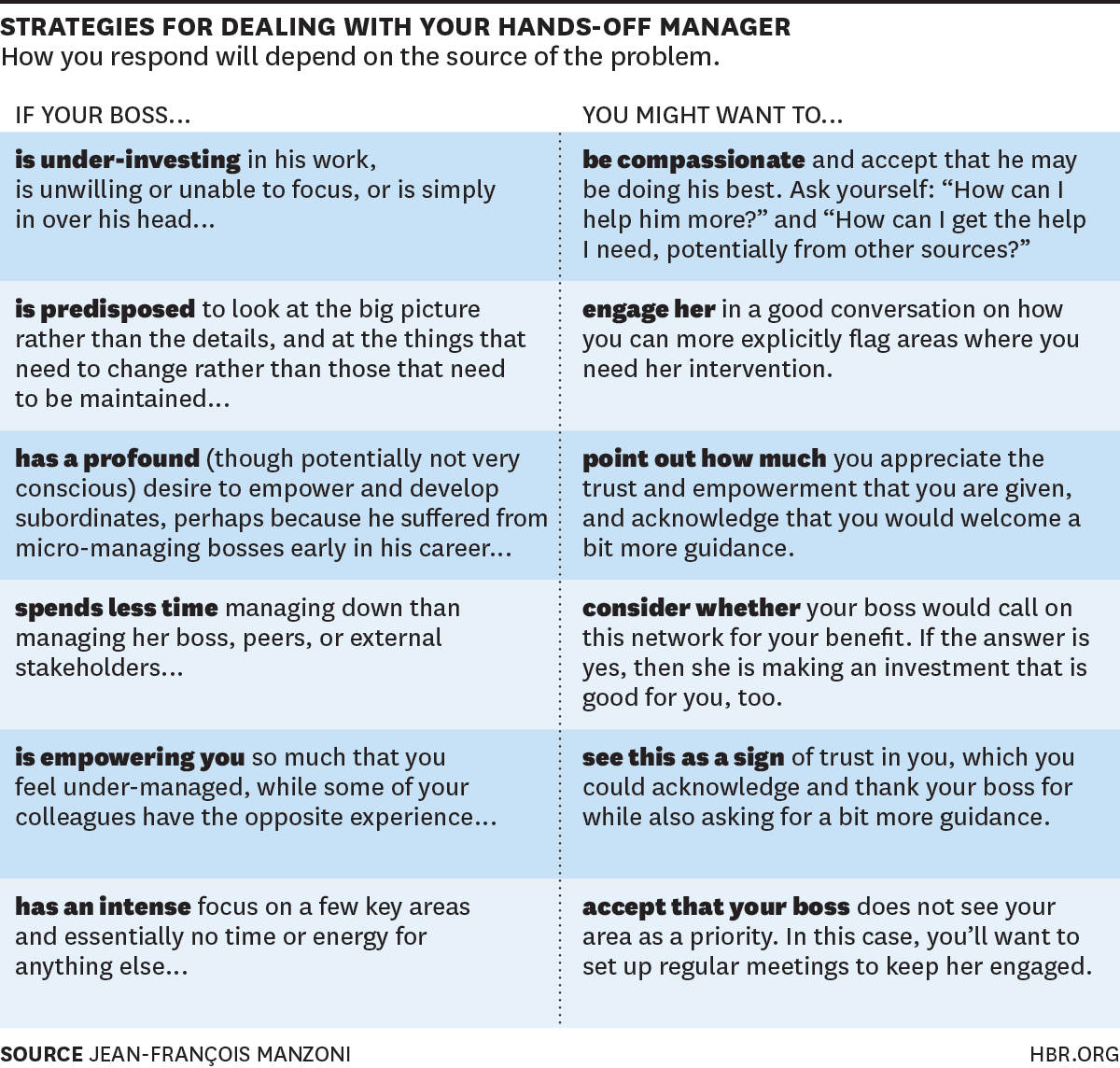
If you're a lover clean environments, Allied Waste Industries, Inc. is a company you've probably heard about. This Fortune 500 firm operated solid waste collection facilities, recycling facilities, landfills, and landfills. It was one of the most prominent companies in the US' solid waste industry. In recent years, it has experienced several challenges that have pushed it to change its business model. Allied Waste, despite these setbacks, is still a viable company providing convenient and clean services.
Allied Waste Industries, Inc.
Allied Waste Industries, Inc. was a Fortune 500 company headquartered in Phoenix, Arizona. It was a vertically-integrated company that owned solid waste collection businesses, landfills, and recycling facilities. The company offered solid-waste solutions and recycling services for cities and businesses in the United States. The company was a leader for many years in the solid-waste industry. However, it shut down in 2012 and the employees are now burdened with huge debts.
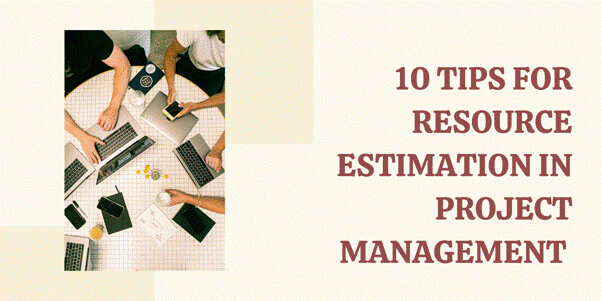
The company bought two Illinois-based waste companies in 1993. National Scavenger Service, Inc., operated landfills and transfer stations. The first company was National Scavenger Service, Inc. The second company, R.I8, became a waste company in New Mexico. After a variety of acquisitions and mergings, Allied Waste was able grow into several states. The company is now the world's largest waste management company.
Lessey & Ivan were promoted to vice chairman and CFO following the acquisition. Ferreira, who had 20 years of experience, was the first president at AWI. However, Lessey left in October 1989 to go back to the venture capital industry. Daniel J. Ivan took over as AWI's president. Despite recent turmoil, AWI managed to maintain its merger and acquisition programs.
Allied Waste Landfill Holdings, Inc.
Allied Waste is an American company that has landfills across the United States. Bruce Lessey established the company in 1987. After years of service in Houston, he started purchasing other companies that dealt with waste. In 1989, his business was facing financial problems. Roger Ramsey, who co-founded Browning-Ferris Industries, Inc., provided assistance. Houston Partners, LP also owned a piece of Allied Waste. Lessey stated that Ramsey brought with him the knowledge and experience from his own business to Allied Waste's board in August 1989.
Allied Waste has approximately 41,000 employees. The company is vertically-integrated and has a decentralized leadership structure. Its subsidiaries own and operate transfer stations, recycling facilities, landfills, and recycling plants. It is owned four private equity funds and serves more than 10 million clients in 39 states. It has 355 collection companies, and 181 transfer stations. It has 167 landfills in operation and 65 recycling facilities. Delaware is where the company is located.
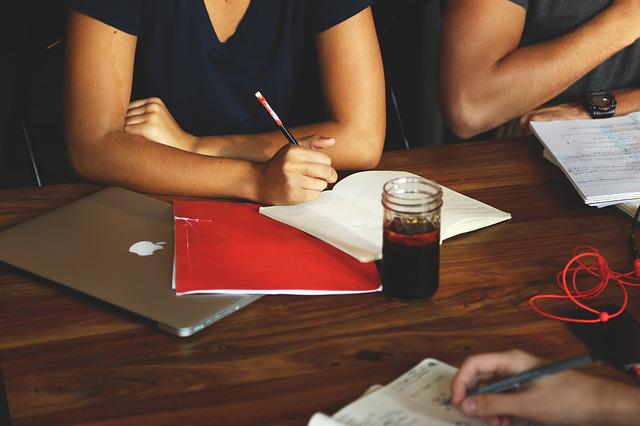
The company was the 2nd-largest solid waste disposal firm in the United States as of 2002. The company reported a profit for the first quarter 2002, as opposed to nearly $36million in 2001. To meet the company's rapid expansion, Allied spent money to upgrade its infrastructure. The number of locations was increased from two to four to twelve to 12 regions and to 58 districts. Allied Waste's internalization rate grew to 67 per cent in 2001.
FAQ
What are management concepts, you ask?
Management concepts are the principles and practices used by managers to manage people, resources. They cover topics like job descriptions (job descriptions), performance evaluations, training programmes, employee motivation and compensation systems.
What are the five management process?
Planning, execution, monitoring and review are the five stages of any business.
Setting goals for the future is part of planning. Planning involves defining your goals and how to get there.
Execution occurs when you actually carry out the plans. You need to make sure they're followed by everyone involved.
Monitoring is the process of evaluating your progress toward achieving your objectives. This should involve regular reviews of performance against targets and budgets.
Review events take place at each year's end. They provide an opportunity to assess whether everything went well during the year. If not, changes may be made to improve the performance next time around.
After the annual review is complete, evaluations are conducted. It helps identify which aspects worked well and which didn't. It provides feedback about how people perform.
What is TQM and how can it help you?
The quality movement was born during the industrial revolution when manufacturing companies realized they could not compete on price alone. They needed to improve the quality and efficiency of their products if they were to be competitive.
Management realized the need to improve and created Total Quality Management, which focused on improving all aspects within an organization's performance. It included continuous improvement, employee involvement and customer satisfaction.
What is the difference between project and program?
A project is temporary while a programme is permanent.
A project typically has a defined goal and deadline.
It is often performed by a team of people, who report back on someone else.
A program will usually have a set number of goals and objectives.
It is usually implemented by a single person.
Statistics
- As of 2020, personal bankers or tellers make an average of $32,620 per year, according to the BLS. (wgu.edu)
- This field is expected to grow about 7% by 2028, a bit faster than the national average for job growth. (wgu.edu)
- The BLS says that financial services jobs like banking are expected to grow 4% by 2030, about as fast as the national average. (wgu.edu)
- Hire the top business lawyers and save up to 60% on legal fees (upcounsel.com)
- 100% of the courses are offered online, and no campus visits are required — a big time-saver for you. (online.uc.edu)
External Links
How To
How can you implement Quality Management Plan (QMP).
QMP, which was introduced by ISO 9001:2008, is a systematic approach to improving products, services, and processes through continuous improvement. It helps to improve customer satisfaction and product/service quality by continuously measuring, analyzing, controlling and improving.
QMP is a common method to ensure business performance. QMP helps improve production, service delivery and customer relationships. QMPs must include all three elements - Products, Services, and Processes. If the QMP focuses on one aspect, it is called "Process." QMP. The QMP that focuses on a Product/Service is called a "Product." QMP. QMP is also used to refer to QMPs that focus on customer relations.
Two main elements are required for the implementation of a QMP. They are Scope and Strategy. These are the following:
Scope is what the QMP covers and how long it will last. If your organization wishes to implement a QMP lasting six months, the scope will determine the activities during the first six month.
Strategy: This describes the steps taken towards achieving the goals set forth in the scope.
A typical QMP is composed of five phases: Planning Design, Development, Implementation and Maintenance. Each phase is explained below:
Planning: This stage is where the QMP objectives are identified and prioritized. To understand the expectations and requirements of all stakeholders, the project is consulted. Next, you will need to identify the objectives and priorities. The strategy for achieving them is developed.
Design: This stage is where the design team creates the vision, mission and strategies necessary for successful implementation of QMP. These strategies are executed by creating detailed plans.
Development: Here, the team develops the resources and capabilities that will support the successful implementation.
Implementation is the actual implementation of QMP according to the plans.
Maintenance: This is an ongoing process to maintain the QMP over time.
Additional items must be included in QMP.
Stakeholder Engagement: It is crucial for the QMP to be a success. They must be involved in all phases of the QMP's development, planning, execution, maintenance, and design.
Project Initiation: The initiation of any project requires a clear understanding of the problem statement and the solution. The initiator must know the reason they are doing something and the expected outcome.
Time Frame: The time frame of the QMP is very critical. For a short time, you can start with the simple version of the QMP. However, if you have a long-term commitment, you may require more elaborate versions.
Cost Estimation is another important aspect of the QMP. You can't plan without knowing how much money it will cost. Before you start the QMP, it is important to estimate your costs.
QMPs are not only a document, but also a living document. This is the most important aspect of QMPs. It can change as the company grows or changes. It should therefore be reviewed frequently to ensure that the organization's needs are met.